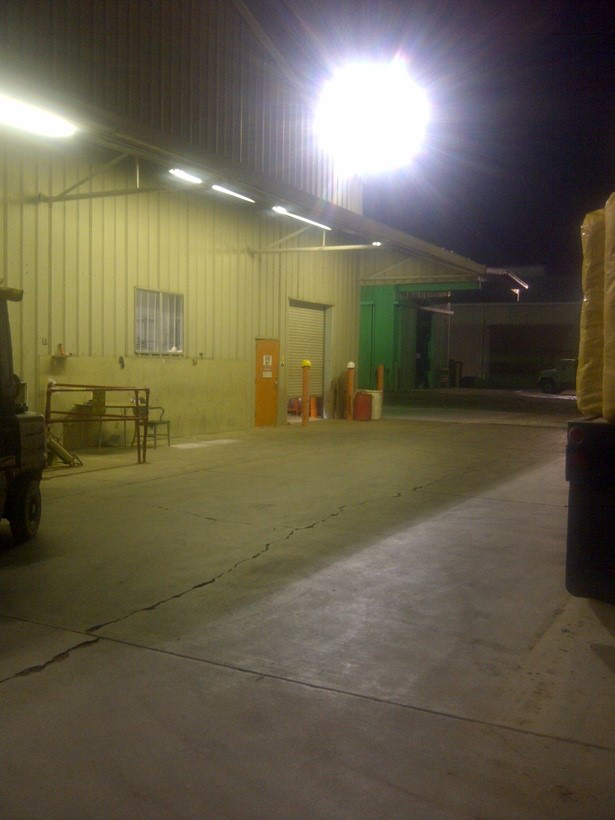
Are you operating at night around the huller or on the farm? In June 2020, the Standards Board for the California Occupational Safety and Health Administration (Cal/OSHA) adopted new lighting workplace standards for protecting agricultural workers who harvest, operate vehicles and perform other jobs between sunset and sunrise. The new regulation requires agricultural employers to evaluate areas of outdoor worksites to determine if the present lighting levels are within the specifications established by the standard.
The goal in establishing this requirement is to implement protective measures that improve visibility of workers by operators of farm equipment and vehicles, and ensure workers have adequate lighting depending on the area they are operating in and the task they are preforming. Supervisors must conduct safety meetings at the beginning of every shift to inform workers about their surroundings and high traffic areas.
General Requirements
Agricultural equipment, including tractors, harvesters and trucks, must have at least one headlight to illuminate the front of the equipment at least 50 feet in front of the equipment. For all other operations occurring at night, the standard requires agricultural employers to meet specific illumination levels (Table 1).
Required illumination levels can be met by providing hands-free portable lighting and/or area lighting. It is important to note that these illumination levels should be measured by a meter. These meters can be purchased from typical equipment supply companies like Grainger. Look for meters from Flir, Extech or similar.
The Association recommends conducting a site assessment, by taking light measurements at night in those areas where activities can or may occur in. A critical area is the loading or unloading of stockpile bins onto or from trucks. Be sure to take light measurements in these critical areas. Once you know the actual light levels, you can decide on how to address any deficiencies or make changes to avoid low-light areas. A well conducted site assessment is critical to a successful plan.
Safety Meetings
There is a specific requirement for “safety meetings” for this regulation. It mandates that supervisory employees conduct a safety meeting at the beginning of each shift to inform employees of the location of the restrooms, drinking water, designated break areas and additional hazards, such as nearby bodies of water and high-traffic areas. For most tree nut facilities, this should not be a huge issue as these typically don’t change much, but it is important to make sure employees know these areas and are reminded of them. Farming or field operations may have additional information to cover with employees as work crews move to different worksite locations. While not required, the Association strongly encourages you to document these meeting as well as who attended them.
Personal Protective Equipment (PPE)
This particular regulation mandates the employer provide and require workers to wear Class 2 high-visibility garments conforming to the specifications of the American National Standard for High-Visibility Safety Apparel and Accessories (ANSI/ISEA) 107-2015 for any work activities that occur between sunset and sunrise. This requirement is a good safety practice as Class 2 high-visibility vests that meet this standard are inexpensive and readily available. Many tree nut facilities make this a standard requirement as other conditions, such as fog in the winter, sometimes makes it difficult to see people. Reflective clothing helps improve visibility immensely.
While this is another one of those California-only regulations, there are some aspects of this regulation that make sense, such as wearing the reflective vest or other clothing. Being visible is the most critical point here, and the reflective clothing will definitely help.
For those that need assistance in meeting these requirements or need help understanding this rule, please feel free to contact the Association Offices.
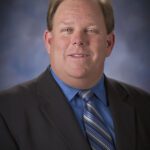
Roger A. Isom
Roger is President/CEO of the California Cotton Ginners and Growers Association and Western Tree Nut Association. He brings over 30 years of regulatory and legislative advocacy experience, specializing in environmental and safety matters. Roger’s responsibilities include the management of both Associations’ staff and day-to-day operations. Roger is also the President of the Ag Energy Consumers Association (AECA), board member and Past President of the Ag One Foundation at California State University Fresno, and manages the Navel Orangeworm Action Committee (NOWAC).