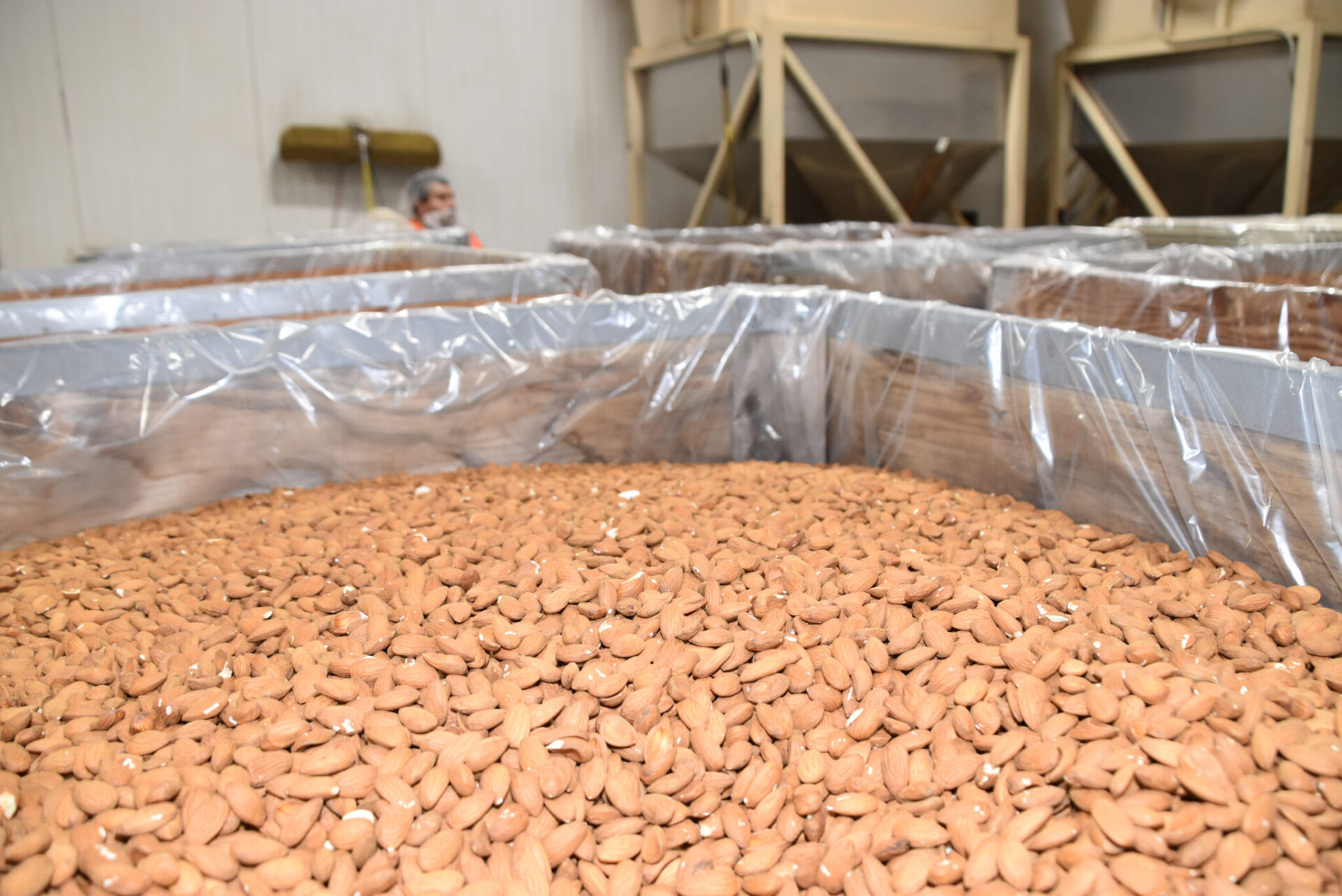
Admitted innovators, the family members behind Travaille and Phippen Inc. embrace technology to improve their production efficiency and bottom line and manage a dwindling labor pool. So, when Scott Phippen, one of the partners in the Manteca-based almond grower and processor, stopped by a World Ag Expo booth that featured robotic corn seed sorting several years ago, his interests were piqued.
“’What do you think about robotics for sorting almonds?’” Scott Phippen said, recalling a question posed by Eric Pflueger of Bratney Cos. “I said, ‘I think that’s real interesting. Can you do it?’ They were wanting to try it, and I said I’m up for that. The next thing I know, a contingent was here from Des Moines, which was where they were headquartered.”
Travaille and Phippen partnered with Bratney Cos. to develop a prototype and eventually installed four lines, each featuring two pick-and-sort robots, in 2013. Now they are working with Premier Tech, a Canadian firm that acquired the patent from Bratney, to develop the next generation of robotic sorters that uses artificial intelligence.
As Scott Phippen and his brother, Dave Phippen, were quick to point out, robotics won’t turn a poor quality crop into a good one. Instead, they view the technology as one of the final steps to ensure a high-quality product that begins with proper cultural practices in the orchard, timely harvest, knowledgeable post-harvest handling and careful shelling steps.
Batting Clean-Up
Travaille and Phippen hulls and shells its own almond crop as well as those from other growers. Nearly all of their nuts go to export as brown skins, with much of the volume destined to discerning high-end markets.
As such, the Phippens said they’re focused on growing and producing a quality product that far exceeds USDA’s Fancy grade, which allows for 5% chipped or scratched kernels and 2% other defects, among other tolerances.
Even before the nuts reach the robotic sorters, the Phippens run them through several machines and optical sorters to remove most of the extraneous material and defective kernels.
The robotic sorting system relies on cameras above the conveyors to image each nut as it goes by. It then sends the data to a computer, which determines whether the nut is sound or needs to be removed. Should the nut or extraneous material need to be culled, the computer sends a message to the robotic picker, which vacuums it up in an instant and sends it via a pneumatic tube to a bin. All of this occurs in a fraction of a second.
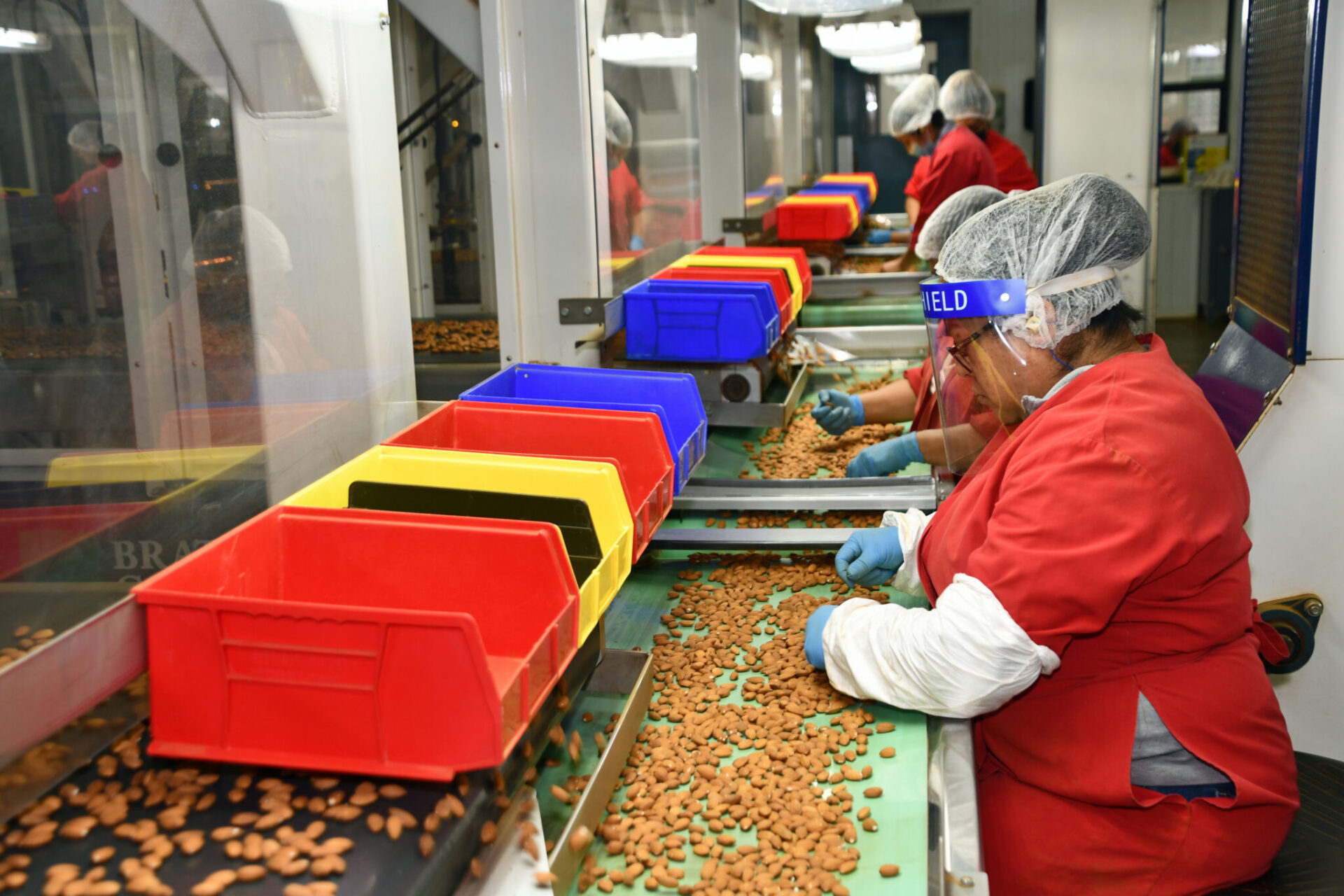
A human eye relies on the RGB, or red, green and blue, spectrum. This also is referred to as visible light.
The current cameras over the sorting belts use hyperspectral imaging, which involves a multitude of light wavelengths ranging from 400 to 1,000 nanometers, said Pflueger, who now works for Premier Tech.
The next-generation sorter uses very high-end RGB imaging. Each image also carries a spectral signature. As the computer accumulates the signatures, it continues to “learn about crop characteristics” using artificial intelligence. This only improves its decision-making capabilities.
In fact, Pflueger said, the new system can class individual nuts as they pass under the camera.
“At the end of the day, we can tell you exactly what’s in that bin because we have classed everything that’s come through,” he said. “It also monitors what’s going into the bin because we have sensors going into the bin—something we didn’t do before.”
Plans for the Future
One of the issues the Phippens had with the old system is it dumped all of the culls into one bin. Then he had to re-sort it to remove nuts that were just chipped or scratched and could go into a processed product such as almond milk, those with worm damage or mold that would go to animal feed, and other culls such as shell that were not consumable.
The new system can separate the defects into different categories and different bins, such as three in the case of Travaille and Phippen, Pflueger said.
The old system also relied on two robotic arms per line, and each robot transited the entire width of the belt. The new system uses four robots per line, and each robot covers slightly more than half of the belt width, with an overlap in the middle. Because the robotic arms don’t have to travel as far, belt speed can be increased. Belts with the old system typically ran up to 34 feet per minute, whereas the new belts can run up to 60 feet per minute.
The actual speed of the system and sorting belts depends on the cleanliness of the crop and buyer specs. But Scott Phippen said they try to shoot for 3,000 pounds per line, or 12,000 pounds per hour, with the old system, and they run 12 hours per day six days a week.
Currently, the enclosed room where the nuts are sorted houses four lines with two robots each. Because the new robots require a slightly narrower support frame and conveyor belt, Scott Phippen said he hoped to squeeze in six lines of four robots each to increase their throughput. Installation of the new system could begin as early as the next few months.
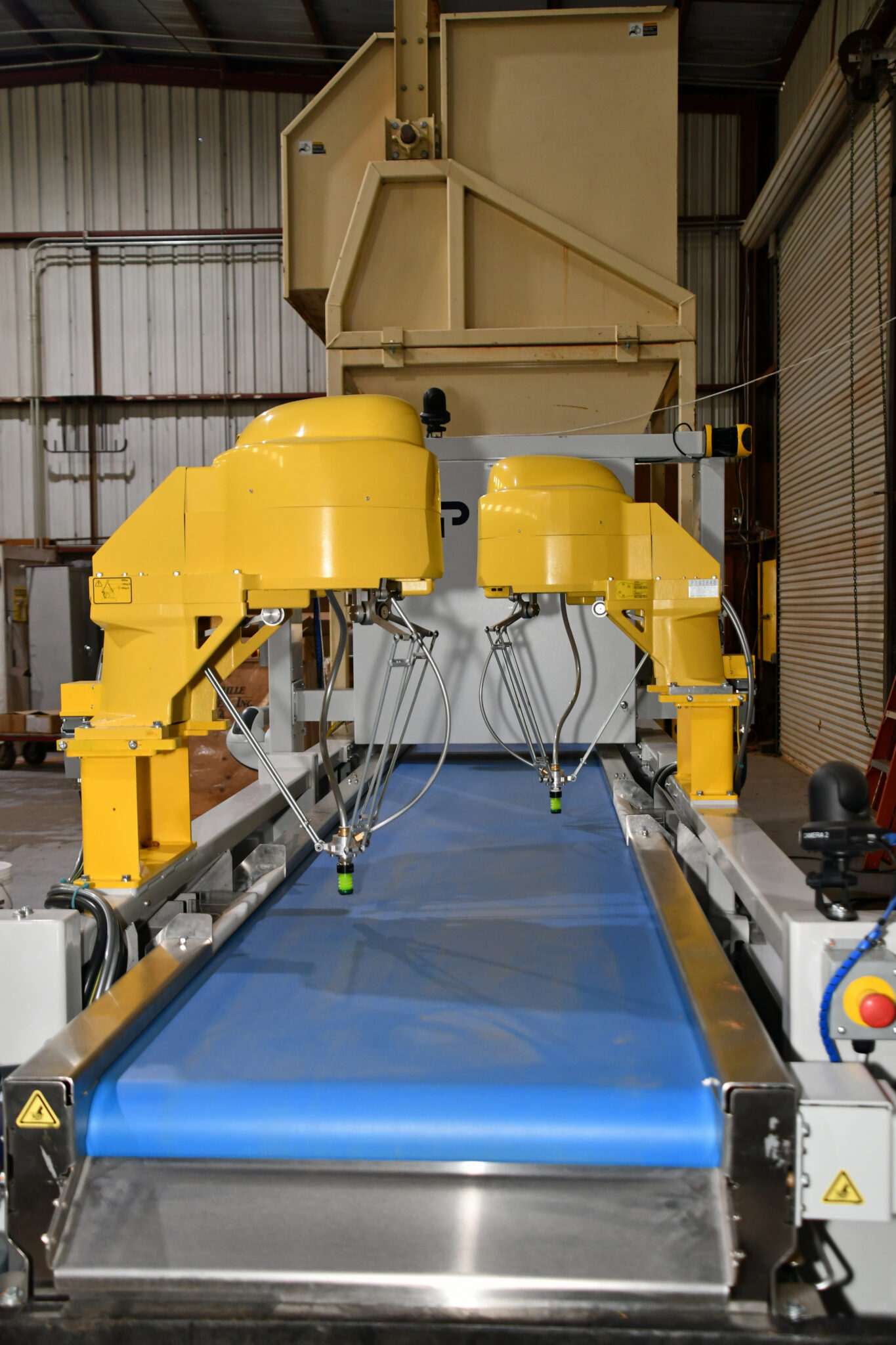
A Place in Pecans
While sound almond kernels have a fairly smooth surface, pecan kernels are just the opposite with deep crevasses and ridges. But the latest developments in imaging can provide views of hidden defects, Pfleuger said.
He recently installed a four-robot, single-line system in a Valdosta, Ga. pecan processor that runs around the clock. Each robot can do 100 picks per minute, or 400 picks per line per minute, without a decline in sorting caliber as the shifts wear on.
Unlike most almonds in California, pecans are infrequently grown in managed orchards and harvested in a timely manner. Instead, a landowner may have a handful of trees, collects the nuts in buckets or burlap sacks after they fall and sells them to a processor.
As a result, sticks, rocks and other debris are often mixed in with the nuts. Pecan quality also varies widely.
In addition, pecan kernels are more fragile and contain significantly more oil than almonds, further complicating sorting, Pflueger said. That means scrapers, pneumatic lines and other parts of the sorting system have to be cleaned or replaced more frequently to prevent damaging oily buildup.
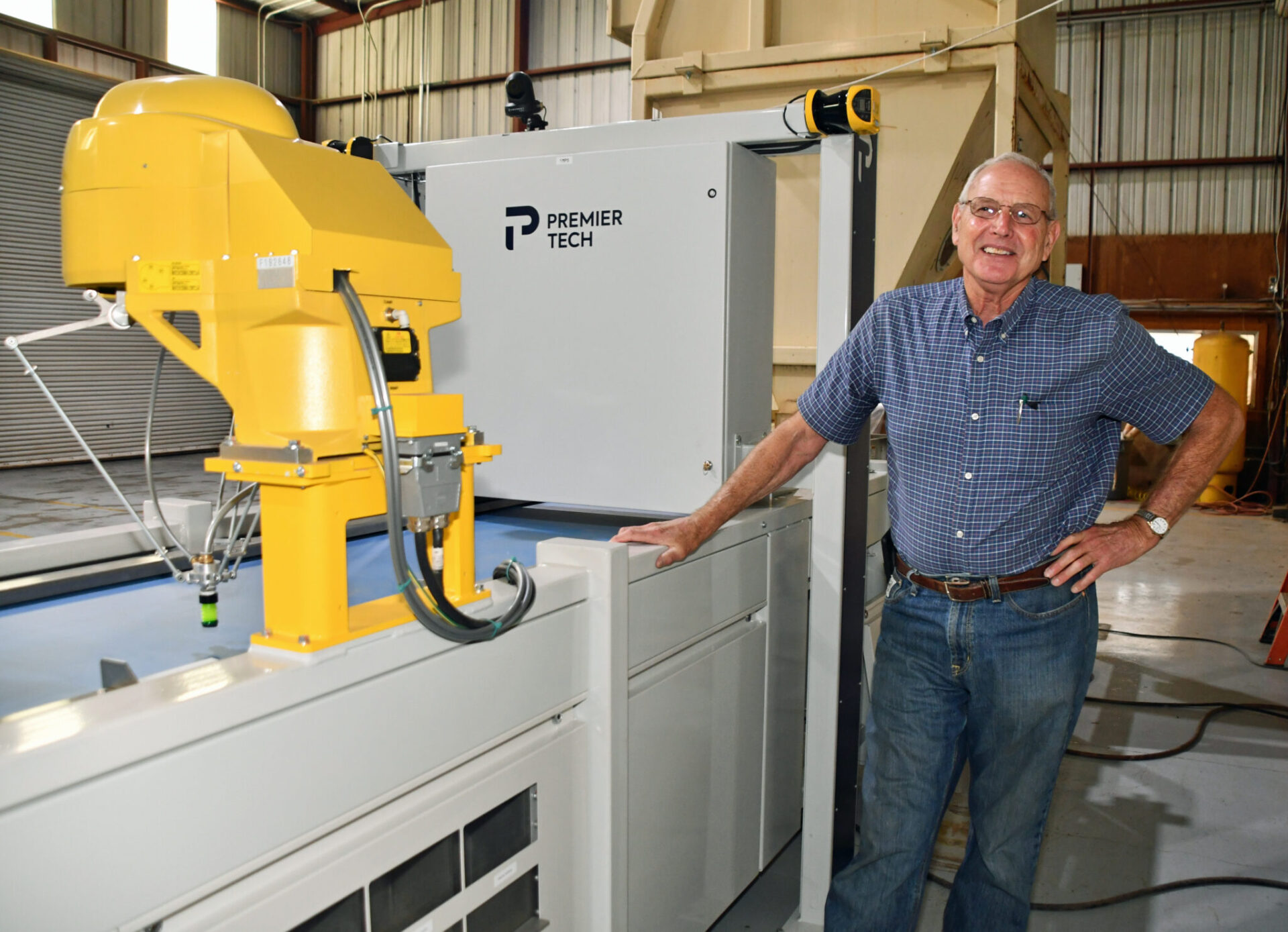
Worker Availability Remains an Issue
Dave Phippen said their agreement with Bratney prohibited them from talking about the cost of the first robotic system. But he said they’re on the positive side of obtaining a payback on their original investment.
The Phippens said they began thinking about replacing their old robotic system after Bratney quit supporting it. In addition, the technology became obsolete.
What attracted them to Premier Tech was the company had the various divisions, such as computing technology and engineering, all in-house. So, one call typically resolves an issue.
“These guys have horsepower,” Scott Phippen said.
Dave Phippen said they originally looked at robotics in the early 2010s because of challenges finding workers, which has only grown worse.
“It was very difficult to get labor, even back in those days,” he said. “I just want to know my labor will show up and is healthy.”
Nevertheless, Dave Phippen said, the operation will continue to employ a small hand sorting crew to give the nuts a final once-over after they exit the robotic sorters and before they go into the box.
“We’ll always have hand sorters because we sell to the upper-end markets,” he said.
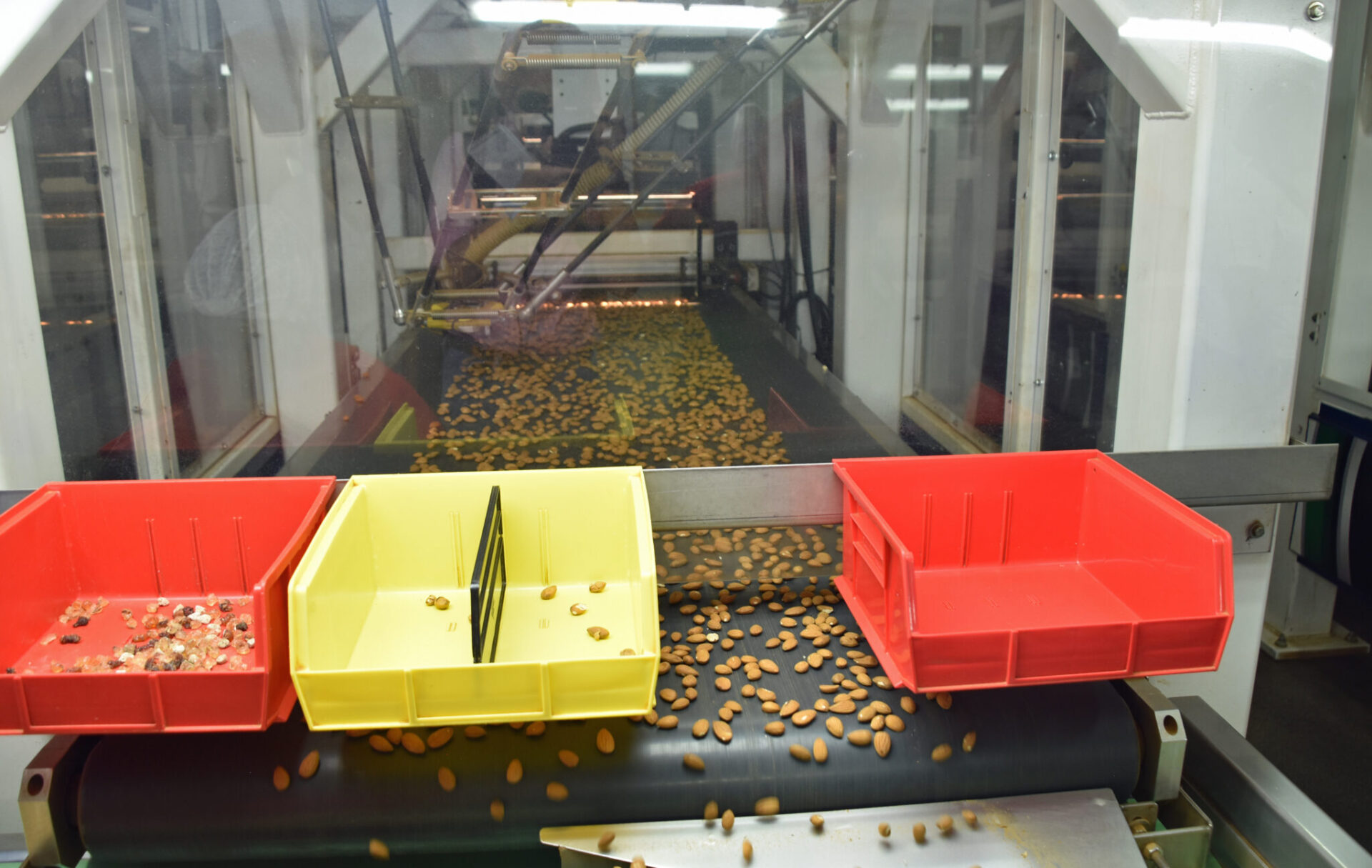