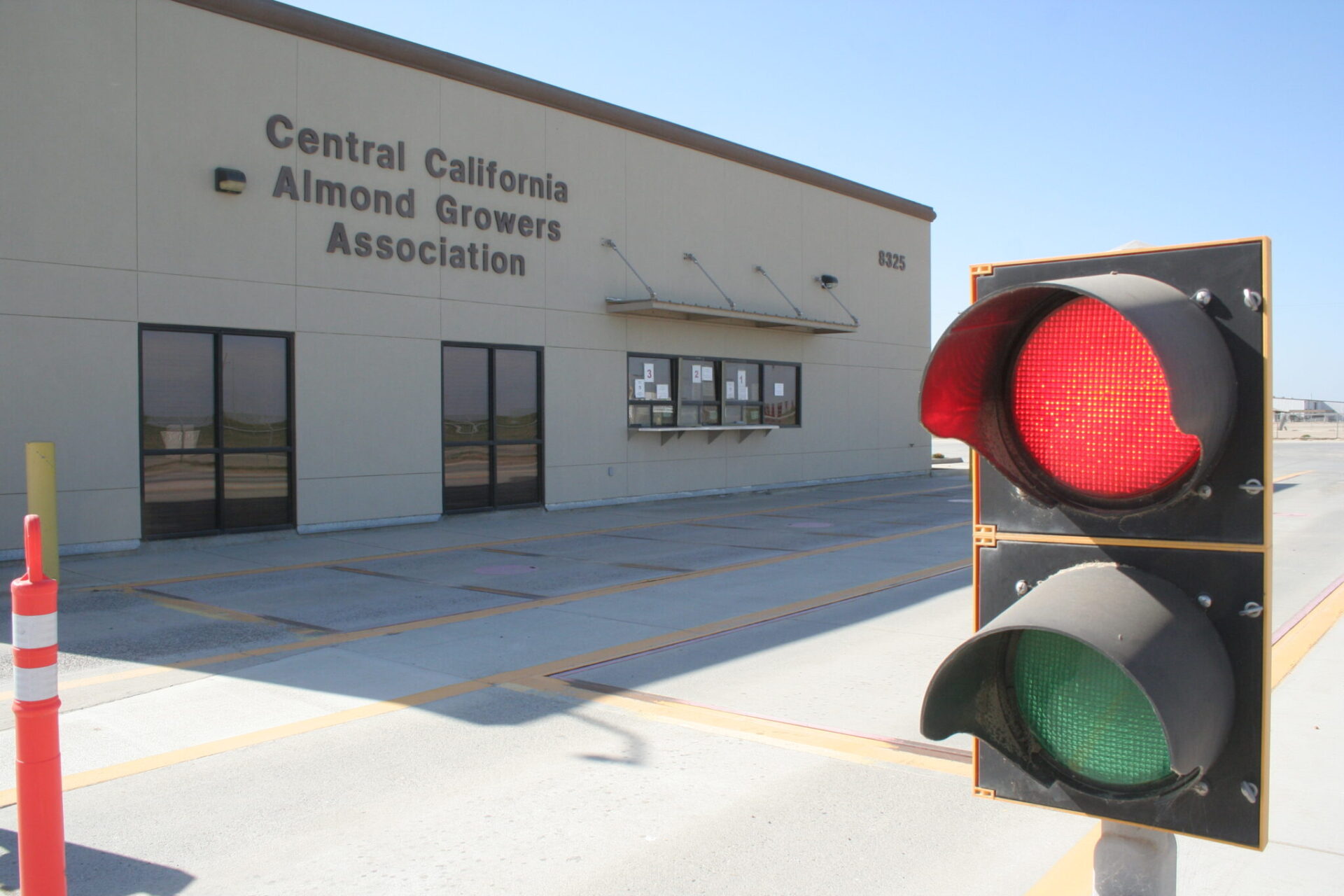
Kevin Long is getting close to overload at Superior Almond Hulling.
As general manager for the Fresno County operation, Long knows the pressure of inbound trucks waiting in line at the scale during harvest. He’s continually challenged to get empty trailers back out again as fast as possible. He’s watched storage space for almond stockpiles grow tighter every year.
And, since 2019, he’s dealt with a plant that’s reached full processing capacity. That’s forced Superior Almond Hulling to turn away new growers hoping to deliver their almond crops for hulling and shelling.
“We have more than doubled our volume in the last six years,” Long said. “The harvest congestion has become a big issue as we’ve grown.”
Long isn’t alone in coping with ever-greater quantities of almonds. Hullers and shellers up and down California are grappling with record harvests that often outpace processing ability.
The expanding crop volumes are putting more burden on truck scales, plant equipment and employees, spurring plant managers to find new ways to deal with the avalanche of nuts arriving during August and September.
“We’re all in the same situation,” Long said of the state’s 102 almond handlers. “California went from a crop of almost 2.6 billion pounds in 2019 to 3.1 billion this last year. That’s 500 million more pounds run through the same amount of hullers.”
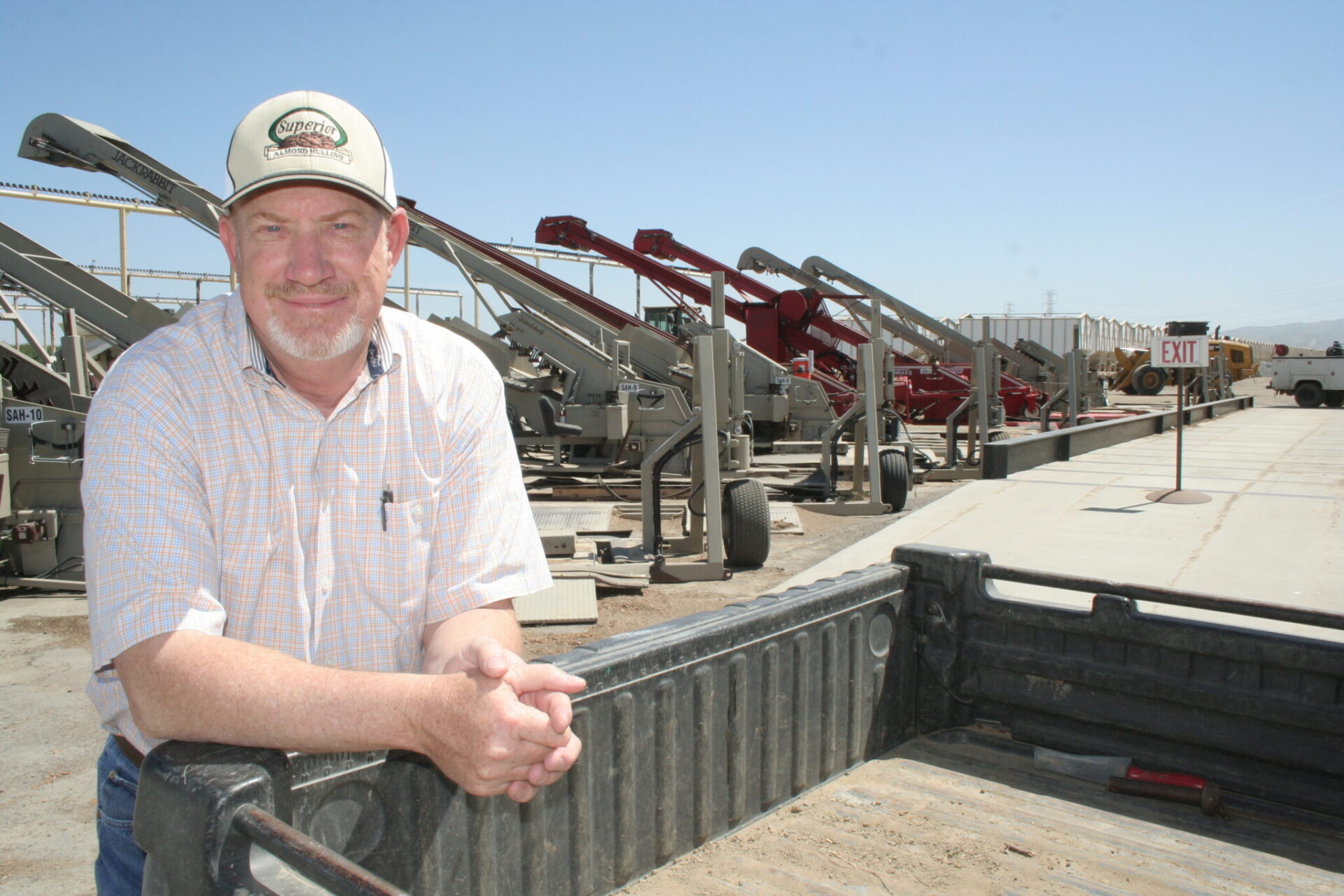
Investing in Upgrades
Like Long, Michael Kelley can relate firsthand to big-crop pressures. Kelley is president and CEO of Central California Almond Growers Association (CCAGA). CCAGA is the world’s largest almond shelling operation, with three plants at its Kerman site and one in Sanger.
In 2020, CCAGA shelled 155 million pounds, the largest volume in its 57-year history. The cooperative was as ready as it could be after investing heavily in its operations to stay ahead of bigger crops.
Since 2005, for example, it’s added two more trucking scales for a total of four. Last year, it completed a $10.2 million modernization of its main plant at Kerman. That upgrade expanded CCAGA’s processing volume from 9,100 pounds per hour to 14,000.
CCAGA has also purchased more stockpiling elevators at a cost of $102,000 each. It now counts 11 at its Kerman plant and three at its Sanger location. CCAGA also rented 75 acres north of its Kerman property for additional stockpiling. It’s increased employee numbers to 150 during the processing season, when its plants run 24/7.
Further, in 2016, CCAGA aggressively tried to relaunch a ranch stockpiling program to address the growing shortage of storage space at its plants. Through the program, growers store just-harvested almonds on their own property until CCAGA’s plants can process them. In 2020, the co-op ranch stockpiled 4.78 million pounds of edible meat, or 3% of its total volume.
“For two years in a row, that’s saved our neck,” Kelley said. “We have 11 large growers participating in the program, but we would love to double it.”
As a result of its record volume, CCAGA has closed its membership. It now counts 358 active members who deliver almonds from 63,063 acres stretching from Tulare County to Merced County.
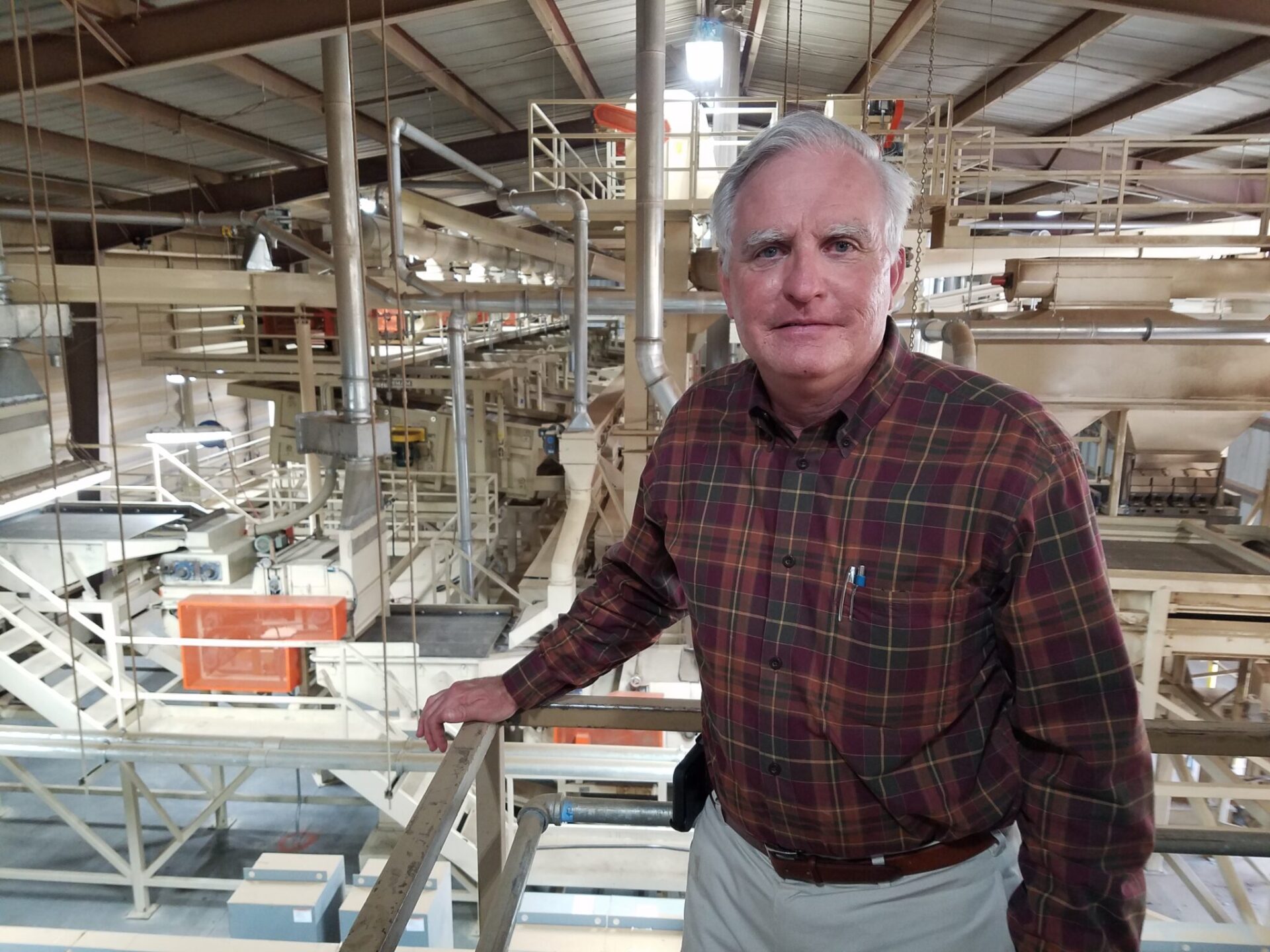
Keeping Up With Growth
Like CCAGA, Superior Almond Hulling has addressed the harvest crunch in multiple ways. That’s become necessary as burgeoning almond crops turned Superior Almond Hulling into one of California’s largest huller-shellers. The plant draws from 50,000 acres of almonds in Fresno, Madera and Kings counties.
Built to handle between 90 million and 100 million pounds yearly, Superior Almond Hulling shelled its largest-ever crop, 124 million pounds, during 2020. That included 8 million pounds of organic almonds.
Adding to the pressure has been the growth in acreage of self-pollinating varieties. They now account for over 10% of Superior Almond Hulling’s acreage, up from less than 3% in 2017. These orchards are nearly all ready for harvest in August, joining the more traditional Nonpareil varieties in the rush for processing.
“The crops are coming in early and further congesting us here,” said Long.
Superior Almond Hulling has spent more than $1 million in the last five years to manage its growth. In 2016, it added a second scale, with an adjoining shop, to weigh trailers coming in from the field. That cost $300,000, but it sharply reduced delays for inbound trucks. Superior Almond Hulling now uses its original scale for trucks picking up bins headed to processors or delivering hulls to dairies.
The plant recently purchased four additional stockpiling elevators for 11 in total. Each new elevator came with a $100,000 price tag, but they’re enabling Superior Almond Hulling to more quickly unload and store the loads of almonds coming onto its property during harvest.
The company, which owns its own trailers, also has increased those to 190 sets. Each set costs about $50,000.
“We went from receiving 130 loads a day six years ago to as high as 240 loads during the last harvest,” Long said. “We need to make sure we have enough empty trailers and stockpiling equipment to keep the harvest going without interruption.”
Moreover, Long has expanded the plant’s storage area by leasing 65 acres of adjacent land. He also added 12 employees to bump up his crew to 80 during the season.
But probably most important, at least in Long’s eyes, is Superior Almond Hulling’s decision to put crews to work at night. “A lot of hullers are reluctant to put their crews to work in the dark for fear of mixing up loads,” he said. “But we’ve invested in trailers and yard lights, and we’ve trained our night supervisors and our people to handle it.”
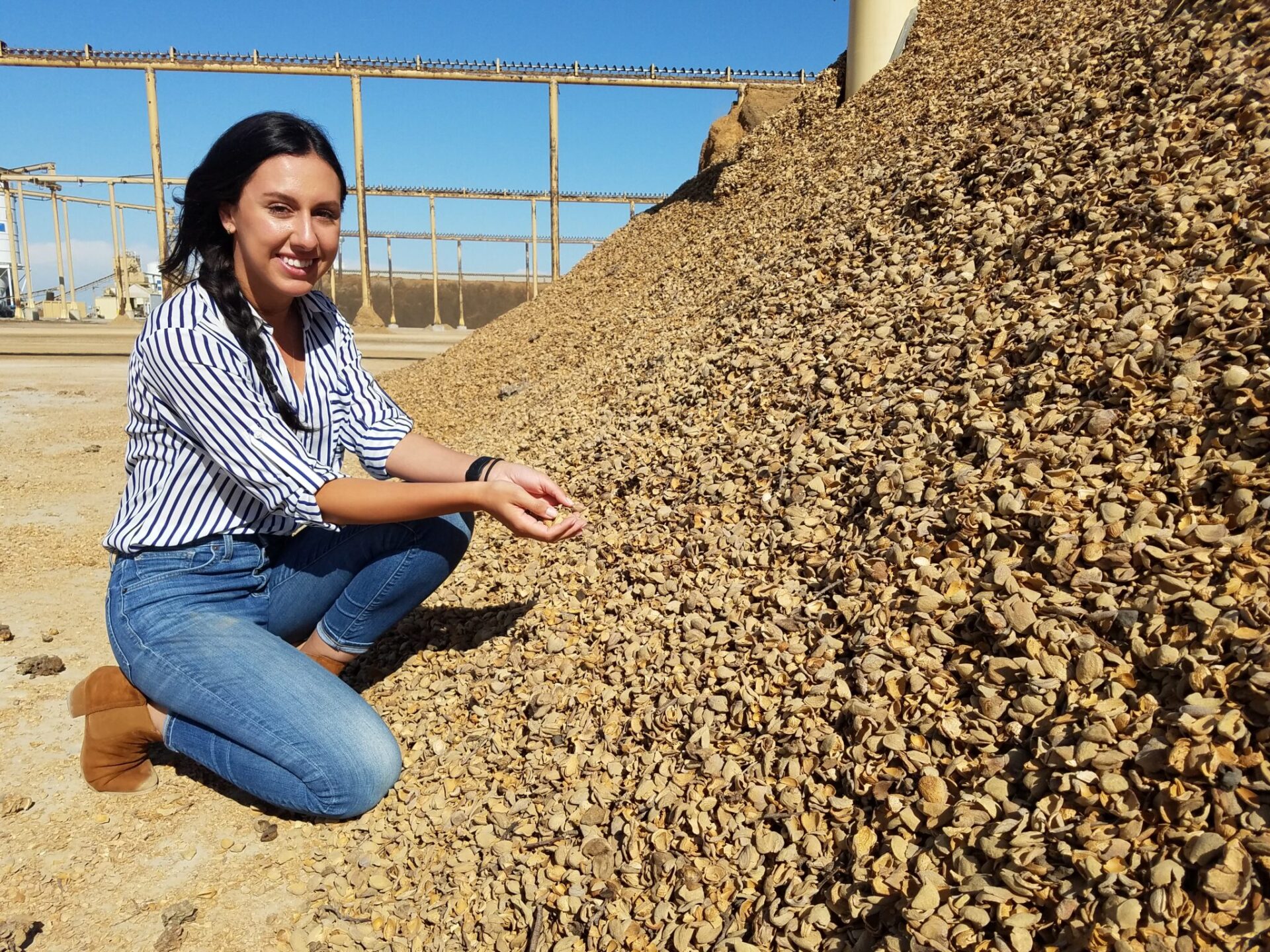
Future Needs
Looking ahead to the upcoming almond crop, both Long and Kelley predict smaller volumes.
“With the drought and the water situation, it’s hard to imagine we’ll see a duplicate of last year’s volume,” Long said. “We haven’t sent out our contracts yet, but we’ll probably be down about 10% to 110 million pounds. It’s still too much.”
Even with a similar drop expected next year at CCAGA, Kelley knows his plants will face continued pressure in coming harvests. As a result, the co-op is considering plans to modernize its Sanger plant in the next few years.
“If we could increase our processing volume at the Sanger plant from 8,200 pounds to 14,000, as we did here at Kerman, that would carry the day,” he said. “That would allow us to handle future crops of 165 million pounds very efficiently.”
For now, CCAGA will put more emphasis on accurate forecasting in the field. “And we’re placing more value on our staff and working to build a culture where employees buy into the vision of what’s needed to move forward,” Kelley added.
Ultimately, California needs more huller-sheller plants, Kelley and Long said. But with a hefty price tag of $18 million to $23 million, building a new shelling facility is an investment few can make. Kelley said two former cooperative cotton gins in the San Joaquin Valley are converting to almond sheller plants. There’s also a rumor that a new plant will be built on Central California’s Highway 198, he added.
For hullers and shellers who have lived through the glut of the past few seasons, the new processing capacity would be welcomed.
“New plants are definitely needed,” said Long. “Harvest congestion is a problem that’s not going to go away.