Just when you thought California couldn’t get any tougher, the California Occupational Safety and Health Standards (Cal/OSHA) Board approved California Code of Regulation, Title 8, Section 3396 Heat Illness Prevention in Indoor Places of Employment. This standard essentially would apply to most workplaces where the indoor temperature can reach 82 degrees F. When temperatures exceed the 87-degree-F threshold, employers must implement control measures for indoor workplaces to bring the temperature down to 87 degrees F or below.
Applicability
What is considered indoors, according to the Department of Industrial Regulation, is “a space that is under a celling or overhead covering that restricts airflow and is enclosed along its entire perimeter by walls, doors, windows, dividers or other physical barriers that restricts airflow, whether open or closed.” This means most operations have at least one area where the regulation would apply. Offices, break rooms, warehouses and farm shops are all examples of indoor worksites.
This standard would apply to most workplaces. The agricultural industry, particularly facilities like hullers and processors, often require heat to process walnuts, pecans or pistachios making it difficult to bring the temperatures down. These operations make it challenging to lower temperatures effectively. Additionally, hullers, processors and farm shops are frequently small, family-owned businesses that cannot afford the costly equipment required to reduce temperatures to 87 degrees F or manage the resulting astronomical electricity bills.
Requirements
When temperatures reach 87 degrees F or a heat index of 87 degrees F, specific safety measures become necessary. This is particularly true when employees wear clothing that restricts heat dissipation or work in areas where temperatures reach 82 degrees F. Employers are required to take proactive steps to ensure worker safety, including developing and implementing safety protocols, regularly monitoring and recording temperature and heat index levels, and, in some cases, providing personal heat-protective equipment. Employers must also establish engineering controls and administrative strategies to minimize heat exposure and maintain a safe working environment.
To comply with indoor heat illness regulations, employers are required to establish one or more designated cooldown areas within the workplace. These areas must be sufficient to accommodate all employees during rest or meal periods. Cooldown areas should be equipped with appropriate cooling methods, such as fans, air conditioning, or shade, to provide effective relief from elevated temperatures.
The regulation also mandates flexibility in break schedules. If an employee begins to feel unwell due to heat exposure, employers must allow additional rest breaks as needed beyond the standard intervals. In cases where an employee shows signs of heat illness, such as dizziness, nausea, excessive sweating or confusion, employers are obligated to respond promptly by offering appropriate first aid or contacting emergency medical services, depending on the severity of the condition. Employers must also train supervisors and workers on recognizing the symptoms of heat illness and the importance of using cooldown areas.
Employers are required to implement measures to mitigate heat exposure in the workplace, starting with engineering controls. These controls are the first line of defense and involve modifying the work environment to reduce heat stress. Examples include installing and maintaining cooling equipment, such as fans, air conditioning systems or evaporative coolers.
Once all feasible engineering controls have been implemented, employers should turn to administrative controls. These controls focus on altering work practices and schedules to reduce heat exposure. For instance, employers can adjust work hours to cooler parts of the day or rotate job functions among employees if feasible.
Employers can also stagger breaks to ensure employees have sufficient time to rest and cool down without disrupting overall workflow. Establishing mandatory hydration schedules and providing clear communication about heat risks and preventive measures are other critical administrative steps. Additionally, planning for gradual acclimatization for new or returning employees can help them safely adapt to working in high-heat conditions.
Clean drinking water must always be readily available to employees, and employers are responsible for offering training on heat safety. Additionally, employers must evaluate and document environmental risk factors, such as temperature and heat index levels, while maintaining detailed records that include the date, time and location of all measurements.
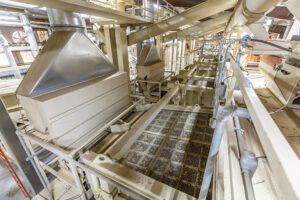
Assessment
Another requirement of the regulation is a heat illness hazard assessment of indoor areas at a worksite. Western Agricultural Processors Association has created an Indoor Heat Illness Assessment to assist the tree nut industry in complying with the indoor heat illness regulation. This assessment helps identify potential hazards, recommends engineering controls to mitigate hazardous conditions and proposes administrative controls to limit employee exposure to heat-related risks.
The assessment will also help identify specific areas within your facility where compliance with the regulation’s requirements may not be feasible. The regulation provides flexibility by allowing each facility to evaluate the feasibility of implementing the rules based on their unique circumstances. However, Cal/OSHA has not defined precise guidelines or criteria for what constitutes feasibility in each operation. Facilities can claim infeasibility under two main categories: technical infeasibility and financial infeasibility. Even if it is infeasible to bring the temperature below 87 degrees F, employers must still provide engineering controls to cool the area(s) as much as possible.
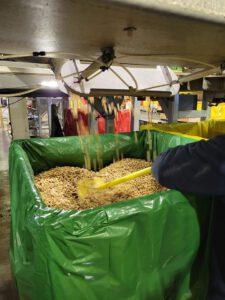
Feasibility
For financial infeasibility, there is no predetermined cost threshold, but it is essential for each facility to conduct thorough due diligence to justify their claim. This includes documenting costs associated with compliance and demonstrating that the financial burden would be unreasonable or prohibitive. Through our research, we found retrofitting hullers and processors with HVAC systems capable of maintaining cold temperatures would require significant structural modifications and equipment installation, costing millions of dollars, an expense beyond the reach of many facilities.
Technical infeasibility also poses significant challenges for many agricultural operations. Certain processes, such as drying walnuts, steam pasteurizing, or other heat-reliant activities, inherently require high temperatures to function. It is impossible to maintain the necessary heat levels for these processes while simultaneously keeping the surrounding environment below 87 degrees F. We have also found facilities like almond hullers that utilize fans that move tremendous volumes of air would not operate properly if the building was sealed shut to cool the building with air conditioning.
These challenges highlight the complexities of applying the indoor heat illness regulation to agricultural operations. The agricultural industry, already burdened with numerous regulatory and operational hurdles, now faces yet another significant obstacle.