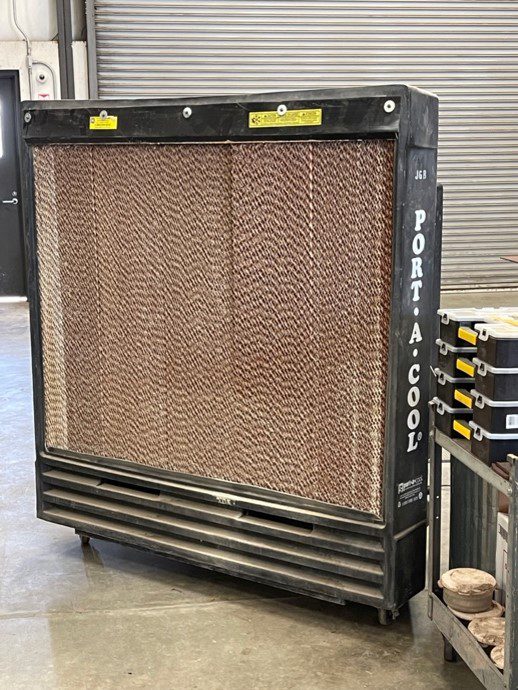
Regulations mandating temperatures below 87 degrees F in all indoor places of employment, including farm shops, tree nut hullers and processors, might just be right around the corner. The Cal/OSHA Standards Board held hearings in May and June on the proposed new Cal/OSHA Standard for “Heat Illness Prevention in Indoor Places of Employment”. Yes, that’s right, indoors!
The new proposed regulation would apply to all indoor work areas where the temperature equals or exceeds 82 degrees F. The regulation specifies access to water, requirements for cooldown areas, engineering controls, training requirements for employees and supervisors and a written heat illness plan. Engineering controls must be used to reduce and maintain the temperature and heat index to below 87 degrees F. A cooldown area must always be provided when employees are present, and a cooldown rest period must be afforded to each employee.
Effective training in the following topics shall be provided to each supervisory and non-supervisory employee before the employee begins work that should reasonably be anticipated to result in exposure to the risk of heat illness:
The environmental and personal risk factors for heat illness as well as the added burden of heat load on the body caused by exertion, clothing and personal protective equipment.
The employer’s procedures for complying with the requirements of this section, including but not limited to the employer’s responsibility to provide water, cool-down areas, cool-down rests, control measures and access to first aid as well as the employees’ right to exercise their rights under this section without retaliation.
The importance of frequent consumption of small quantities of water, up to four cups per hour, when the work environment is hot, and employees are likely to be sweating more than usual in the performance of their duties.
The concept, importance and methods of acclimatization and of close observation during acclimatization pursuant to the employer’s procedures under subsection (i)(5).
The different types of heat illness, the common signs and symptoms of heat illness, and appropriate first aid and/or emergency responses to the different types of heat illness, and in addition, that heat illness may progress quickly from mild symptoms and signs to serious and life-threatening illness.
The importance of employees immediately reporting to the employer, directly or through the employee’s supervisor, symptoms or signs of heat illness in themselves, or in co-workers.
The employer’s procedures for responding to signs or symptoms of possible heat illness including how emergency medical services will be provided should they become necessary.
The employer’s procedures for contacting emergency medical services, and if necessary, for transporting employees to a point where they can be reached by an emergency responder.
The employer’s procedures for ensuring that, in the event of an emergency, clear and precise directions to the worksite can and will be provided as needed to emergency responders. These procedures shall include designating a person to be available to ensure that emergency procedures are invoked when appropriate.
We delineate these here to emphasize the point that this is a serious issue and Cal/OSHA is going to great lengths to make sure employers adequately train their employees on heat illness. In addition to employee training, the proposed standard has specific requirements for Supervisor training, which must include the following:
Prior to supervising employees performing work that should reasonably be anticipated to result in exposure to the risk of heat illness, effective training on the following topics shall be provided to the supervisor:
The information required to be provided by subsection (h)(1).
The procedures the supervisor is to follow to implement the applicable provisions in this section.
The procedures the supervisor is to follow when an employee exhibits signs or reports symptoms consistent with possible heat illness including emergency response procedures.
Where the work area is affected by outdoor temperatures, how to monitor weather reports and how to respond to hot weather advisories.
You must also have a written Heat Illness Prevention Plan (HIPP) just like you do for Outdoor Heat Illness, which must include procedures for access to water, access to cool down areas, how to measure temperature and heat index, emergency response procedures and procedures for close observation of employees during acclimatization.
Now it goes without saying that we must provide a safe work area for our employees, but do we have an issue in our farm shops, hullers and processors? Most facilities provide fans, portable coolers and water wherever possible. We also use these buildings to allow our outside workers an area to cool down. In researching, the cost to get our facilities down to below 87 degrees F would be more than $1 million for air conditioning, which in some cases such as hullers or walnut dehydrators are impractical or would work against the operation.
The proposed standard says that engineering controls shall be used to reduce and maintain the temperature and heat index to below 87 degrees F except to the extent the employer demonstrates such controls are “infeasible.” Unfortunately, the proposed standard does not define “infeasible”. Therefore, the Association was able to provide specific testimony in an opportunity only provided to the Association, making the case that installing a/c systems big enough to cool a huller or processor would be too costly or work against the operation such as a walnut dehydrator.
So where does it go from here? We know that more than 400 pages of comments were submitted on the proposed regulation, but there is a legislative mandate to adopt an indoor heat illness regulation so we know one will be adopted. We just don’t’ know what the final regulation will look like. Stay tuned.
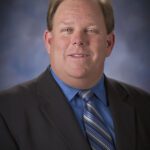
By Roger A. Isom | President/CEO, Western Agricultural Processors Association
Roger is President/CEO of the California Cotton Ginners and Growers Association and Western Tree Nut Association. He brings over 30 years of regulatory and legislative advocacy experience, specializing in environmental and safety matters. Roger’s responsibilities include the management of both Associations’ staff and day-to-day operations. Roger is also the President of the Ag Energy Consumers Association (AECA), board member and Past President of the Ag One Foundation at California State University Fresno, and manages the Navel Orangeworm Action Committee (NOWAC).