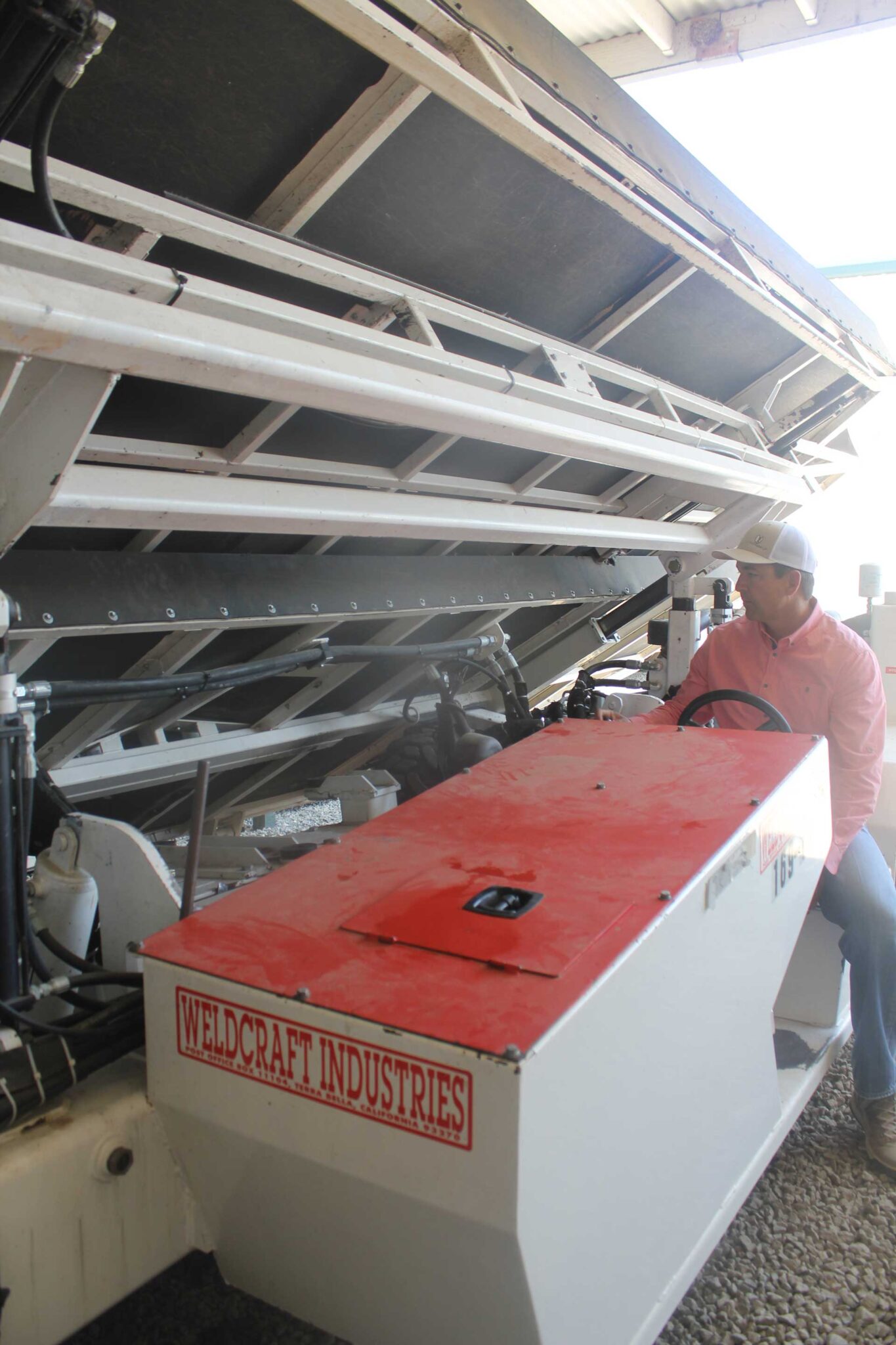
Researchers are looking for ways to improve pistachio harvest efficiency by shaking more nuts off pistachio trees while reducing stress on the trees and energy use at harvest.
The pistachio industry, dealing with very large pistachio trees at harvest, current harvest machine design and machine operator limitations, are facing major issues at harvest. As a relatively new tree nut crop in California, there has been limited research on efficiency of mechanical harvesting of pistachio nuts both in terms of engineering design and tree physiology and effects of shaking on tree health and yield.
Improving Nut Removal
Good nut removal from larger pistachio trees continues to be a challenge for pistachio growers as orchards age, said Bob Klein, manager of the California Pistachio Research Board (CPRB). Size of the tree is not the only factor, Klein said. The newer varieties of pistachio that have been planted, including Golden Hills, Lost Hills and Kalehghouchi, differ from Kerman in terms of wood strength, resilience and flexibility. Developing a machine that can adapt to the different factors, such as size and variety, would improve nut removal, Klein said.
UC Merced mechanical engineering professor Reza Ehsani is conducting CPRB-funded studies to address pistachio harvest efficiency and the effects of mechanical harvesting on trees. Ehsani, who formerly worked on designing mechanical harvest machines for citrus in Florida, said there has been little change in the fundamental design of pistachio harvesting machines since the first pistachio trees were harvested mechanically in the early 1970s.
As part of his research, Ehsani conducted field tests at Wonderful Pistachio orchards in Lost Hills in 2019. Three categories of trees were chosen based on trunk circumference size: small circumference less than 25 inches; medium circumference between 25 inches and 37.7 inches; and large circumference greater than 37.7 inches. These sizes were selected so that trunk diameter would be less than 8 inches for small, between 8 and 12 inches for medium, and greater than 12 inches for large trees. Ten trees were selected for each category resulting in a total of 30 trees for the experiment.
The results of this trial proved that the optimal shaking frequency is different for different sizes of trees. He also found it is possible to install a sensor on the trunk shaker to measure the trunk size during the harvest and suggest the optimal shaking pattern to the operator.
There is a lack of data on machine harvesting efficiency, Ehsani said, but to improve efficiency, it is important to understand all the factors involved—trees, machines and operators. The goal of pistachio harvest, he said, is to maximize removal of nuts with the least damage to trees while reducing the energy needed, balancing cost with leaving nuts on the tree.
Tulare County pistachio grower Larry Wilkinson said one of the biggest factors in good nut removal at harvest is an experienced machine operator. Wilkinson, who serves on the governmental affairs committee for American Pistachio Growers, said due to machine design, operators have a sight challenge as they approach a tree and can’t always determine trunk size. They must also work in sync with the other operator. Wilkinson said it can take half a harvest season for a new machine operator to become proficient with a shaker.
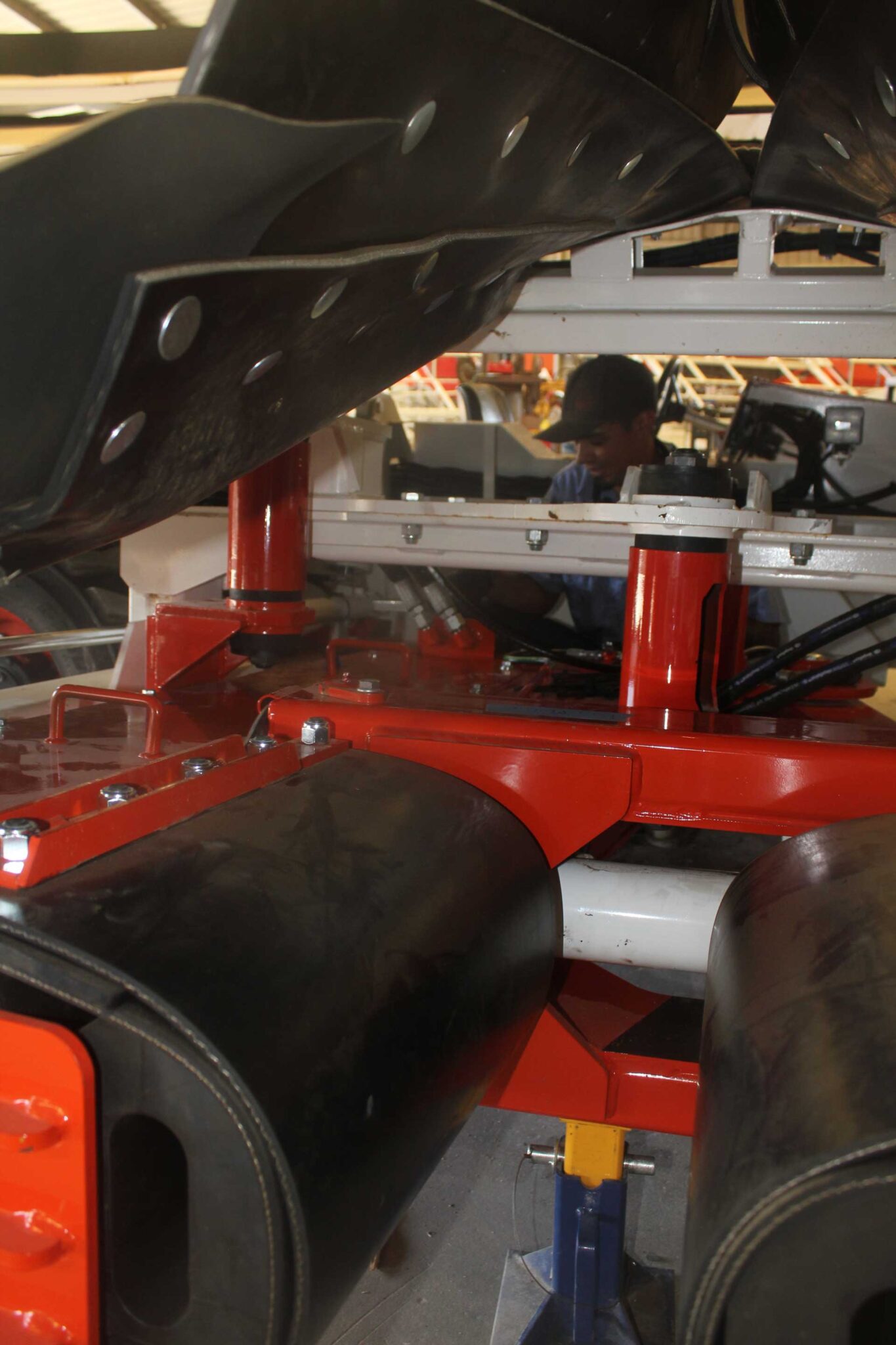
Current Shaker Limitations
Orchard design and tree spacing affect the type and size of machine that can be used in an orchard. In most cases, the harvesting machine accommodates the existing orchard, but Ehsani said that better results can be achieved if the harvesting machine and orchard design can be done together. The way in which young pistachio trees are trained can have an effect on future nut removal. More research is needed to determine best pruning practices for optimal harvest, Ehsani said.
In mechanical harvesting using a trunk shaker, the clamping force, clamping height, shaker amplitude and frequency are key factors affecting nut removal and tree damage. All these factors change with tree size and structure. Ehsani said clamp height is important because lower net power is required for higher attachment points due to the elevated elastic deformation of the trunk at such attachment points. Clamping point can be limited by available trunk height. Clamp force is another factor. Too much force can cause damage to the tree, but a looser grip will not transfer enough force for maximum nut removal. Clamps are padded to prevent damage to trees, but Ehsani said the padding also can reduce energy transfer.
Shaking older and larger trees is more difficult than smaller trees for two reasons. The first is that the overall size and mass of the tree requires more energy to shake. Second, the trees have larger and longer roots which will dissipate much more of the shaking energy. Larger canopies can also dampen the energy and more power is needed for an optimal shake. Young trees are more vulnerable to shaker damage. Ehsani said he would also like to have a shaking option for trees just coming into production that remove nuts but not harm trees.
More research is needed to find the optimal design and force pattern for shaker machines. Ehsani said in theory, the best shaking frequency for nut removal is a range of shaking frequencies around the natural frequency of a tree. The issue is that each tree, depending on its size and structure, has a slightly different natural frequency. Shaking trees at a frequency higher than the natural frequency could potentially cause severe damage to the tree.
Machine Learning from Experience
Then, there are operator limitations. Experience plays a role in machine performance as an experienced driver can achieve maximum nut removal, minimize tree damage and still cover ground. There will be expected drop off in operator performance as repeated motions and fatigue set in. Ehsani said his lab is developing a system that can monitor experienced drivers and record how they harvest trees. Using a machine learning technique, he said they hope to learn from experienced drivers and build a new control system based on their proficiency.
Shaker manufacturers have adopted a computer control system to create different shaking patterns by adjusting the magnitude of the shaking as a function of time. The on-board computer can store multiple shaking patterns and the operator can choose the most appropriate pattern, but deciding on the best pattern is often based on trial and error, and there are no instructions on how to choose the best pattern for each tree. This system cannot be linked to an external sensor which means there is no way to change the pattern using a smart external sensor.
Ehsani’s research is focused on development of harvesters capable of customizing the shaking parameters for each tree and to create a specific shaking system with the goal of maximizing nut removal while reducing tree damage. He said his laboratory team is also working on a shaking system to reduce the energy needed, allowing use of smaller engines on harvesting machines.
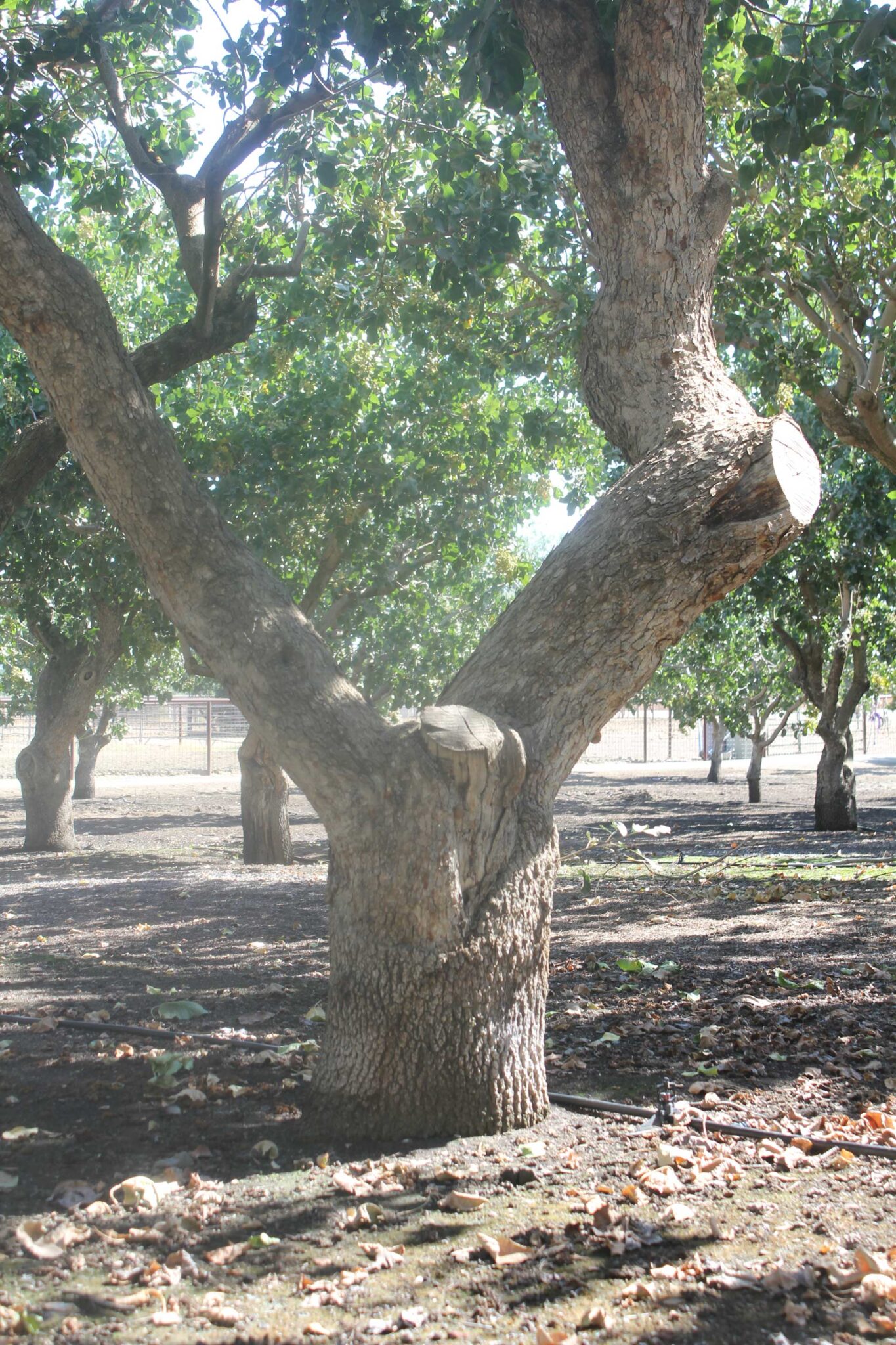