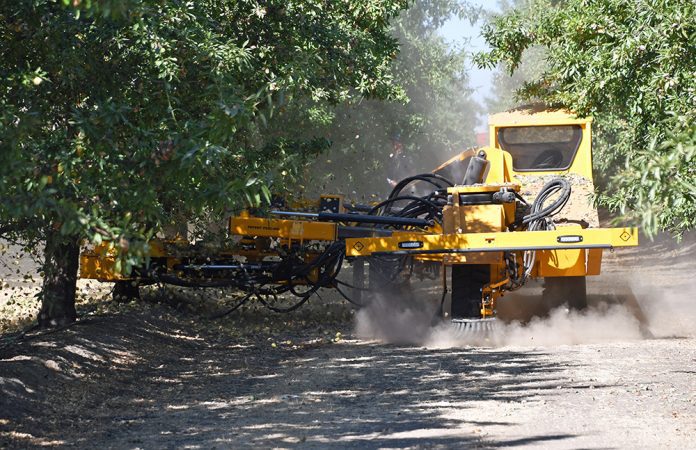
When Orchard Machinery Corp. launched a nut shaker with self-steering capabilities and sensor-driven tree positioning a few years ago, it was only a matter of time before the company developed a fully autonomous machine.
The Yuba City manufacturer of orchard equipment did just that with the new Shockwave X, a self-driving machine that uses vision guidance and a patent-pending head to continuously shake nut trees.
“It’s really going to be a game changer for the industry,” said OMC President and CEO Tobbie Wells. “One of these machines can replace a driver and shake seven, eight, even nine trees per minute. With commodity prices, you’re not going to see it on the revenue side. It’s on the expense side where we’re looking to get traction.”
A certified public accountant by trade, Wells said the machine should provide calculated savings of up to 60% over four years.
During this year’s harvest, OMC demonstrated a prototype model in almond orchards up and down the Central Valley to strong grower interest.
Ryan Winters of Winters Farming Inc. in Manteca said they decided to host a demonstration because they saw the technology as a potential way to address labor issues.
“Anything we can do to try to advance a solution to that need, we’re all about it,” he said. “It’s pretty intriguing.”
Dave Wheeler and his son, Wrangler, who farm almonds and row and forage crops near Modesto, said there’s no doubt they’ll eventually buy one of the autonomous shakers.
“With the way labor is and the liability and availability, you can’t afford not to,” Wrangler Wheeler said.
Even their best operators only shake five trees per minute, and “at the end of the day, they’re tired,” Dave Wheeler said.
Both also said they were impressed with the new Shockwave design. Rather than stopping at each tree to extend the shaker arm to clamp onto the trunk and shake the tree, the machine continued to move throughout the process.
The Autonomy Revolution
Winters and the Wheelers aren’t alone in their concerns about finding workers. Walt Duflock, vice president of Innovation with Western Growers and a fifth-generation Monterey County farmer, said massive decreases in available farm labor throughout the specialty crop industry are driving the autonomy revolution.
In the 1950s, the nation’s farmers employed about 10 million farm workers, he said. Currently, about 2.4 million people plant, till and harvest crops.
Some of the decrease is due to mechanization. Taking up some of the remaining slack are an increasing number of H-2A temporary ag workers, which has risen from about 48,000 nationwide in 2005 to 371,000 in 2022. But they haven’t made up the entire gap.
Minimum wages also continue to climb in a number of large specialty crop producing states, increasing growers’ overall costs and affecting the H-2A prevailing wage.
“It’s a massive economic challenge for specialty crops, and the only way out of that is to automate,” Duflock said.
Where he has seen the largest technological growth is on the processing fruit and vegetable side with autonomous weeding, planting and harvesting. While growing and harvesting nuts already was already fairly mechanized, he said there’s still room for growth.
“Nuts are probably leading the pack,” he said. “
Duflock said he doesn’t necessarily see technology eliminating farm worker jobs but instead shifting responsibilities from manual labor in fields to servicing machines.
“All of this new technology creates bigger and bigger skill-set problems,” he said. “We need more people as farming operations do more with ag technology.”
Already, Duflock knows of larger grower-packer-shippers who have begun to retrain crew members to support the latest technology.
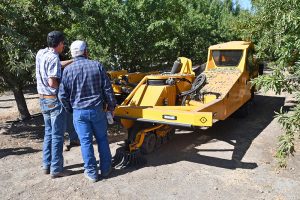
Patent-Pending Shaker Head System
The first formal Shockwave X model rolled off the OMC assembly line in early fall, and an additional 12 are slated for completion in time for winter sanitation and shaking mummy nuts, Wells said. Software and hardware upgrades to the shaker are available via an annual subscription.
Currently, the shaker can navigate autonomously down the tree row but needs a human to turn it and guide it into the next row.
OMC already has self-turning technology in its 200 hp Aftershock AR500 shuttle truck that has a 9-foot turning radius. The modular rear-frame system also allows users to hook up sprayers, spreaders or other implements.
Autonomous shakers purchased this winter and bundled with the annual service subscription will be fully upgradeable in the future to allow for self-turning, and units manufactured in 2024 will come standard with the feature, Wells said.
OMC has taken a shaking arm mounted on a slider and pivot and added novel shaking heads to develop a patent-pending system. Wells said each of the components individually isn’t necessarily earth shattering. What is innovative and worthy of a patent is the combination that allows the machine to continually move while shaking.
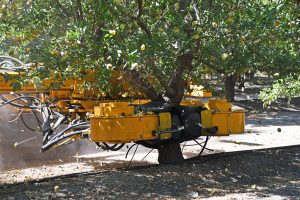
As the shaker arm approaches a tree, the right-hand head is extended nearly straight out from the arm and makes first contact with the trunk. It is followed by the left-hand head that closes around the trunk from about a 90-degree angle.
Shaking ensues, after which the right-hand head releases first. All of this occurs as the machine continues moving down the row and the shaker arm slides and pivots. By the time the shaker reaches the next tree, the heads have returned to their starting positions.
With 14-foot tree spacings and a shaker speed of 1.5 mph, the machine can harvest almost eight trees per minute, said OMC Vice President Brian Andersen. That’s far more than the industry average of less than five per minute.
‘It Literally Has Eyes’
Earlier this year, San Jose-based Bonsai robotics approached OMC about a collaboration, and Wells said it made sense. After all, Bonsai founder and CEO Tyler Niday had previously worked for OMC before joining John Deere’s Blue River Technology, where he led various autonomy projects, including the autonomous 8R tractor, for more than six years.
Bonsai also has an 800-acre orchard and vineyard near Davis where the company can conduct real-world tests on technology.
The Shockwave X relies solely on vision guidance from five ruggedized automotive-grade cameras for navigation and 360-degree coverage, Niday said.
“It literally has eyes,” Wells said.
It does not use GPS or LiDAR (light detection and ranging), so it can work under tree canopies, under dusty conditions or at night where other technologies might fail, Niday said.
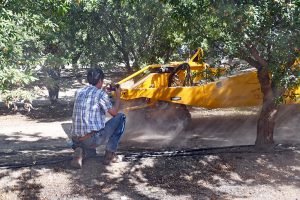
Users simply enter a georeferenced orchard boundary, but they don’t need to map every tree row using GPS as part of machine guidance, he said.
Machine-mounted cameras feed information to an on-board computer, which turns the data into 3D images. In a fraction of a second, the computer uses machine learning and artificial intelligence (types of high-speed computing on steroids) to compare the images to those in one of the world’s largest databases of orchard images.
Based on the results, the computer instructs the shaker on the next move. The more the shaker operates, the more images it collects and the more machine learning improves its operation. It has an accuracy of plus or minus 2 inches.
“As we collect more data, we get smarter and smarter,” Wells said.
She compared it to watching a movie you’ve seen before a second or third time; you naturally pick up on details you may have missed the first time.
The computer also is able to differentiate between telephone poles and tree trunks, Niday said. It also can tell whether it’s approaching a mature tree or a thin-trunked replant. In the future, he said they plan to have a function that will automatically raise or lower the shaker head to accommodate for low tree crotches or low-hanging branches.
The camera system is designed with safety redundancies and will stop the machine if it detects humans, obstacles or unusual movements, he said. The computer simultaneously sends a stoppage alert via cell signal to the supervisor, who can determine whether to restart the machine remotely or visit the site in person to remove the obstacle.
In addition, OMC has partnered with Topcon for telematics that allow users to remotely monitor operations, including alerting them to engine maintenance and monitoring operator efficiency, fuel efficiency, drive patterns and upcoming repairs.
A 174 hp Cummins Tier 4 diesel engine powers the Shockwave X. The engine also is Stage 5 compliant for use in the European Union, Andersen said.
Based on average fuel consumption, the 54-gallon diesel tank can run for more than 14 hours before needing a refill.
Shaker operations can be monitored on a tablet or smartphone, and Niday said he envisions one person supervising as many as four autonomous shakers at a time.
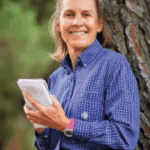
Vicky Boyd | Contributing Writer
A veteran agricultural journalist, Vicky Boyd has covered the industry in California, Florida, Texas, Colorado, the South and the Mid-South. Along the way, she has won several writing awards. Boyd attended Colorado State University, where she earned a technical journalism degree with minors in agriculture and natural resources. Boyd is known for taking complex technical or scientific material and translating it so readers can use it on their farms. Her favorite topics are entomology, weeds and new technology. When she’s not out “playing in the dirt,” as she calls agricultural reporting, Boyd enjoys running, hiking, knitting and sewing.