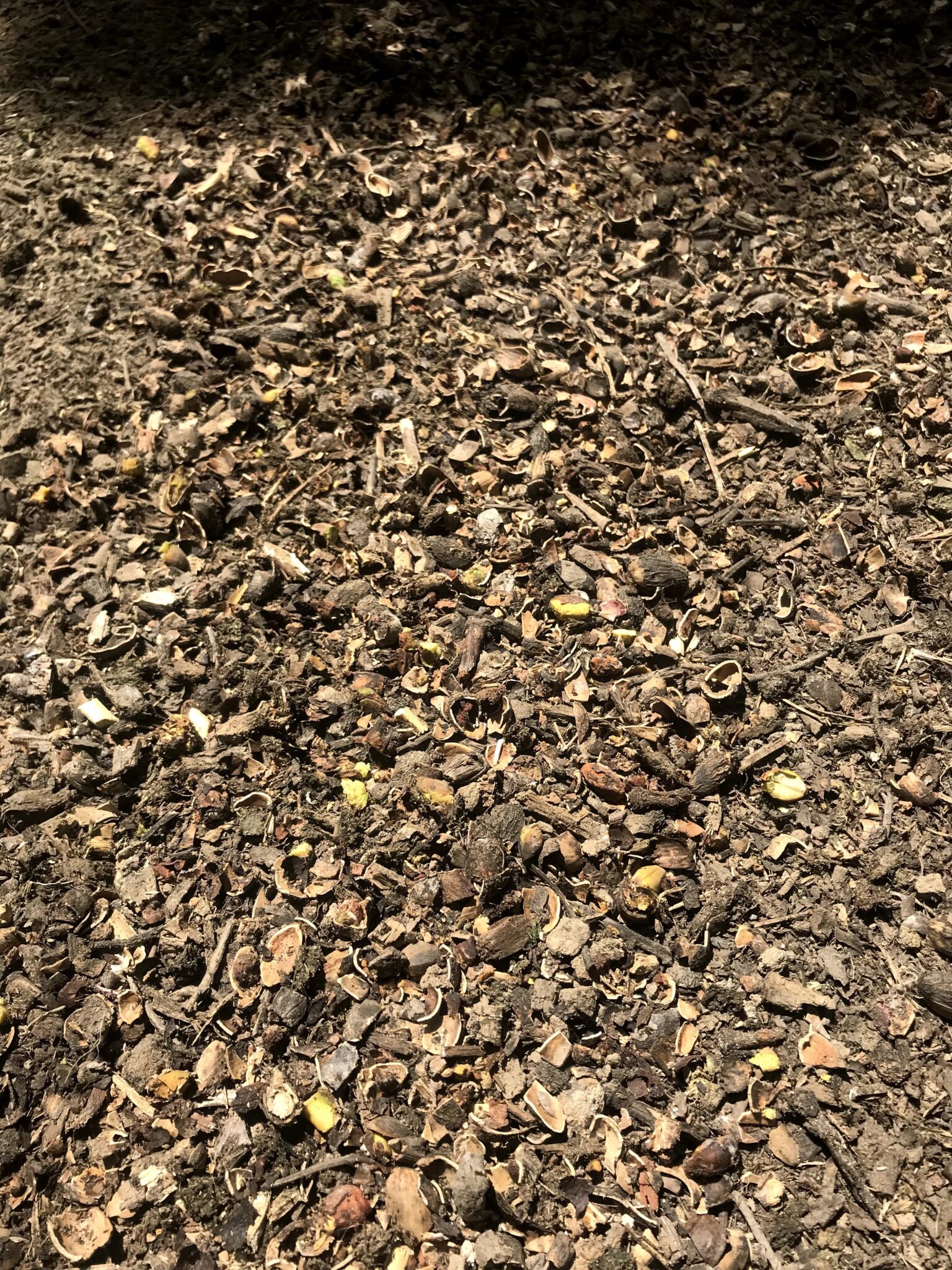
Overwintering NOW in pistachios are reliably difficult to deal with in comparison to almonds. But growers are looking at novel ways to destroy those downed mummies. By the fall of 2021, California pistachio growers may be able to custom-order a mummy grinder that could dramatically improve winter sanitation.
The grinder is the brainchild of two farmers and a metal fabricator who have gone outside the box to develop a solution to a problem that has plagued pistachio growers for decades: namely, how to destroy mummies, a major food source for the navel orangeworm (NOW).
After two years of testing, the mummy grinder is providing results that are surprising even the growers.
“We take biweekly trap counts in our orchards,” said James Nichols of Nichols Farms. “And in both the orchards that have mating disruption and those without mating disruption, we’ve seen a pretty drastic difference between the orchards that we ran this on.”
Nichols, whose family also operates a processing plant in Hanford, Calif., said he was getting trap counts in the 60s, 70s and 80s this past spring in orchards where he didn’t run the grinder. Where he ran the grinder, he was finding between zero and one moth per trap.
“It is certainly not the only tool in the toolbox, but from a nonchemical treatment standpoint, we are really excited about the fact that we’ve seen a lot of pressure reduction in our traps, and I think it is attributed to the lack of food source for the navel orangeworm,” Nichols said.
The Nichols mummy grinder, which they are calling a “Worminator,” has its origins in a conversation between Nichols and his shop manager, Richard Brock, after the farm suffered poor performances in 2016 and 2017 due to navel orangeworm.
Nichols said he remembers standing in an orchard with Brock looking at mummies on the orchard floor.
“I remember having a meeting out in one of the orchards, and we were looking at the leftover nuts from the previous harvest, and we were asking, ‘How can we get rid of these,’” he said.
“Jimmy (Nichols) said to me, ‘We need to come up with a different way of doing things,’” Brock said. “With our normal practice, we are probably getting 15-40% of the mummies. And he said, ‘Richard, I want to get 90-99% of them.’ So that is when we started looking at different alternatives to achieve that goal.”
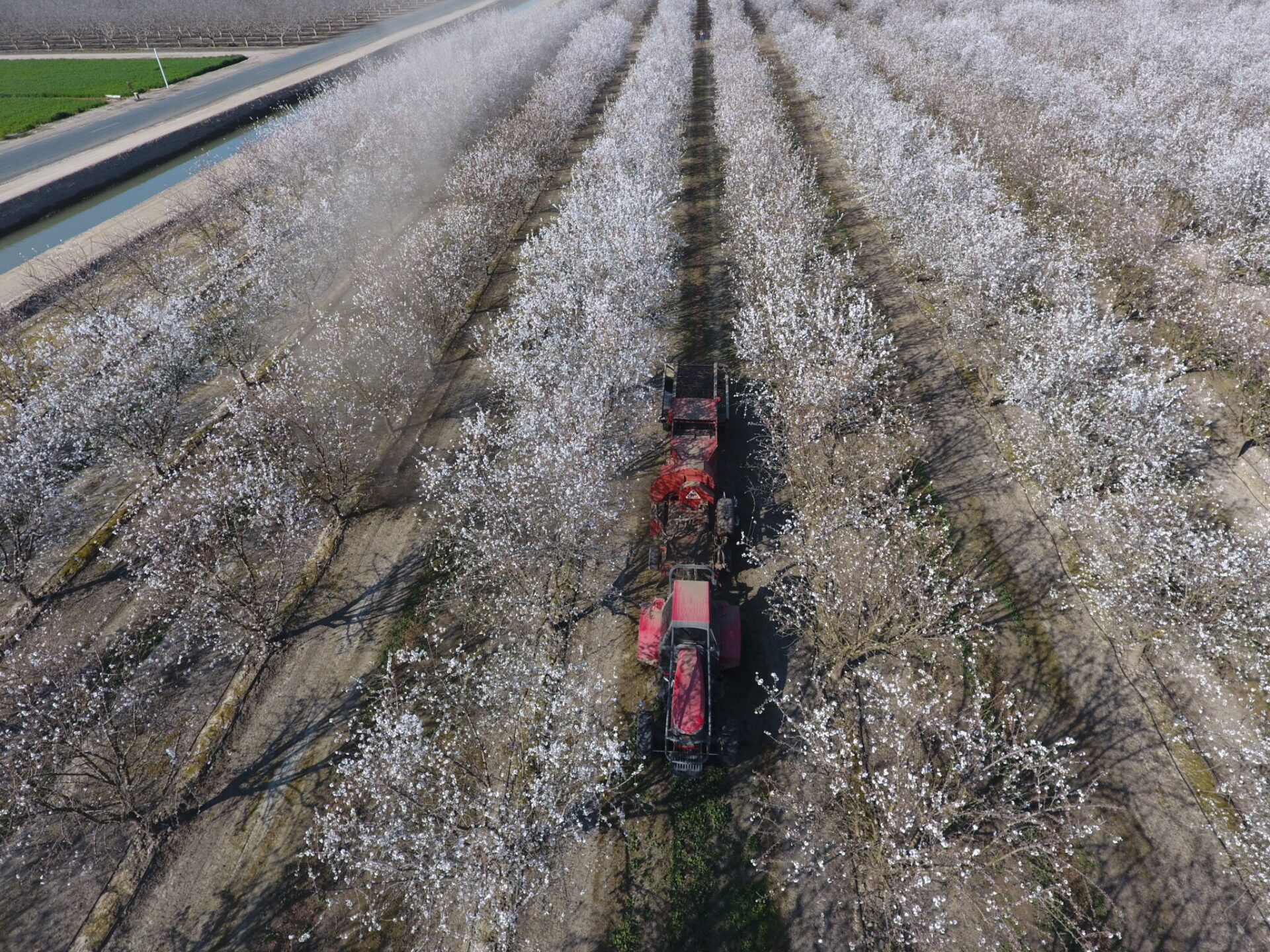
The High Cost of NOW
High navel orangeworm pressure in the 2016 and 2017 seasons cost Nichols Farms in three ways.
“It affected us at the grower level in that we weren’t receiving the premiums that we would have received if we sent in low-insect crop,” Nichols said. “It was slowing down the plant operations because it was requiring a lot more hand sorting. And it was asking a lot more from customer service, because we had quite a few complaints about finding navel orangeworm in our product.”
Nichols and Brock started their journey by realizing their best bet would be to gather the nuts in the center of rows with an almond sweeper and somehow remove them. Pistachios are innately difficult to dispose of in large part because of the hardness of their shell, so Brock’s first thought was to use a wood chipper to grind them. “But then we realized that wouldn’t grind the nuts fine enough,” Brock said.
The two eventually brought in Terry Kwast of Sawtelle & Rosprim in Corcoran, Calif., a fabricator who had worked with Brock’s father in the past.
Kwast suggested using an industrial grinder to grind the nuts, similar to one used in municipal sewage and waste systems to grind everything from agricultural byproducts and wooden pallets to surplus compact discs.
“When Richard came and asked me if I could help on this, one of the first thoughts that came to my mind was we needed a good, high-quality industrial shredder,” Kwast said. “And that is where we started. The rest of it is a matter of the mechanics of getting the power to it and getting it to work.”
Nichols Farms began testing the grinder in the 2018-19 winter. “There were some struggles,” Brock said.
After the first year, the designers increased the hydraulic power on the input side of the grinder and boosted the system’s pressure so it could deliver more torque, and they sped up the grinder before bringing it back last winter to improved results.
“We covered quite a bit of ground with it this year,” Nichols said. “I would say we ran it on 40-50% of our orchards on the east side (where the farm typically has high NOW pressure).”
The farm tested the grinder in orchards with and without cover crops, and it performed equally well in both.
The system requires some prep work on orchard floors, and it requires an almond harvester to windrow pistachio mummies and condition an orchard floor before bringing the grinder in. The Worminator then comes through and picks up the mummies, collects them in an enclosed hopper, shreds them and drops them back on the floor in fine pieces that no longer provide a food source for the navel orangeworm. Nichols said he ran the grinder at 4 miles-per-hour with good results this past winter.
The grinder also works in almonds.
Pays for Itself
As for the economics of purchasing a grinder, Nichols said he believes the system will pay for itself in premiums alone many times over.
“One of the things that was driving me to look at the idea was economics,” Nichols said. “On pistachios, there is a very high premium for low-insect inshell product – on the order of 25 cents a pound for most processors. So, if you have a payable 3,000-pound inshell crop that comes in at 2% insect damage, you are missing out on roughly 750 dollars an acre, which is pretty substantial, plus the missed revenue opportunity of the nuts that were infested.”
Added together, the missed revenue in the example comes to $900 an acre when adding $150 an acre in missed revenue for the crop itself.
Nichols said the farm didn’t initially intend to make the grinder commercially available. “This is something we originally thought we could have for our own operation. But going through this process and seeing what it is able to do in the field, we took a position that we think this might be of commercial viability,” Nichols said.
Asked when growers may be able to purchase the grinder, Kwast said probably a year to a year and half.
“Things are going to have to be worked out,” Kwast said. “For example, how somebody wants to drive them: do they want something that is self-powered or do they want something they can drive with their tractor? There are a lot of different options here.
“For the first several years, you are probably looking at custom building one for each customer,” he said.
Asked how Nichols, Brock and Kwast may have come up with a solution to a problem that has dogged pistachio growers for decades, Kwast said it involved looking outside the box.
“I think we just looked at the problem a little differently than it was looked at in the past,” Kwast said. “The people that have tried to address it in the past have tried to address it with traditional agricultural practices, such as disking and flail mowers and such, and we kind of took a different approach.
“We kind of looked at it like, let’s collect the nuts in a hopper in an enclosed system with a grinder that is capable of grinding that product,” Kwast said. “I think it is just a different thought from the starting point of how to attack the problem.”
