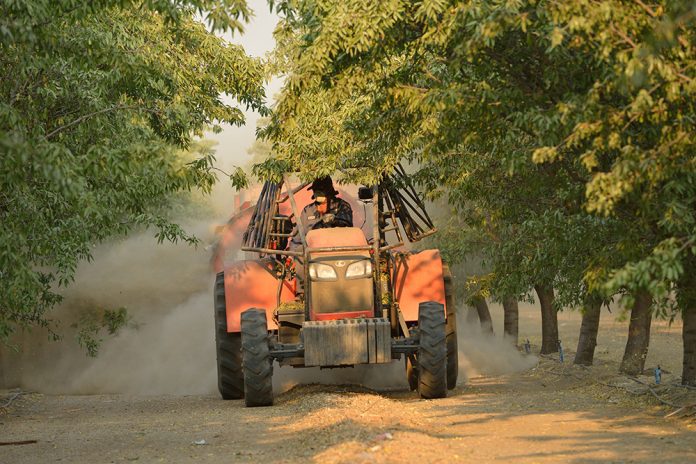
Communication and efficiency are the two most important words on almond harvest contractor Matt Efird’s mind at harvest time.
“Contract harvesters are paid to pick up nuts and put them in the trailer. They are not necessarily paid to do it cleanly,” Efird said, explaining why communication with almond growers who have hired him to harvest their crop is critical. He spells out the orchard floor conditions necessary for him to do the best possible job of picking up nuts at an efficient speed.
Efird, also an almond grower in the Fresno area, serves as vice chair on the board of Central California Almond Growers Association, the largest huller and sheller of almonds in the state. From that perspective, he sees the need for efficiency and communication.
He makes it clear that he does not want to create more dust than necessary when his machines sweep and pick up nuts, but the reality is that harvest is less efficient at slower speeds needed for optimal dust reduction. Orchard floors with weeds, ruts, trash and soft dirt make it difficult to maintain speed and reduce dust. It is the responsibility of the almond grower to have orchard floors firm, clean and smooth at harvest time, he said.
“Contract harvesters are paid by the acre. With optimal field conditions, I can pick up nuts at four miles per hour. If I have to go slower due to uneven floors or excess sticks, that makes me less efficient, “ Efird said.
He can operate at slower speeds, but it is hard to justify when it cuts into the total number of acres he is able to cover during the harvest season. “There are a lot of caveats; that is why we have contracts. I do not know anyone who does not charge more per acre for unprepared orchards.”
Contracts Spell Out Expectations
Efird’s contracts for almond harvest spell out what he expects when his harvest equipment arrives at the orchard. Harvest requires a clean, firm floor where almonds can be shaken, swept or blown into windrows and harvested, he said. Growers need to eradicate weeds from berms and floors, smooth floors and remove anything they do not want dumped in the bins and delivered to the processor. Rocks, sticks and trash in the windrows slow down the harvest process. Efird said he can deliver dirt along with the nuts, but excess dirt causes wear and tear on machinery and expensive down time for repairs at the processor.
Recent changes in how growers are charged for processing may also make growers aware of orchard conditions at harvest. Hulling charges at some but not all processors are based on incoming weights.
Firm floors not only reduce the dust generated when nuts are picked up off the ground, but they reduce the amount of dirt that is picked up with the nuts.
Efird said they have calculated in recent years that each truckload of almonds coming into the plant also contains about 1,600 pounds of dirt.
Sticks that come in with the loads also pose a problem. They can slow down the unloading process and must be separated from the nuts.
Harvest Speed Should Be Discussed
Efird said growers should talk with their contract harvester about harvest speed- or as an alternative, purchase a conditioner and run windrows through prior to pick up. This piece of equipment picks up the nuts in the windrow, sifts out much of the dirt, sticks, rocks and leaves and leaves a cleaner windrow for the harvester.
Use of these machines has increased exponentially in the last few years, Efird said, mostly because it allows the nuts to dry down faster and accelerates harvest so water-stressed trees can be irrigated sooner. Cleaner windrows are a bonus.
Given the lack of rainfall in recent years, younger orchards with microirrigation tend to have floors that will not be firm, and Efird said that you have to accept running at slower speeds.
Madera-based custom harvester and almond grower Jeff McKinney said having his equipment field-ready at the start of harvest season is a big part of harvest efficiency. His focus is on off-season repairs, anticipating what parts will wear out and planning ahead, all with an effort to avoid downtime in the field.
“We know what parts won’t make it through the season and we try to have those on-hand,” McKinney said.
Like Efird, McKinney believes that communication with the grower before and during harvest is important in keeping the machines running.
“We always think five to seven days ahead of the shake, making sure the trees have been watered and water is shut off. We do a lot of scouting to make sure the orchards are ready when we are supposed to arrive.”
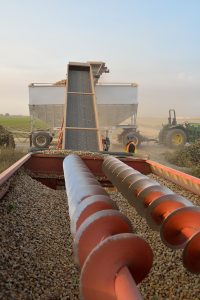
Planning Ahead Saves Time
Efird also recommends preharvest planning with the grower, contract harvester and the processor to keep harvest running.
Typically, he said he runs two harvest machines in an orchard, but three is optimal. When they pull in, he said they check for structures that could be affected by dust and determine orchard boundaries.
In single-variety orchards, they break the block into thirds and the machines each take a block to keep out of each other’s ways.
If harvesting two different pollinating varieties at the same time, he said they make sure each machine only picks up one to avoid co-mingling. Between dust and shuttles running in the orchards, it works best to not be in close proximity, Efird said.
Having experienced machine operators helps with efficiency, McKinney said. He has a good return rate with employees who know how to keep the operation running and take care of equipment.
In recent years, McKinney said he has improved efficiency of harvest by stockpiling almonds harvested from his own orchards. Having a yard large enough to handle 40 to 50 truckloads has been a lifesaver, he said, as it saves on trailers and wait times during the busiest time of the year.
The piles are tarped, sealed and fumigated while in his ranch yard and are taken to the processor later after the bulk of the harvest has been delivered.
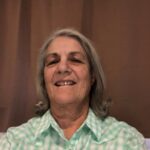
Cecilia Parsons | Associate Editor
Cecilia Parsons has lived in the Central Valley community of Ducor since 1976, covering agriculture for numerous agricultural publications over the years. She has found and nurtured many wonderful and helpful contacts in the ag community, including the UCCE advisors, allowing for news coverage that focuses on the basics of food production.
She is always on the search for new ag topics that can help growers and processors in the San Joaquin Valley improve their bottom line.
In her free time, Cecilia rides her horse, Holly in ranch versatility shows and raises registered Shetland sheep which she exhibits at county and state fairs during the summer.