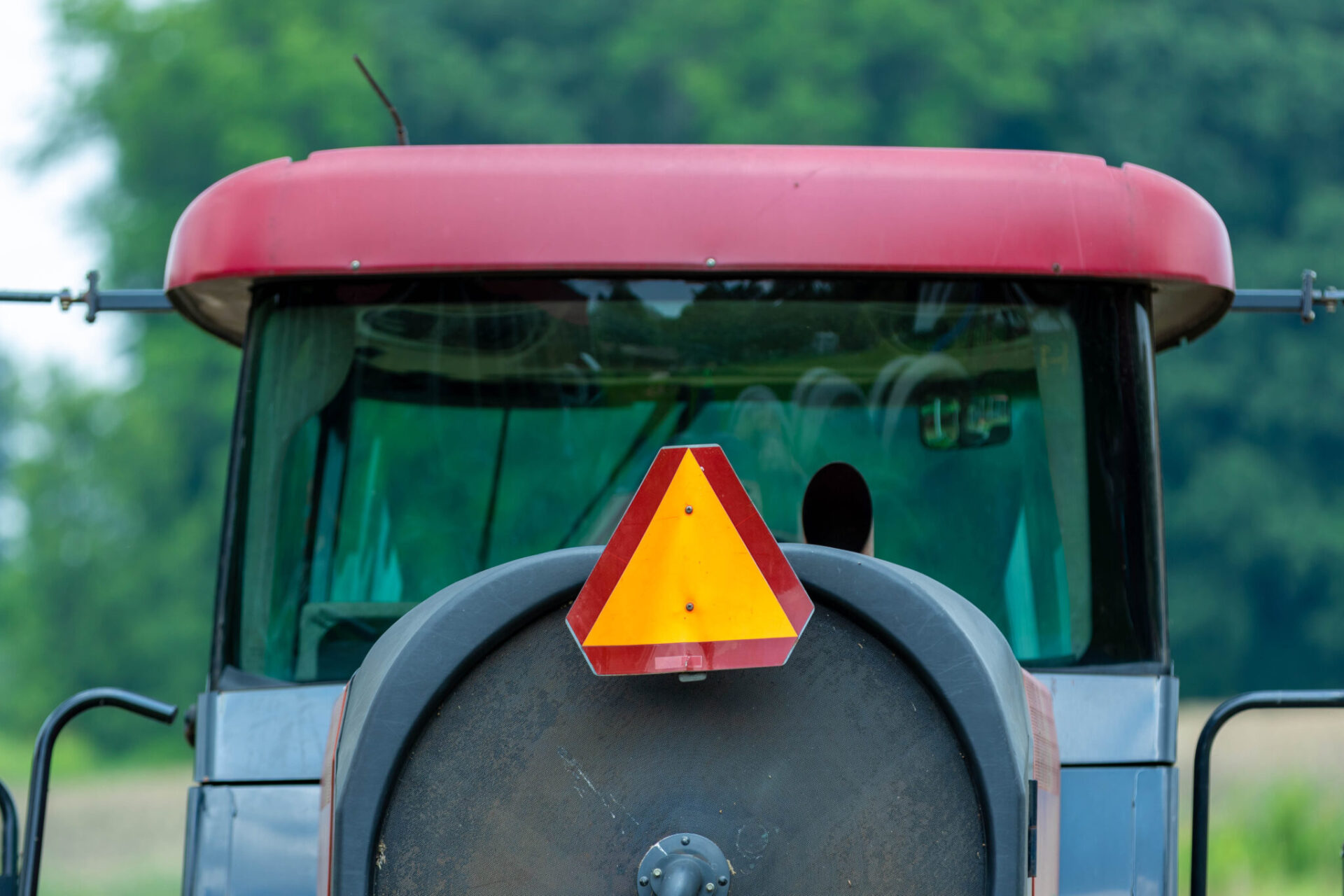
Before we know it, it will be harvest season in almond orchards. You will be timing your last pre-harvest irrigation and determining your harvest date to minimize naval orangeworm and ant damage, all while operating powerful equipment and, more importantly, keeping your employees safe in the process. As we approach the season, it’s important to think safety and understand where are employees getting hurt in the orchard? The most common injuries can be grouped into four categories: operation of equipment, ground crew hazards, moving equipment on the road and maintenance work.
Operation of Equipment
In general, the equipment used during harvest varies in size, but all of it is powerful and has the capacity to hurt someone if not operated correctly. While the size of the equipment may vary, one constant is dust. Between the dust and the low profile of some harvesting equipment, limited visibility reduces the ability to see hazards in the orchard.
So, what’s the solution? Effective training. Train your employees on all the equipment they will operate during the harvest season. Not only is this best practice, but it is a requirement under the California Code of Regulations, Title 8, Section 3441: Operation of Agricultural Equipment. Employees need to be trained annually and preferably given a refresher training prior to the harvest season.
In addition to equipment training, train employees to evaluate each orchard in which they will be working. Assessing an orchard prior to moving in equipment can help employees identify hazards. Are there electrical lines, fences not clearly marked or irrigation valves that can be easily overlooked? If those hazards exist, consider using orange cones or flags to help better identify these hazards. Assessing the orchard prior to harvest will help minimize incidents down the road.
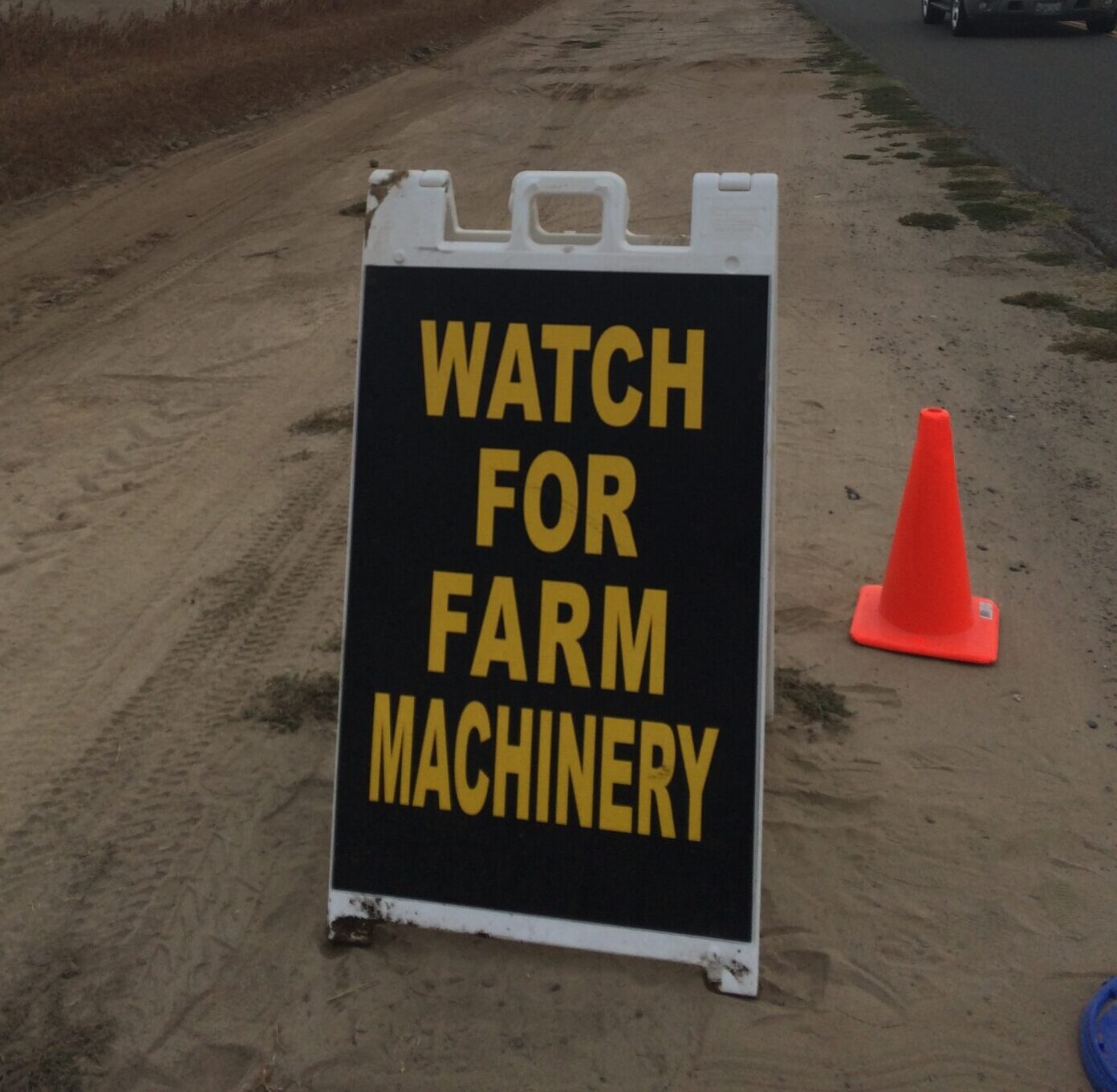
Ground Crew Hazards
Hitting an unmarked irrigation valve is one thing, but hitting a person is quite another. Employees working on the ground around heavy equipment operated by a driver with limited visibility can be a recipe for disaster. In this situation, both the equipment operators and ground crew employees should be trained in how to reduce these hazards.
In larger orchards, it is not uncommon to have multiple operators harvesting at the same time. The U.S. Department of Labor website is full of accident reports that highlight these dangers. In one particular occurrence, two employees were harvesting in the same orchard. One employee got out of the harvester to move a large branch. He hadn’t sufficiently shut down the harvester and it ran him over. The second employee attempted to help his coworker by stopping the harvester and then became pinned between it and an almond tree. Both employees lived but suffered fractures and internal injuries.
These kinds of incidents can be avoided. Operators should be trained to shut down equipment completely if they need to leave the cab and limit their distractions. For example, a no cell phone, headphone or ear buds policy is helpful. Any employees having to work on the ground during harvest should wear reflective clothing or safety vests. And, if practical, limit the number of ground workers while harvest equipment is in operation in an orchard.
Moving Equipment on the Road
As we move equipment from orchard to orchard, extra precautions need to be taken. Slow-moving vehicle signs are needed, and, in some cases, certain types of equipment are not allowed on the road and need to be hauled on a trailer. Either way, the equipment is cumbersome and not traveling at the same high speed as the cars passing by.
Some things to consider before entering a public roadway with harvest equipment:
- Always be mindful of traffic flow.
- Develop, implement and enforce policies to minimize distractions such as cell phone use and texting.
- Designate a route that is wide enough, less congested and in good condition.
- Install slow moving vehicle signs.
- Utilize a guide vehicle with lights flashing when travelling down roadways.
- Train employees on best practices for travel, especially when going to make a left turn on a main road.
Maintenance Work
It is inevitable. Harvest begins, you are under a tight timeline and your harvesting equipment breaks down. Maintenance work on equipment always comes with hazards, but those hazards become even more significant when tired employees under time constraints are performing the maintenance work.
Failure to implement lock out-tag out (LOTO) on equipment being serviced can cause entanglement, severe injury or even death. LOTO is implemented to minimize the exposure to hazards from the unexpected energization or release.
Key elements to implementing LOTO:
- Training for those that operate or use a machine on which maintenance is being performed under LOTO or work in an area in which such servicing is being performed.
- Using appropriate devices that prevent the transmission or release of energy.
- Using a tagging system that identifies the employee who has applied the LOTO device.
- Written procedures for equipment requiring LOTO.
- The same danger is presented when working around an unguarded PTO.
Why PTOs are dangerous:
- PTO shafts rotate at a very high speed.
- They make 540 to 1,000 revolutions per minute when they are at normal operating speed.
- Most PTO accidents happen when people get too close to the rotating shaft, especially if guarding has been removed or is damaged.
- Hair and loose clothing, such as a pant leg or the drawstrings from hooded sweatshirts or jackets, can get caught on the shaft and wrap around it.
- The chances of that happening increase if the shaft has small nicks, dried mud or manure on it.
- Once your hair or clothing is caught on a PTO shaft, it is nearly impossible to escape. The more you pull away, the tighter the wrap becomes.
Within fractions of a second, your hair or clothing may be torn off or your body may wrap around the spinning shaft.
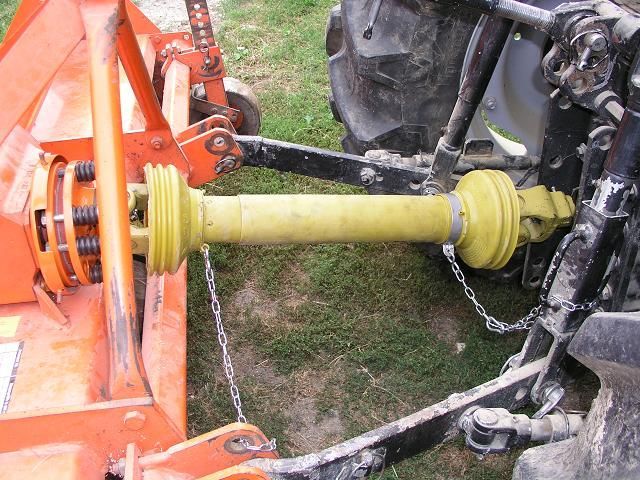
As harvest creeps upon us, keep in mind the four areas of concern: operation of equipment, ground crew hazards, moving equipment on the road and maintenance work. Training, preparation and maintained equipment are essential to a safe harvest season.
For more information about harvest safety, or any worker safety, health, human resources, labor relations or leadership development, please visit www.agsafe.org, call us at (209) 526-4400 or via email at safeinfo@agsafe.org. AgSafe is a 501c3 nonprofit providing training, education, outreach and tools in the areas of safety, labor relations, food safety and human resources for the food and farming industries.