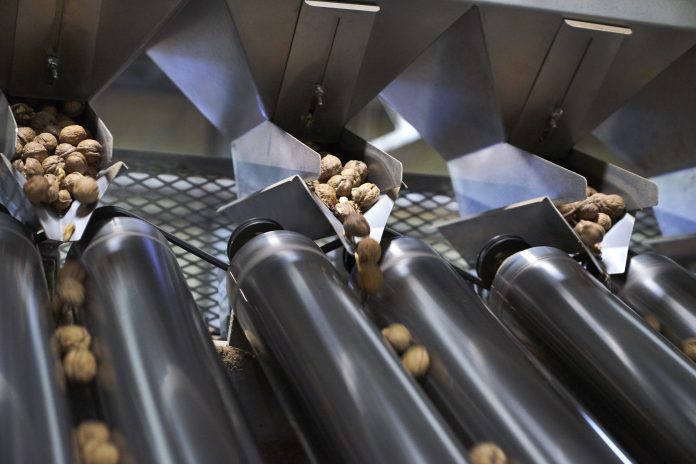
Every year, Cal/OSHA publishes the top 10 most cited safety standards, and the LOTO standard is consistently in the top 10 every year since 2014. In the most recently released list for 2022, Cal/OSHA reported the most cited and appealed violations with Control of Hazardous Energy, Including Lockout/Tagout ranking in at No. 6. With Lockout/Tagout being among the top concerns, it is important employees understand and are familiar with the company’s Lockout and Tagout procedures and all the key elements of the regulation are met.
The Lockout/Tagout (LOTO) procedures, or hazardous energy control procedures, outline the specific procedural steps for each piece of machinery or equipment. When equipment is properly shut down, it reduces the risks of accidents and injuries from an unexpected startup. Whether it be during cleaning, servicing, adjusting operations, un-jamming or when an employee places any part of body in contact with point of operation, LOTO procedures should be implemented properly.
Some key elements of the regulation include a lockout/tagout written program, periodic inspections, certifications, training, machine specific procedures and lockout devices. Let’s take a closer look into some of the key elements.
Machine-Specific Procedures
In 1974, Cal/OSHA required machine-specific procedures for each piece of equipment in a facility. As mentioned, LOTO procedures are written-out procedures that outline the steps of each piece of machinery in your facility, including but not limited to mobile equipment such as tractors and any other piece of equipment that will require servicing by the employee. The written LOTO procedures will include the name and location of equipment; identity of hazardous energy sources, such as electrical, mechanical, pneumatic, hydraulic, etc.; procedural steps for location and method of application of hazardous energy control devices; and procedural steps for shutdown and restart of equipment.
These procedures should be followed when performing routine tasks where an employee is servicing, repairing, unjamming or unchoking a machine. For instance, out at the stockpile yard, through the unloading process debris can sometimes jam the elevator, and when unjamming occurs, employees must follow LOTO protocol to remove the blockage. Consequently, uncocking or unjamming can be an overlooked practice when it comes to LOTO procedures. It is extremely important that everyone follows machine-specific procedures to reduce the risk of injury.
Periodic Inspections of Procedures
During the season, you may find yourself needing to modify or replace your equipment to meet the season’s needs, and the question is how do we ensure that any new equipment gets included in the LOTO procedures or our procedures are up to date? With an annual periodic inspection conducted by an authorized employee, one can ensure any new equipment or modification is included in the LOTO machine-specific procedures.
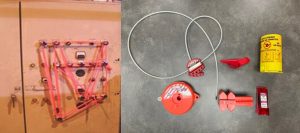
Training
Another key element of the regulation is training. Training should be provided to all employees to some degree. Employees who will be involved in the lockout and tagout process (authorized employees) should have an in-depth understanding of the regulation, procedures, hazards, energy sources and how to apply lockout/tagout devices. Affected and other employees must also receive training and have a general knowledge of LOTO. To ensure training is effective, apply practical demonstrations and small group discussions alongside exercises in their language at a level they can understand.
When training is not adequate, devastating consequences can occur. As reported by the Cal/Osha Reporter, a death at a paper company in Moreno Valley occurred in 2022 was noted with the 58-year-old employee being crushed inside a recycling baler by climbing into the hopper to remove a jam. The employee suffered a fatal injury due to lack of implementation of LOTO procedures and training, and this company faced hefty penalties of more than $68,000 in proposed penalties. It is crucial to provide training to employees to reduce risk of injury.
Certification
After the training, you must verify the employees understand the procedures. This can be achieved through certifying authorized employees annually. The certification of the authorized employee includes a review in which the authorized employee demonstrates knowledge and skills required for identifying the specific procedures for a certain piece of equipment or machine. The following elements are evaluated during the certification:
- The identity of the machine or piece of equipment that will be utilized
- Listed shutdown and restart procedures to show competency and understanding
- Date of certification
- Employees included in certification, including the person performing it
- Apart from being a requirement, the evaluation of procedural steps for shutting down and reenergizing equipment is to help provide a reinforcement/refresher and ensure steps are being followed by employees.
Lockout Devices
Lockout devices are also an essential part of the program. The devices used in the LOTO program such as tags and locks must meet certain requirements. They must be durable and substantial, easily identifiable and used for LOTO purposes only. The energy isolating device is a mechanical device that physically prevents the transmission or release of energy for electrical, mechanical, pneumatic, hydraulic or any other hazardous energy. Examples of these tools are locks, blocks, blocks for valves, cable locks, plug lockout canisters and others.
As the end of the year and season for some is approaching, we would like to remind folks to remain vigilant and ensure LOTO practices are being followed. Injuries and accidents can be reduced by including in the LOTO program machine specific procedures, periodic inspections, certifications, training and lockout devices. It’s everyone’s responsibility to ensure a safe workplace environment, proper LOTO procedures and related programs go a long way in ensuring the necessary safety environment. Be vigilant!