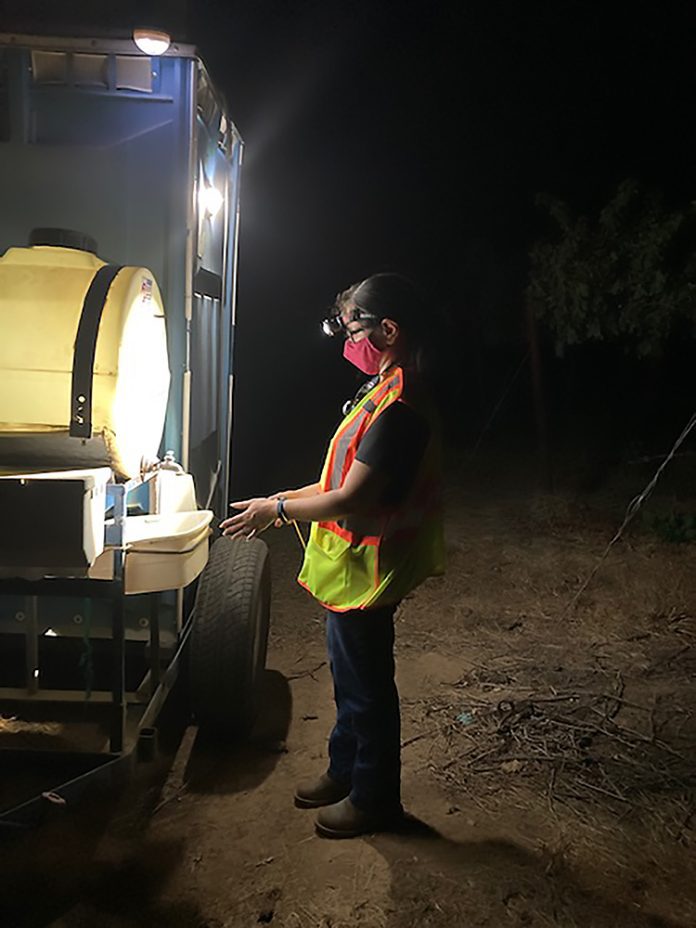
Nut harvest coincides with a time of year which can create some safety challenges for agricultural operations. During the fall months in California, our days are getting shorter and much of our state is under wildfire watch. Because of these circumstances, Cal/OSHA requires special safety measures to protect our agricultural workforce when working in the dark or in areas impacted by varying degrees of wildfire smoke. In this article, we will discuss these issues and the regulatory requirements you must know to be in compliance.
Wildfire Smoke Protection
It’s no secret that California’s dry, hot climate from spring to late fall, coupled with our recent drought conditions, create the optimal environment for wildfires to emerge across the state. In recent years, the length of the wildfire season has expanded, the fires have grown, and they are encroaching in on our fields and orchards. In 2021, there were over 8,800 fires which burned more the 2.5 million acres of land in California.
These conditions have led the Department of Industrial Relations’ (DIR) Occupational Safety and Standards Board in February 2021 to adopt a safety standard to protect outdoor workers. This regulation applies to outdoor worksites where the current Air Quality Index (AQI) for airborne particulate matter (PM) is 151 or higher, and where employers should reasonably anticipate that employees could be exposed to wildfire smoke. The following are the essential elements of the regulation and steps for implementation.
#1: Have A Plan and Reduce Exposure
As with many of the other Cal/OSHA regulations, the Wildfire Smoke Prevention Standard requires employers to develop an emergency action plan. The plan must include emergency evacuation routes for all work locations, and the plan should be communicated to your employees. It is also important to have alternate plans in place. If it is suspected that the air quality will reach the unhealthy range, consider adjusting the crew’s work schedule, move them to another worksite where the air quality is better or to an indoor worksite. A best practice would include contacting emergency services in your area. Discuss your plan details with emergency personnel, provide worksite locations and your communication plan, and ask for their input on proposed evacuation routes prior to an incident occurring.
#2: Monitor Air Quality
It is essential that the person responsible for your crews working outdoors is checking the Air Quality Index (AQI) Particulate Matter (PM) 2.5 forecast prior to the shift beginning and throughout the workday. The AQI measures the level of pollution in the air. The index ranges between 0 to 500. An AQI between 0 to 50 is good, 51 to 100 is moderate, 101 to 150 is unhealthy for sensitive groups and 151 to 200 is unhealthy. The PM measurement accounts for solid particles and liquid droplets in the air. PM 2.5 consists of fine inhalable particles, with diameters that are generally 2.5 micrometers and smaller. A measurement of 2.5 micrometers is about 30 times smaller than the diameter of a human hair.
While incredibly small, these particulates can cause damage to our hearts and lungs. The AQI measures the PM 2.5 in the air. or instance, if the AQI is at 30, then the levels of PM 2.5 are in the healthy range; however, if the AQI is 201 or more, the PM 2.5 has reached dangerous levels for people working outside. Information on the AQI and PM 2.5 specific to your area can easily be found on several websites, including U.S. EPA AirNow, U.S. Forest Service, California Air Resources Board and your local air pollution district. It is also important to note that the AQI and PM 2.5 levels will fluctuate throughout the day, usually getting worse in the afternoon hours, so it is critical that the individual responsible for the implementation of this plan checks the levels on a regular basis.
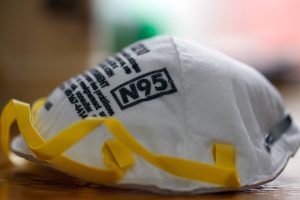
#3: Have Respirators Ready
The Wildfire Smoke Prevention Regulation requires employers provide respiratory protection equipment that filters out fine particles. Respirators must be labeled N-95, N-99, N-100, R-95, P-95, P-99 or P-100 and be approved by the U.S. National Institute for Occupational Safety and Health (NIOSH). If the AQI is 151 or higher but does not exceed 500, respirators must be made available to employees for voluntary use. If the AQI is 500 or greater, then respirators are required to be worn. As a best practice, ensure you have an ample supply of respirators in your inventory for your employees throughout the season.
#4: Train Employees
One of the most essential elements of your Wildfire Smoke Protection Plan includes training your employees. The regulation requires the following topics be covered in your training program:
- The health effects of wildfire smoke.
- The right to obtain medical treatment without fear of reprisal.
- How employees can obtain the current AQI (provide them with the website.)
- Share your two-way communication system with workers on how you will keep them updated on changing conditions.
- Provide compliant respirators, show them how to use and maintain them and encourage them to use them (they can refuse to wear one, and if someone does, there needs to be a waiver where they sign off that they were offered a respirator and declined to use it.) The employer must require employees to use respirators when the AQI for PM 2.5 is greater than 500.
- The importance, limitations and benefits of using a respirator when exposed to wildfire smoke.
- What you will do to protect them from smoke (when you will stop work, when you will move them to another location, etc.)
-
Standard lighting chart (dir.ca.gov/dosh/dosh_publications/Night-Agriculture-fs.pdf). Lighting is measured in candle feet, which defines the amount of light in a 360-degree circle from where someone is working.
Outdoor Hours of Darkness Standard
During the early fall months, nut growers, farm managers and their crews aim to start work before the sun comes up and save additional tasks for after sunset in order to beat the heat. While some level of additional lighting has been the norm during those early morning/late evening hours, as of July 2020, the State of California began enforcing a regulation that specifically governs how much lighting is required and the kinds of reflective clothing needed to protect anyone working at night in an agricultural environment.
The rule, Outdoor Agricultural Operations During Hours of Darkness standard, was developed by the California Division of Occupational Safety and Health (Cal/OSHA) with input from multiple ag industries including nut growers.
There are three specific areas within the rule that growers must be aware of:
- Lighting
- Personal protective equipment
- Training
Lighting Requirements Vary by Task
The rule includes a matrix detailing how much lighting is mandated depending upon the task. Lighting is measured in candle feet, which defines the amount of light in a 360-degree circle from where someone is working. Cal/OSHA specifies that light measurements are recorded 30 inches off the ground. For growers and applicators, some jobs may require 10 candle feet of light while some maintenance duties may specify 20 candle feet of light.
Lighting can be provided through a combination of stationary lights brought into an orchard, headlights on vehicles and personal lighting such as headlamps on hard hats.
It is highly recommended that you invest in a light meter and ensure the steps you’ve taken to mitigate this risk are working. Cal/OSHA has approved the use of light meters provided by three different companies: Davis, SPER and Extech.
Reflective Clothing a Must
The rule also requires growers to provide workers with any personal protective equipment they need when working at night. Such equipment may include hardhats with lamps and Class 2 high visibility reflective clothing such as shirts, vests and jackets.
Ensure to equip your employees with the correct PPEs as they work during hours of darkness. Any vehicles that will be used at night, such as trucks, tractors, forklifts, sweepers, ATVs and UTVs, must have proper headlights and taillights.
Nightly Safety Training Mandated
Training is a major component of the nighttime regulations. Before each work shift begins, employers are required to ensure that employees know where drinking water is stationed; what areas are designated for hand washing, rest and meal breaks, and parking; and what hazards exist (canals, irrigation equipment, roads and areas where trucks and equipment might be as well as their traffic patterns.)
Cal/OSHA has the authority to make unannounced inspections of workplaces to see if these regulations are being followed. Fines start at a few hundred dollars per violation per worker, per shift, meaning they could add up quickly for growers out of compliance.
To help growers understand and comply with these rules, AgSafe created training videos, resources and forms that are available on their website. If you need assistance with creating your safety programs, trainings or have additional questions, please contact AgSafe at safeinfo@agsafe.org or call 209-526-4400.
AgSafe is a 501c3 nonprofit providing training, education, outreach and tools in the areas of safety, labor relations, pesticide compliance and human resources for the agricultural community. Since 1991, AgSafe has educated over 100,000 employers, supervisors and workers about these critical issues.