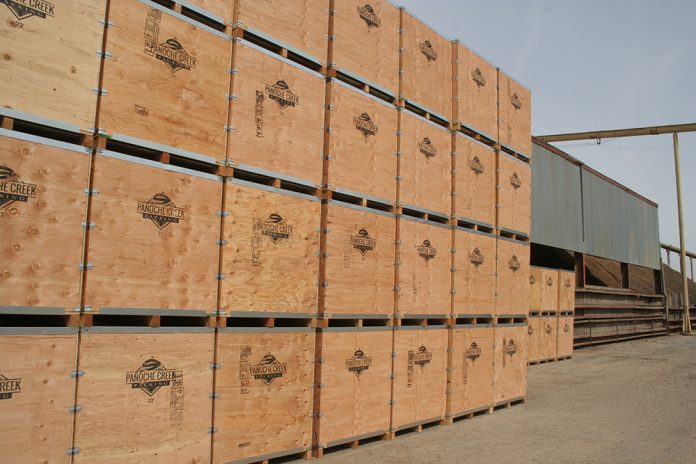
California almond handler Dave Phippen has spent sleepless nights this year wondering if he’ll find enough wooden bins and warehouse space to store the upcoming crop.
“It gets my heart pumping when I’m walking through our warehouses looking for empty spots,” says Phippen, a partner in Travaille & Phippen, a huller-sheller and shipper based in Manteca between Stockton and Modesto.
Phippen isn’t alone in trying to find extra storage capacity. Handlers throughout California’s almond industry face a shortage of bins and storage space this season. The shortfall stems in part from major supply chain problems that arose when the pandemic’s lockdown began backing up shipments in 2020. Almond storage bins that should have been emptied months ago are still full.
Meanwhile, as shipments stalled, California produced record or near-record almond crops, creating a now-looming carryover projected at 800 million pounds or more. With another large crop on the way, handlers are worried.
Such a carry-in will require some 300,000 to 400,000 bins alone, says Denis Prosperi with Panoche Creek Packing. The San Joaquin Valley-based company is one of California’s largest almond handlers.
“Instead of being empty when the harvest starts, many bins will still be full of last year’s nuts,” Prosperi says. “That means when the crop comes, unless it’s extremely light, or shipping really takes off, or something changes with sales or volume, you’re starting with a deficit of bins.”
At the same time, he adds, “all the packers are sitting on probably two to three times more packed sold product, not in wooden bins but packed and ready to ship, that’s sitting in warehouses because of shipping problems at ports. Every 1 million pounds of almonds in the barn that’s packed but not shipped is taking the space of 2 million pounds of almonds you could have had in bins.”
Moreover, huller-shellers not only have been pushing out more volume with bigger almond crops but increasingly finishing their season’s work by December.
“Huller-shellers are speeding up their productivity, and we’re slowing down ours, hence a bin shortage,” Prosperi says.
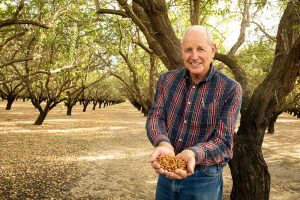
Spotlight on Bins
Although the 4-foot x 4-foot wooden bins don’t typically attract the spotlight, they play a crucial role in the almond industry.
“Wherever almonds are going until they’re packaged for commercial use, they’re in a wooden bin,” says Phippen.
Industry giant Blue Diamond Growers doesn’t use wooden bins, relying instead on bulk transport in trucks. But nearly all other packers and processors use the steel-reinforced, plywood containers to move and store their hulled and shelled almonds.
At hulling and shelling facilities, the nuts are loaded into bins before making their way to fumigation, storage and sizing. Once the almonds are packaged for shipment, the empty bins return to the huller-sheller or to the handler, who owns them. Unlike cardboard units, wooden bins can withstand the weight of storage stacking and the sometimes-rough treatment by forklifts and other transport equipment.
But finding those bins has become increasingly difficult and expensive. To help meet their need for more storage last year, Phippen and his partner ordered 3,000 bins at a cost of $250 each, sharply higher than the $145 paid in 2020.
Phippen also looked at renting outside storage space. But landlords wanted a five-year contract, and he didn’t want to commit that far ahead. That drove Travaille & Phippen, which packs and ships almonds for 120 growers, to build extra storage last year at a cost of $1.35 million. The new warehouse was filled by mid-September, forcing Phippen and his team to struggle with space throughout the harvest. This year, they’re building another storage facility.
Such expenditures, says Phippen, “are sucking all the capital out of our company.”
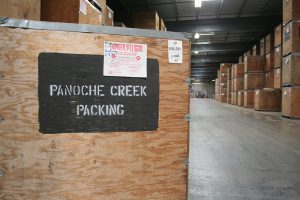
Seeking More Storage Space
Like Phippen, Prosperi has struggled to ensure there will be enough bins and storage space at Panoche Creek Packing. The company accepts nuts from about 40 huller-shellers and handles a yearly volume of about 170 million pounds of almonds.
Panoche Creek’s packing plant in Kerman has 500,000 square feet of storage space plus forklifts and other equipment needed to process and warehouse its almonds. Once the nuts have been packed to sales specifications, Panoche Creek delivers them to the ports of Oakland, Los Angeles or Long Beach, or to domestic buyers.
Prosperi has been buying and renting bins, “but lately we’re still short,” he says. “We’ve constantly got workers repairing bins because it’s too expensive to keep buying new ones.”
Compared to past years, Prosperi has paid 50% or more for new bins this year. That’s not only due to increased demand but because bin manufacturers have seen their own prices rise as costs for wood, labor, trucking and fuel escalate.
Prosperi also has been forced to rent additional space, just as other handlers have. In his case, it was to store 20 million pounds of almonds outside of Panoche Creek’s Kerman plant. He could have constructed an additional warehouse but says, “I’d have to go buy a piece of property and build the building, and you know how hard it is to get anything built today?”
On top of all that, the longer almonds sit in bins, the more likely they’ll need to be re-fumigated, says Roger Isom, president and CEO of Western Agricultural Processors Association.
“That’s another added cost, and it’s not cheap,” Isom said. “In some cases, depending on where you are, you might already be up against your fumigation permit limit with the air district.”
‘A Game of Patience’
At Central California Almond Growers Association, the state’s largest huller-sheller, President and CEO Michael Kelley has offered packers the opportunity to store their empty bins ahead of harvest at his two sites in Kerman and Sanger.
“It will buy us an advantage to have bins on site,” says Kelley. “But, in the end, all bins in the state will be full at some point in the fall for some packers, and we will have tough decisions to make in operating our plants to finish the shelling season.
“There’s a potential that if we don’t get bins, we may not be able to run one or two of our shellers toward the end of the season,” he adds.
That’s the last thing Kelley wants. He remains hopeful that time will cure the industry’s pain as COVID-19 becomes more manageable and the strains on the shipping system ease.
Likewise, Phippen is keeping his fingers crossed that the almond harvest and its hulling, shelling and packing operations run without interruption. But there’s no guarantee.
“We’re all challenged this year,” he says. “It’s going to be a game of patience.”