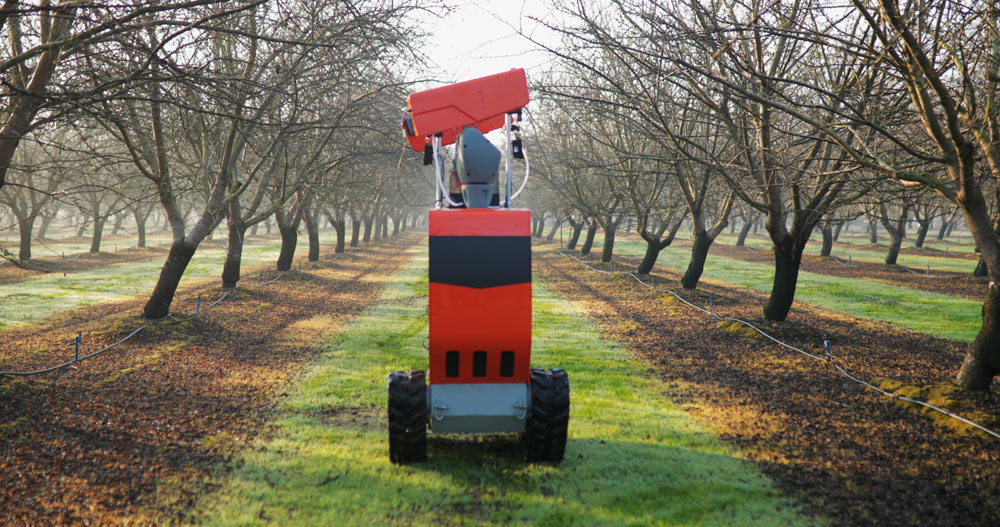
The Roomba, a robotic floor sweeper, has been a hot Christmas gift for the past few years for consumers wanting to have hands-free cleaning. Almond growers may soon get their own robotic clean-up machine with the introduction of InsightTRAC’s Rover autonomous mummy nut remover.
The brain child of Anna Haldewang, InsightTRAC founder and CEO, the Rover uses mounted cameras to “see” mummies. It then knocks them from trees by firing biodegradable pellets powered by air blasts. The machine is designed to eliminate polling crews and possibly winter shaking, depending on the number of unharvested nuts left on trees.
And unlike human mummy removal, the Rover can operate around the clock for a couple of days before its pellet supply and 18-gallon gas tank need to be refilled. During a season, it can cover about 425 acres, a comparable pace to a polling crew of eight people working nine-hour days, Haldewang said.
But the machine can work during daylight and in the dark and doesn’t call in sick or need breaks. A single technician oversees operation of the Rover using a tablet to monitor its course.
Going Commercial
In late fall 2021, Haldewang sought five to eight growers to host demonstrations in January in the state’s three main almond growing regions. Later this winter, she plans to conduct a preliminary trial with pistachios, which also have issues with navel orangeworm overwintering in mummies.
“We then want to branch out into walnuts, then branch out into other crops,” she said. “We’re looking into other seasonal activities we can do around the orchard.”
Haldewang has already started taking orders for the Rover. If all goes according to schedule, she plans to make the first deliveries the last quarter of 2022.
The one unknown is current supply chain disruptions. “That’s definitely been a challenge, especially as we near the period of production,” she said. “We’ve had to wait on other suppliers to bring in the components. It’s been a challenge, but I’m proud of the team.”
The True Cost of Mummies
Extension specialists have long recommended almond growers in the Sacramento Valley strive for fewer than two mummies per tree. In the central and southern San Joaquin Valley, they recommend a target of one or fewer mummies per tree. The reason for their concerns is mummies can provide overwintering habitat for NOW larvae. They also can provide egg-laying sites for the first moth flight in the spring.
By removing and destroying this habitat, growers typically start the season with much lower NOW populations.
Dr. Sebastian Saa, senior manager for agricultural research for the Almond Board of California, hasn’t seen the Rover in action. But he said the almond board welcomes novel and cheaper methods to aid winter sanitation.
“We understand that this cultural practice is key to implementing a full integrated pest management approach to control navel orangeworm, our key insect challenge,” he said. “Winter sanitation is not only an expensive cultural cost for our growers but also a treatment that is hard to do right; effective sanitation with less than two mummy nuts per tree.”
Doing nothing and leaving mummies on the trees also can hit growers hard financially. Blue Diamond’s Mel Machado estimates that NOW damage at 2% reject levels can translate to losses of $336 to $436 per acre.
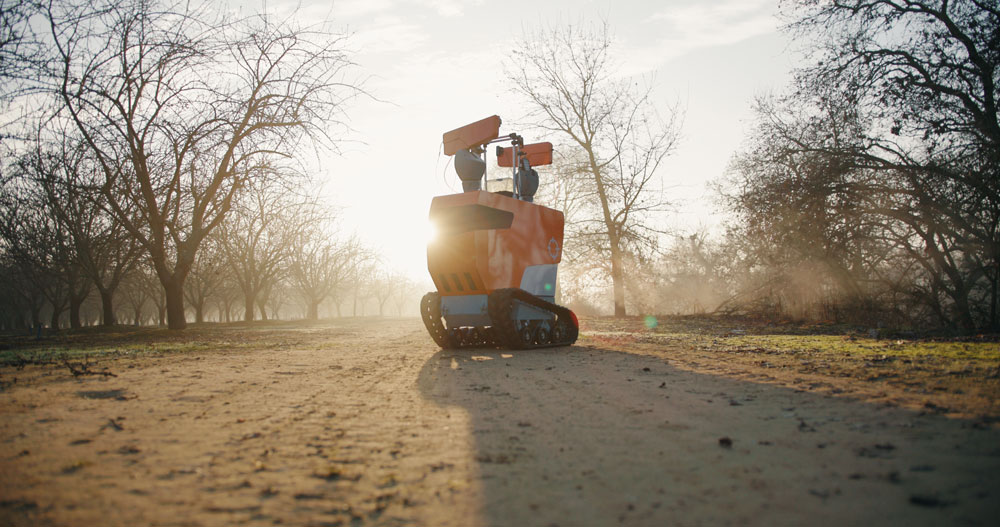
With hourly wages of more than $30 per hour, Australian almond growers are also looking at automation to manage their expenses. Although they don’t have NOW, they do have Carpophilus beetle and carob moth, considered Australian almonds’ most serious insect pests. But much like NOW, the two Australian insect pests overwinter in mummy nuts.
As a result, Haldewang said, growers Down Under are equally interested in her Rover automation. With the Australian almond season opposite California’s, she’s able to double up on demonstrations and collect twice as much data per year. Haldewang also plans to conduct demonstrations in Australian almond orchards in June.
The Evolution of the Rover
As an amateur beekeeper in Indiana, Haldewang had heard about the plight of honeybees and thought about using drone pollination to augment the millions of beehives required during the six to eight weeks of California almond pollination.
After talking to California almond growers and industry representatives, she learned of the pressing mummy nut issue and refocused her efforts. Haldewang admitted she didn’t have the technological background to develop such robotics, but she credited her team for bringing the needed engineering know-how.
The first hurdle to overcome was how to remove the mummies on the tree. About 15 people came together in a room to brainstorm.
“No idea was off the table,” she said. They narrowed the candidates down to five that included an air jet, a water jet and a bristle brush. Eventually, they weeded out the bristle brush because of the difficulty pulling it through the tree. A water jet only worked if the machine was a few feet away from the mummy nut. Plus, with the current drought, Haldewang said she didn’t want to potentially increase water use in an orchard.
A system similar to a pellet gun that used biodegradable plastic pellets powered by air blasts seemed to be the most effective at removing mummies.
Collecting Photos of Mummies
Beginning in 2019, Haldewang began the arduous task of collecting over 20,000 images of mummy nuts to create a database.
“I did it all by hand,” she said, laughing. Using a make-shift system comprising a light and laptop strapped to her, Haldewang walked orchards taking photos at specific distances and angles that mimicked how the Rover would see mummies.
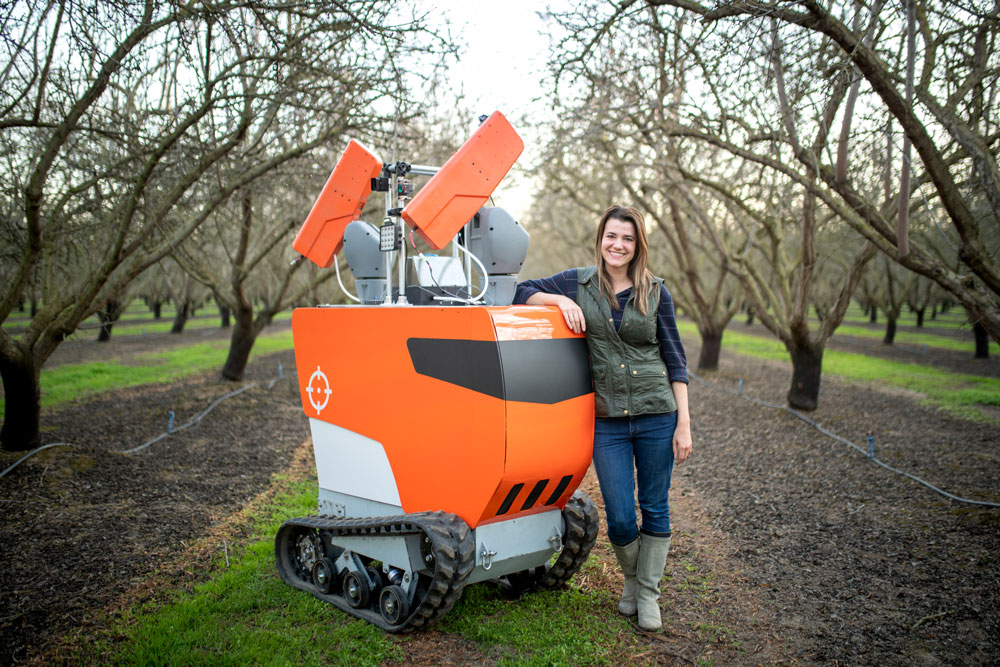
Digital cameras on the Rover view a mummy nut and relay the information. Using artificial intelligence and drawing from the image database, the computer “brain” within the Rover can accurately identify and remove mummies up to 30 feet away.
As the Rover goes through orchards on its duties, it continues to collect mummy nut images, improving upon the image database, she said. At the end of the clean-up activities, the Rover can produce maps, showing growers where the most and least number of mummies were in the orchard.
“Over time, the grower is able to see patterns in their orchard,” Haldewang said. “Maybe [the higher mummy numbers are] related to stress in this area due to irrigation. This data is going to be really powerful to answer other questions as well as in other seasons.”
Winter Demonstrations
Haldewang began work on the original Rover prototype in 2019. She put it through demonstrations in a couple of California almond orchards with a few grower and industry members during the 2020-21 winter. Based on their suggestions, she and her engineering team added the improvements and launched what she refers to as Rover 2.0.
Instead of having cameras strapped to the machine as the original one did, the latest prototype has the imaging technology integrated into the body design. But much like the original machine, the latest version retained the four-foot-wide footprint with tracks to navigate potentially muddy orchards. The Rover is powered by an electric motor with an on-board gas generator.
Haldewang foresees growers using the machine in two ways. If they have a higher number of mummies, they’d mechanically shake first, then use the Rover to clean up the last few nuts. This would be much as they would with a hand polling crew.
If growers had a clean harvest and only a few mummies per tree, they could enlist the Rover alone to remove the remainders.
“If you have 50 per tree, it will take three hours to get through an acre,” she said. “If you have side-by-side polers versus us, we would be slower. But where we pick up that time is we operate 24/7. We don’t take breaks. We keep at it long after they’re gone for the day.”
InsightTRAC plans to market the Rover directly to growers with larger acreage or to custom operators who want to provide an added service to their grower-customers.
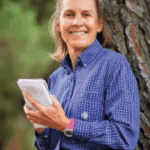
Vicky Boyd
A veteran agricultural journalist, Vicky Boyd has covered the industry in California, Florida, Texas, Colorado, the South and the Mid-South. Along the way, she has won several writing awards. Boyd attended Colorado State University, where she earned a technical journalism degree with minors in agriculture and natural resources. Boyd is known for taking complex technical or scientific material and translating it so readers can use it on their farms. Her favorite topics are entomology, weeds and new technology. When she’s not out “playing in the dirt,” as she calls agricultural reporting, Boyd enjoys running, hiking, knitting and sewing.