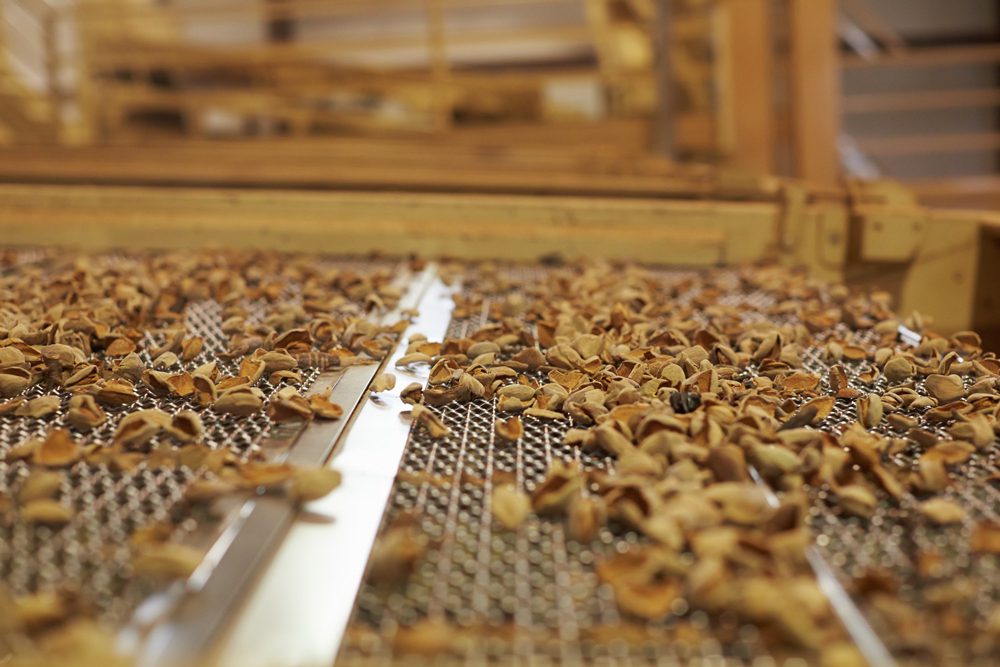
Almond hulls and shells represent approximately 70% of the almond fruit weight that comes out of an orchard each year, but they account for only 3% of revenues gained from harvest. Guided by years of strategic research and investment, the Almond Board of California (ABC) seeks to narrow that gap by developing higher-value uses for hulls and shells, once simply thought of as byproducts of the almond growing process. For growers, that could mean lower costs for hulling and shelling and a better return for hullers, too.
“We’re at a pivotal point of shifting from thinking about biomass as just a research program,” said Josette Lewis, ABC’s chief scientific officer. “We know lots of things are possible, so the next step is promoting the development of commercial markets for new products that research shows are technically feasible with hulls, shells and woody biomass.”
With projected coproduct biomass estimated to be as much as 2.2 million tons of hulls, 900 million tons of shells and 1.3 million tons of wood per year by 2025, that large volume either offers potential new revenue opportunities, along with market differentiation for almonds as a zero-waste industry, or simply a waste challenge.
New Markets for Coproducts
With mountains of hulls and shells to move, raising the value of these coproducts for the industry will require developing multiple new markets. The economics are simple; as supply of almond coproducts has increased steadily, the price has decreased. The development of new outlets for coproducts can create healthy competition in the marketplace with the prospect for higher returns.
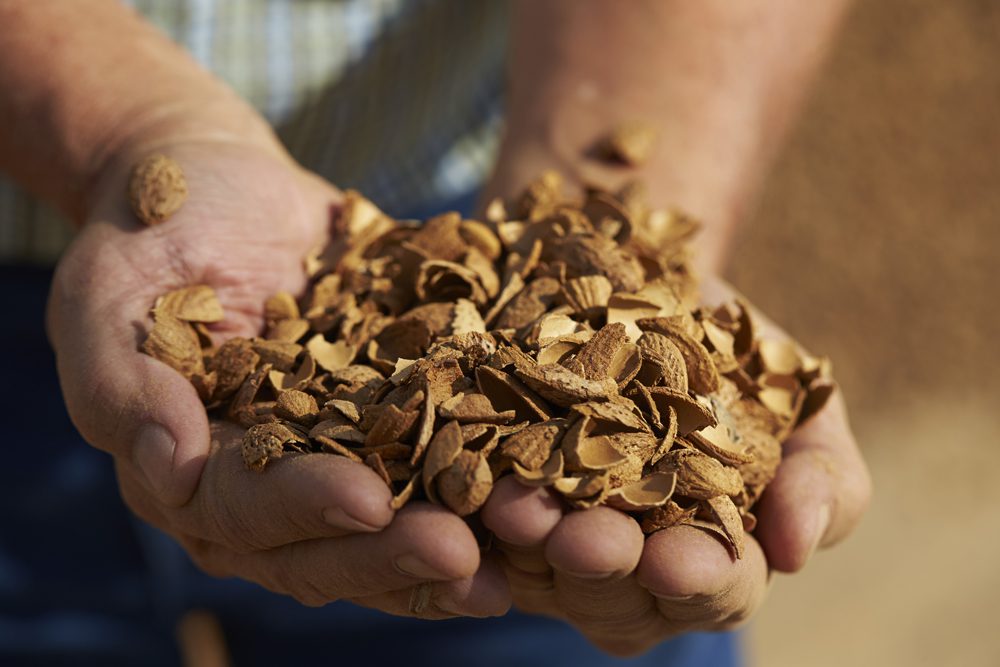
Achieving positive potential for the industry is the rationale for the $2 million ABC has invested over the last five years in biomass research projects. The research is guided by industry volunteers who serve on the Biomass Workgroup, now under the Strategic Ag Innovation Committee. The Working Group and the Board of Directors are now in the process of reviewing results of a commercial biomass market assessment to prioritize the opportunities to start with and then define tactics for development of those markets.
“We commissioned this assessment of the market opportunities for almond biomass to look at a full range of factors; what makes almond biomass unique that might make it a preferential feedstock when compared to products that already exist, or have a better cost of goods,” Lewis said.
Almonds Hulls as Feed
For decades, dairy producers have used almond hulls as a source of fiber and digestible carbohydrates in their cows’ feed rations. According to Guangwei Huang, ABC’s associate director of Food Research and Technology, recent studies confirm the potential value of almond hulls in feed applications.
“Our recent research shows dairy cows can consume as many as 12 pounds per day, more than the three to five pounds used today, with no adverse effect on milk production,” Huang said. “With more than 1.7 million dairy cows in the state, part of our strategy includes communicating this to dairy producers.”
There is no question that almond hulls have a beneficial feeding value, but they are often treated as an inferior feed alternative, and priced as such, due to inconsistent quality. Shells, sticks and other debris can discourage dairy farmers from using a higher hull content in their daily rations. Therefore, the purest form of almond hulls with the least amount of foreign material will demand the greatest value.
Huang noted the Workgroup is exploring several tactics to expand hull use in dairy feed that will also return more value.
“First, we have to demonstrate the economic value to the huller/sheller for providing more consistent hull quality for the feed industry,” he said. “This might include the use of conditioners at harvest to deliver cleaner materials to the huller/sheller and the establishment of practical hull grades as an industry best practice for consistent delivery to return more value.”
Poultry Shows Promise
A growing body of ABC-funded research suggests additional comprehensive benefits of feeding broilers (poultry raised for meat) and layers (poultry raised for egg production) a diet that includes ground almond hulls.
“We already know that almond hulls can replace 9% to 15% of a bird’s energy ration,” Huang explained. “In addition, we have found unexpected benefits from the high fiber and phytochemicals found in almond hulls.”
University of Georgia found that the high fiber content of hulls can reduce salmonella infection and localization, while the phytochemicals improved the antioxidative activity in the liver, making broilers less susceptible to a common internal parasitic infection called coccidiosis.
“There is also additional functionality that we are starting to understand in broilers and layers,” Huang said. “In the layer study, we learned that a diet that includes almond hulls improves the composition of the egg yolk.”
Researchers observed an improvement in the lipid profile of the egg yolk, including an increase in polyunsaturated fats. For consumers, polyunsaturated fats are considered “healthy” fats that include omega-3 and omega-6 fatty acids, which are essential for brain function.
According to Huang, the almond industry is just starting to understand the comprehensive benefits to the poultry industry.
“Expanding use of hulls in more livestock industries is one of the priority areas for market development,” Lewis said.
Food Grade Uses Offer ROI Potential
Whole almond hulls are unlikely to gain popularity as the next health food craze, but emerging technologies are opening the door for the use of whole hulls and hull-extracted ingredients derived for a variety of food products.
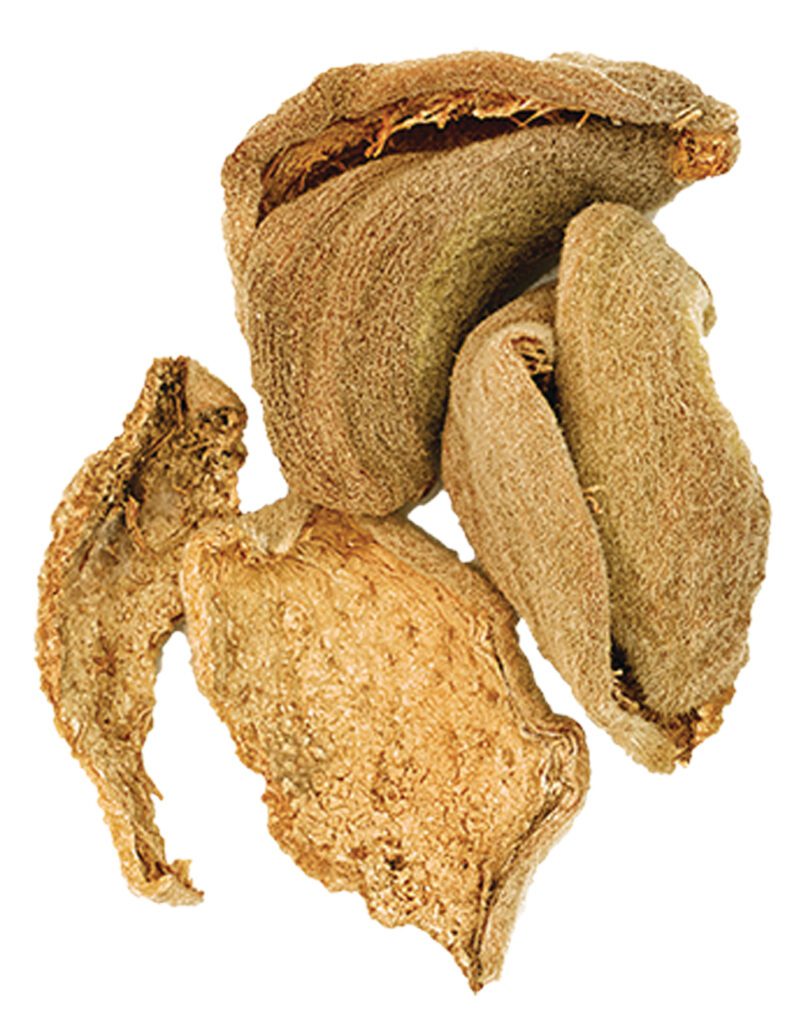
Almond hulls contain 36% dietary fibers, including 6.5% soluble fiber, and hulls are reported to contain up to 42% extractable sugars on a dry matter basis, including about 9% non-fermentable sugars.
A research team funded by ABC has created several ingredients from almond hulls for a variety of functional foods, foods designed to have a potentially positive effect on health beyond basic nutrition. These food trials include functional dietary fibers, emulsifiers, functional syrup, antioxidants and a functional beverage drink powder.
“The products made from hull-derived ingredients have shown greater processing functionality and antioxidant capacity than popular commercial products,” Huang explained.
The market assessment identifies a nutritional bar containing multiple hull-derived components as an opportunity which takes advantage of the unique combination of fiber, sugars and antioxidants together. The Biomass Workgroup is considering various tactics to further develop the market for hull-derived foods, including building the food safety dossier, taste pairings and outreach to the food industry.
Almond-enhanced Plastic
Almond-enhanced plastic can provide a new market for producers and address some challenges facing plastic manufacturers.
“Plastic that includes torrefied almond shells is beneficial to manufacturers; they can make stiffer, stronger, and more heat-resistant composites than traditional plastics,” Huang said.
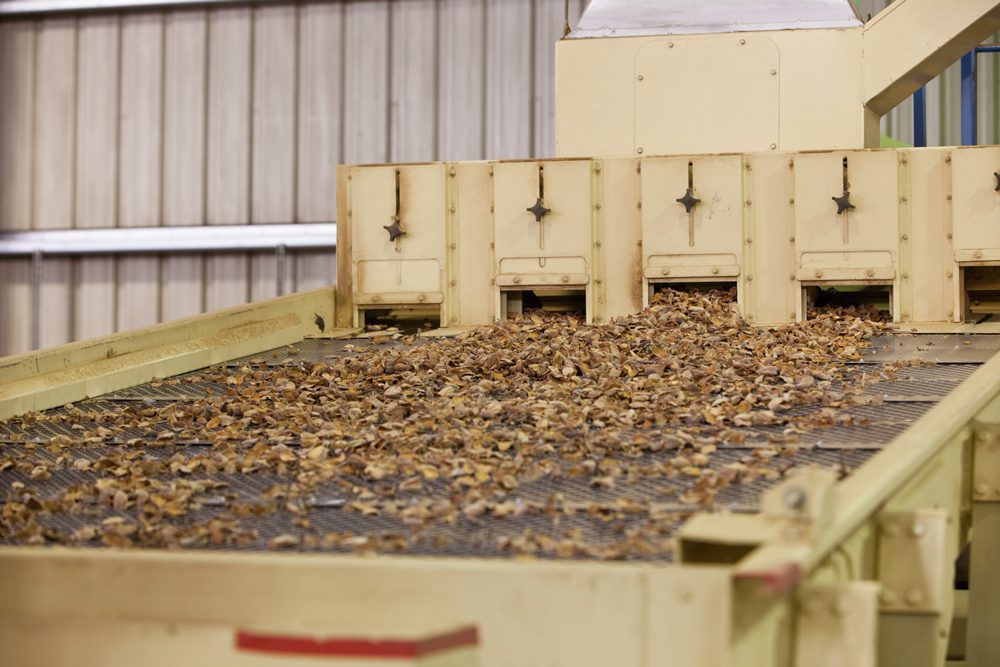
The idea of torrefaction, which involves roasting shells to remove moisture and low energy volatiles to create a new product that can be used in plastics manufacturing, is not an entirely new concept for the almond industry; however, the path toward expansion is becoming clearer.
Three years ago, the ABC Biomass Workgroup, working with the USDA Albany research team, made significant strides in developing torrefied almond shell (TAS) plastic composites and provided them to plastic pallet and slipsheet companies to make prototype products.
Though pallet manufacturing was successful, coarse particle size of TAS became a significant roadblock in the slipsheet manufacturing process. ABC has contracted Idaho National Laboratory to make a large batch of TAS-plastic composite and shell-plastic composite at a pilot scale to better mimic industrial processes, refine the economic models and provide demonstration materials to interest manufacturers.
The other torrefaction product identified by the ABC-commissioned market assessment is activated carbon used in water filtration at household, industrial and urban scales. Studies conducted by USDA-ARS researchers in Parlier, Calif. demonstrated that torrefied almond shells provided a good substrate for filtering out harmful chemical pollutants. As both California and USDA climate strategies identify the opportunity for agricultural and woody biomass utilization, torrefaction may be an area that receives public investment to further develop and attract commercial investment that will benefit the Central Valley.
Consistent Quality is Key
To take advantage of new revenue opportunities for almond coproducts, quality is key.
“Most high-value applications will demand a cleaner coproduct to start with. Contaminants have the potential to interfere with processing. Pursuing new markets will require some changes in harvesting or processing practices,” Huang said.
Use of conditioners and, eventually, off-ground harvesting will make improvements in what goes to the huller and sheller. Additionally, consistent quality may be produced through cleaner coproduct streams, including post-hulling sorting or modifications of hulling and shelling lines.
“Of course, new biomass markets will have to show increased return to growers and huller/shellers to warrant making these investments,” Huang said. “This is a central focus of the Biomass Workgroup.”