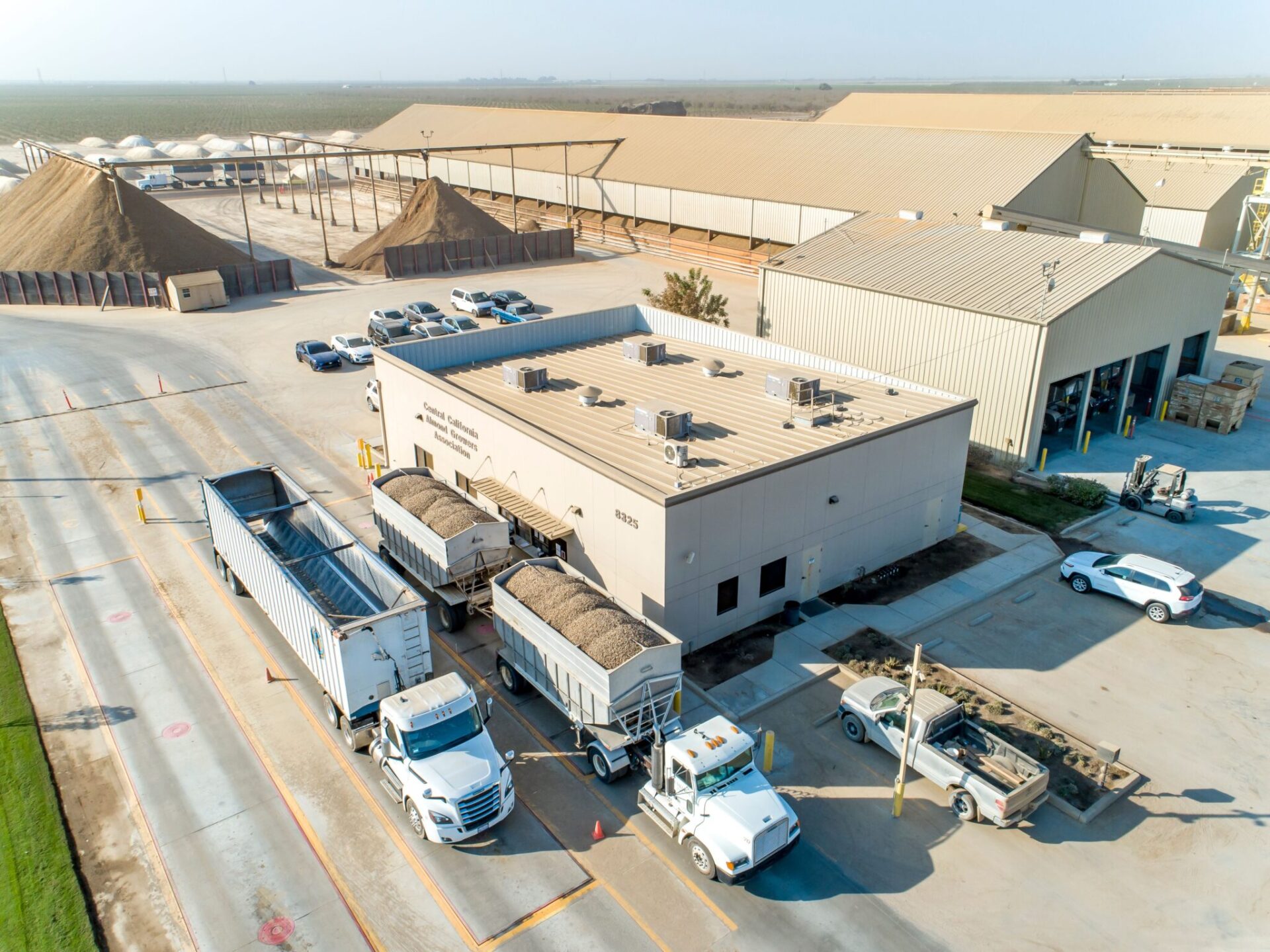
Operators of almond and pistachio processing plants are cautiously optimistic their labor force will be adequate in August to handle this year’s crops.
Hullers and shellers as well as processors of value-added products rely on skilled workers to operate equipment and manage incoming loads. There are also numerous unskilled jobs that need to be filled to keep the plants operating at optimum efficiency.
Even though most COVID-19 restrictions were lifted in June, the U.S. Department of Labor reported approximately two million people were still receiving unemployment benefits in California. The California Workforce Association reported in June that fewer job seekers are contacting their office about employment.
As in other industries, nut handlers report challenges staffing their work force. Some plants are offering worker bonuses for referrals, competitive pay and other incentives to attract skilled and unskilled workers this year.
Labor Challenges
Ali Amin CEO of Primex, detailed some of the hurdles encountered in processing the 2020 crop and how the pistachio processor would meet labor needs this year.
Primex did have a COVID-19 outbreak in 2020, and the plant had to reconsider operations quickly to protect workers, Amin said.
“We are emphasizing education, and we would like to incentivize all employees to be vaccinated.”
This year, Amin said, the plant is bracing for a tighter labor market and higher labor costs. Primex works with employment agencies and has relationships with farm labor contractors to meet labor needs.
They are reviewing salary ranges to attract workers, but negotiating higher salaries for skilled and unskilled workers will eventually affect the growers’ bottom line.
“We can squeeze our margins, but eventually it will go to the grower. Higher nut prices will help this,” Amin said.
Unskilled labor at Primex does not always remain unskilled, he added. Seasonal workers recognized for their skills and work ethic can become permanent employees, and Primex strives for those long-term relationships with employees.
The reality of a tight labor market is that the plant operations can be maintained at 20% below optimal labor levels, but it can create delays.
“It is a challenge, but it can be done, “Amin said.
Kirk Squire, grower relations manager at Tulare-based Horizon Nut, said labor contractors are reporting that workers aren’t out there this year.
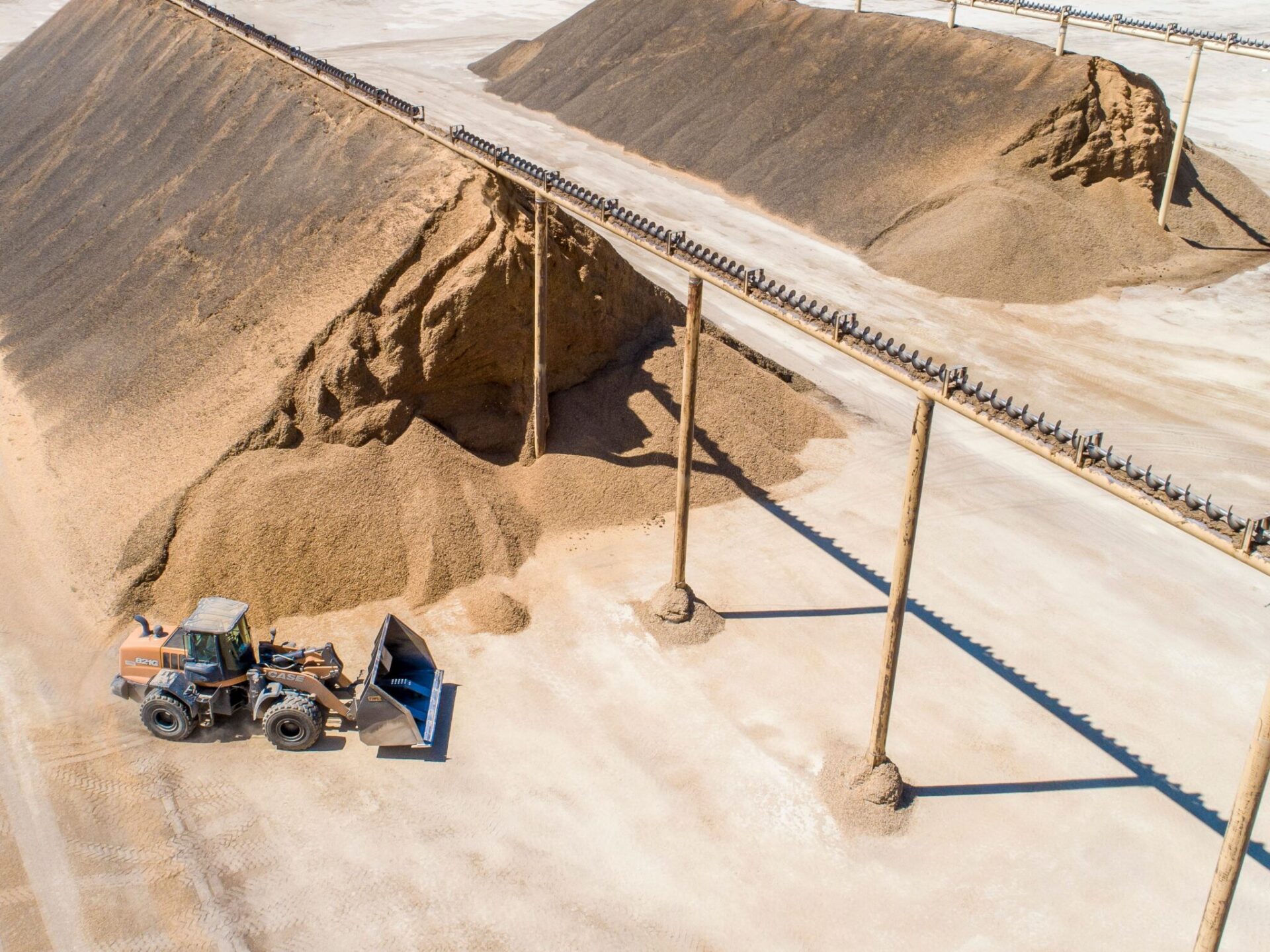
He said the labor shortage couldn’t entirely be blamed on the pandemic, but on continuing struggles with drought in the San Joaquin Valley. Both year-round and seasonal workers moved away from the area during the last drought and haven’t returned, he said. Competition with other nut processing plants for labor has increased the cost of labor, Squire added.
Trucking companies that contract to deliver nuts to the plants have also been experiencing a shortage of drivers. An effort supported by Western Ag Processors Association is increasing truck weight limits, which would cut down on load numbers and the need for more drivers.
Looking ahead, Squire said that automation in many areas of Horizon’s plants would be needed to process pistachio crops in the future as technology improves. Sorting is the main area in processing where automation is becoming more common as the cost for hand sorting and need for high labor numbers is on the rise.
“We have been at the tipping point for years with human versus automation,” Squire said.
With planned plant expansions at their three facilities, Horizon is looking at processing 120 million pounds of pistachios in the future. Automation can’t cover all their labor needs and there will be job opportunities, he added.
Mike Kelley, president and CEO of Central California Almond Growers Association said he is optimistic that the four facilities operated by CCAGA will have the necessary workforce in place for this year’s harvest.
“We are down now, but optimistic that numbers will improve in the next two months,” Kelley said.
With a nod to the multiple-plant workforce that powered through the 2020 harvest, Kelley thanked the shellermen, plant operators, stockpile workers, loader drivers, sanitation and office staff who kept the plant in operation.
Labor is the biggest operating cost at the CCAGA plants, the largest huller and sheller of almonds in the world. Kelley said labor accounts for around 50% of their operating costs, up from 40% just five years ago.
The plant depends on skilled workers to operate machinery and manage stockpiles from August through the end of the year.
“A lot of talent is required of our workers. Harvest is fast-paced, and we can’t just put anyone on a machine. If an operator doesn’t show up, we can’t put just anyone in their place.”
Worker safety is a serious issue with CCAGA, and trained personnel are needed for machinery operation. Staffing has to be adequate or the plant can’t operate, Kelley said.
Butch Coburn, plant manager at Hughson Nut Inc., said various avenues to attract workers have been explored. Hughson Nut operates three value-added plants and needs a sufficient labor force to maintain production. In June, he said they had held job fairs and are offering workers bonuses if they can bring in a new employee.
Critical needs are forklift drivers and machinery operators. Like other processors, Coburn said that where possible, they are turning to automation.
As the technology advances, more nut processors are turning to automation and not just in the sorting lines, said Mike Durrant of MPA solutions. As plant capacities increase, the need for labor will also increase. Product quality is also important for processors, he said.
Durrant noted that automation in processing plants is not just about replacing workers with machines or filling in labor gaps, but it can assist with providing the data to assist with management decisions.
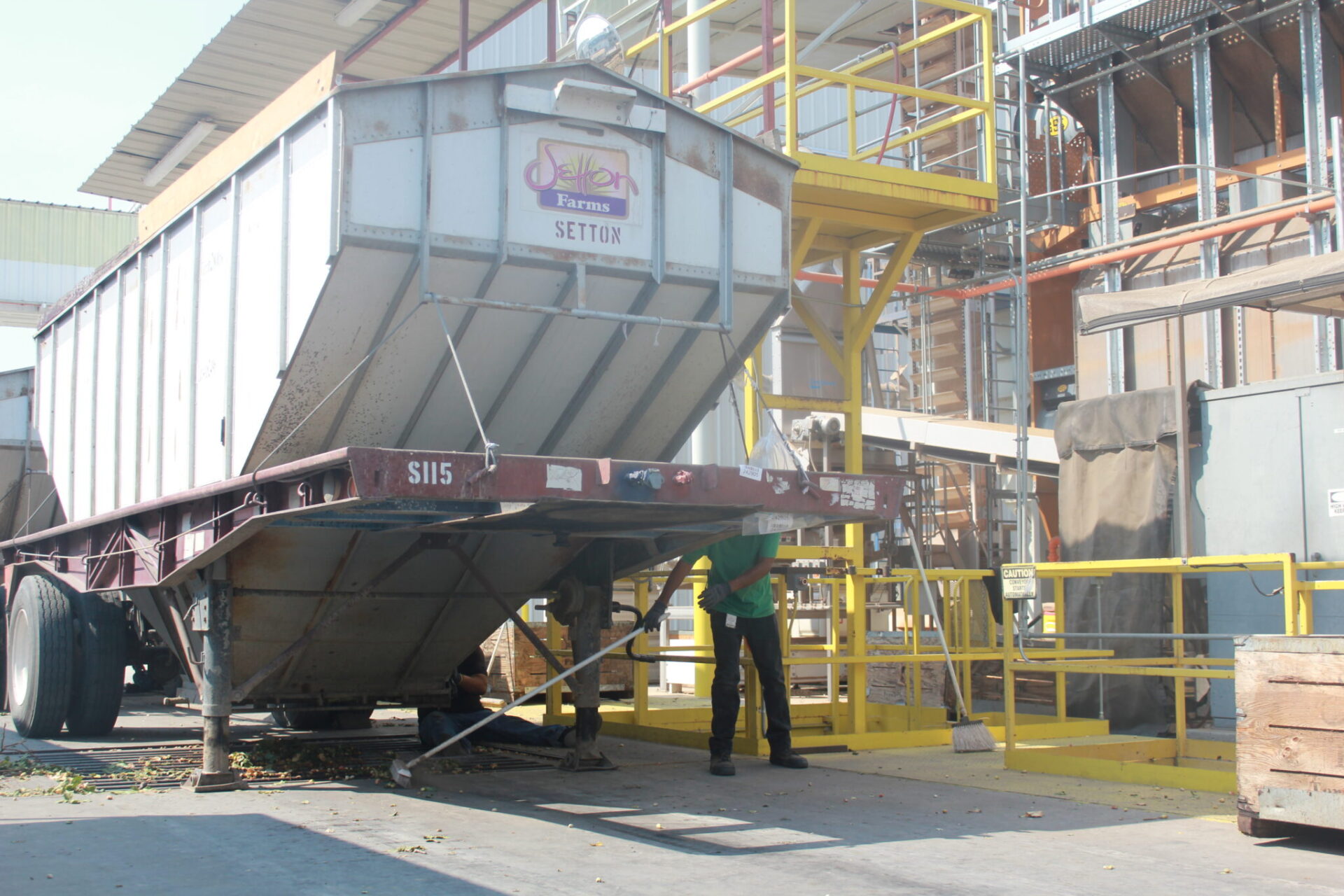