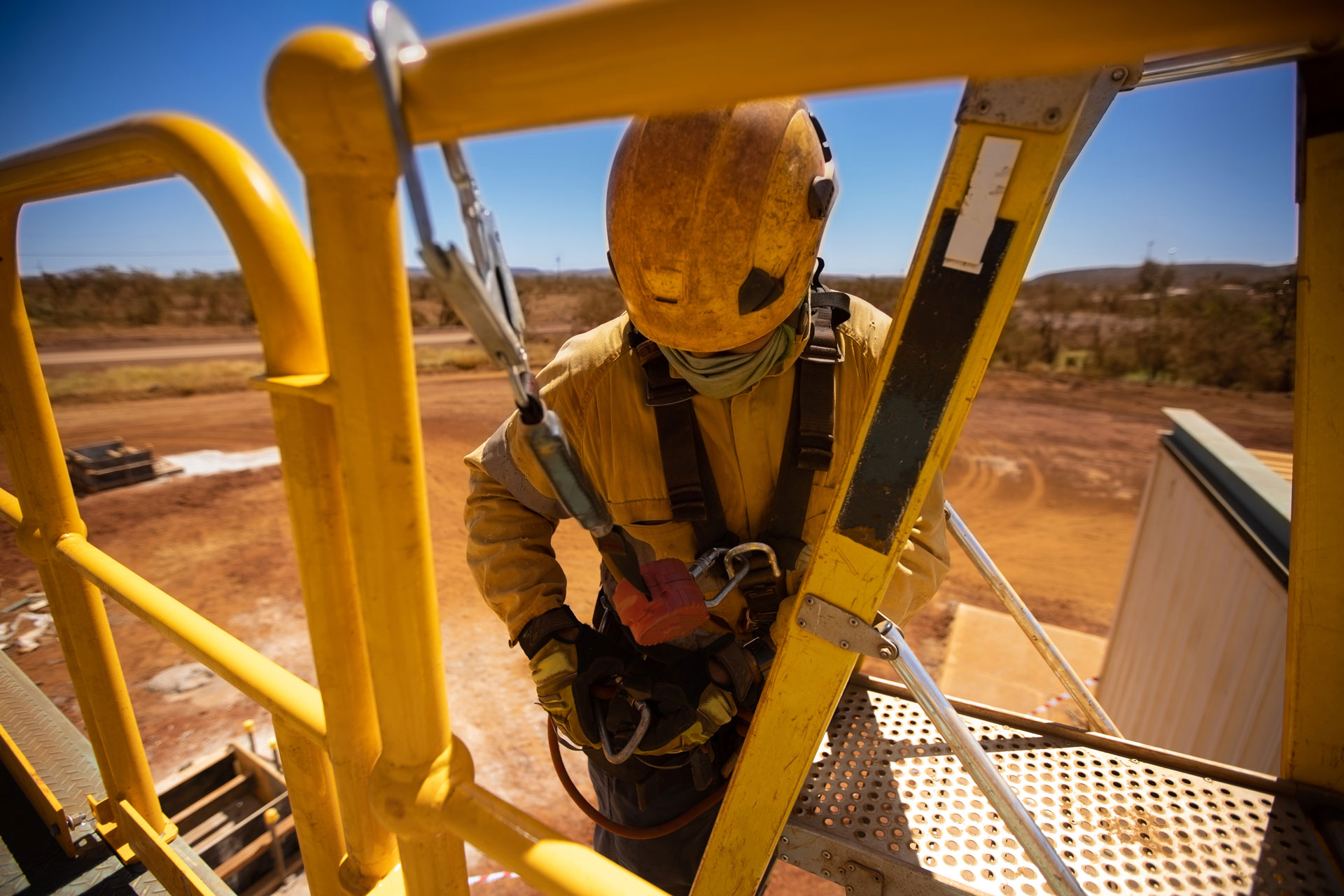
As one of many post-agricultural harvest operations, the nut hulling and processing industry continues to flourish in the state of California. The demand for this commodity has been a driving force in the growth of nut farming as well as processing facilities in the past few years. The increase of nut hulling and processing operations is accompanied by the safety challenges these employers face to keep employees safe and comply with Cal/OSHA regulations.
Like any other agriculture-related business, nut processing operations are seasonal. This characteristic brings forth the exposure to non-routine safety risks. Non-routine tasks are work tasks that are not performed on a daily or routine basis throughout the calendar year and take place during the “off season”. They occur one or two times a year and usually do not take a long period of time to complete.
They include facility maintenance and repair-related tasks that can expose employees to possible falls from heights. A few of these tasks include entering confined spaces like deep receiving or pre-cleaner pits, climbing up to baghouses located several feet above ground, and repair or adjusting of hard-to-reach parts on machinery located at above heights. In some cases, stacked bin fumigation practices may require the need for employees to climb the stacks to apply or adjust a tight-fitting tarp. Employees may access these areas through use of fixed ladders or operation of aerial lifts. These tasks may be performed infrequently (two or three times a year) and usually do not take a long period of time to complete.
Fall Hazard Assessment
The types of safety measures or controls that will need to be implemented are determined after a fall hazard safety assessment of each area where employees are exposed to above heights. This assessment is completed for the purpose of developing a required written Fall Prevention Plan that will list the applicable Cal/OSHA requirements for use of fall protection controls, present fall prevention policies, use of required personal protective equipment and employee training.
Although Cal/OSHA requires fall protection measures when employees are exposed to possible falls from 7.5 feet, regulated height triggers should not be the only factor considered while completing an assessment of fall hazards. Situations with multiple possibilities for falls to occur may call for a combination of controls that may not be required through regulation, but will have a greater effect on preventing injuries or deaths due to falls.
In situations where it is not possible to implement Fall Restraint systems (physical barriers impeding the employee from working or moving in close proximity to the edge of an above heights surface, such as guardrails, scaffolds, personal fall restraints, etc.) as control measures for fall prevention, Fall Arrest System controls must be implemented. The most common fall arrest system used in the nut hulling and processing industry is referred to as a Personal Fall Arrest System. It is comprised of a full body harness along with a lanyard, lifeline, rope grab and anchorage that can withstand a minimum weight of 5000lbs. The best way an employer can be confident that the selected parts of a personal fall arrest system will be effective in safely stopping a fall in its tracks is to fully understand each component of the system and how they work.
As Easy as A-B-C
Understanding each part and how it works can be as easy as A-B-C.
Anchorage (tie off point) must be engineered to withstand at least 5,000 lbs of dead weight and assigned a safety factor of 2. The selection and position of anchor points is crucial in the success of stopping a fall without creating additional hazards like a pendulum (swing) effect than can result in falling against adjacent structures. Another item to consider is how much time it would take for the employee to be rescued if he or she was hanging from a certain anchor point position. All anchorages must be equipped with an anchorage connector used to connect the remaining portion of the Personal Fall Arrest System.
Body Wear refers to the full body harness. This harness must be engineered and designed to withstand a total of 1,800 lbs and distribute fall arrest force onto the pelvis, thighs and across the shoulders. The harness must be equipped with a D-ring located at the back of the harness to be positioned between the wearer’s shoulder blades. The D-ring itself must be engineered to withstand a minimum of 5000 lbs and will be used to connect the harness to the anchorage point.
Connecting devices are used to connect the full body harness to the anchorage point. They can be one of the following:
Energy (Shock) absorbing lanyards will activate at up to six feet of free fall and are a flexible line securing a full-body harness to an anchorage point. They minimize the energy exerted on the wearer’s body and can provide decelerating distance from the moment the fall is initiated.
Self-Retracting lifelines are another efficient connection device that usually activates after two feet of free fall and allow for more movement horizontally or vertically.
Connection devices are equipped with snap hooks at each end, which allow for connection to the anchorage connector point and must also be engineered to withstand a minimum of 5,000 lbs. Although manufacturers of components for Personal Fall Arrest Systems may vary, they must be compatible to work together and arrest a fall successfully. Specifications for Personal Fall Arrest components may vary with applicability of Cal/OSHA regulations depending on industry and purpose for use. All components of Personal Fall Arrest Systems must be ANSI standard approved.
Do the Math
Additional evaluation that will determine the type of Fall Arrest System equipment that will be needed is the calculation of the Total Fall Distance to ensure that if a fall occurs, there is enough clearance between the wearer’s feet and level ground (3.5 feet or more) at completion of fall arrest. The most common formula used for this calculation is defined as:
TFD=FFD+DD+HEFF+VEL+SF
Total Fall Distance (TDF)
(FFD) Free Fall Distance: the distance traveled during a fall before the connecting devices, such as the shock absorbing lanyard or self-retracting lifeline, will activate and begin to arrest a fall.
(DD) Deceleration Distance: the fall distance between the activation of the fall arrest system and fall arrest completion. Required to be 3.5 feet or less and is obtained from the manufacturers label on shock absorbing capability.
(HEFF) Harness Effect: harness stretch at fall arrest is usually one foot or less and obtained from manufactures label.
(VEL) Vertical Elongation Capability: elongation of the chosen connective device at initiation of deceleration.
(SF) Safety Factor: a chosen variable that should be at least one foot.
Although the formula might seem long and complicated, knowing the definition of each variable will make it easier to understand. A competent administrator of this plan must ensure that this calculation is performed to assure accuracy in the criteria that will determine the chosen fall protection equipment employees will use.
Effective Employee Training
Like any other type of personal protective equipment, if a Personal Fall Arrest System is not utilized in the correct manner (based on company policies, training and manufacture instructions), it will not provide the intended protection. This training must be provided previous to allowing the employee to use the equipment. Employee training on use of a Personal Fall Arrest System must include the following:
Explain the purpose for use of a Personal Fall Arrest System, how it works and how it is part of the Fall Prevention Plan in place.
Provide a full description of each component of the chosen Personal Fall Arrest System.
Direction and demonstration on how to put the equipment full body harness on, adjust the straps to fit adequately and ensure that connecting devices are secured onto the anchor points.
Demonstrations of how the full body harness and connection devices are used in combination with any operated aerial lifting devices.
How to maintain and inspect the equipment. Requirements call for frequent inspections and specifications on maintaining or replacing harnesses and connection devices.
Follow all other fall prevention practices while accessing above heights areas, such as not overloading on tools while climbing up or down a fixed ladder and only exiting an aerial lift when it is absolutely necessary and additional training has been provided.
The Emergency and Rescue Plan Procedures that include use of the suspension trauma relief straps typically equipped on the full body harness.
Emergency Rescue
A well-planned Personal Fall Arrest System must include an Emergency Rescue Plan to ensure that a fallen employee is rescued as soon as possible to reduce the risk of suspension trauma. Suspension trauma can lead to death from approximately 10 to 40 minutes. It occurs from prolonged constriction of blood circulation in the legs cause by the harness straps as the employee hangs. An onsite rescue plan should include training activities with information on how to avoid post-rescue death that can occur as a result of suspension trauma, and ensuring that the fallen employee received immediate emergency medical attention.
Permit Required Confined Spaces
Use of a Fall Arrest System can be part of the safety controls established for Permit Required Confined Spaces. This is usually the case in nut hulling or processing facilities depending on the tasks that will be completed by the employee while accessing confined spaces with exposure to possible falls. Practice of all other permit required confined space controls, such as Lock Out/Tag Out or Fire Prevention measures, must also be emphasized in training activities to ensure all Cal/OSHA requirements are met and employee safety is effective.
Western Agricultural Processors Association has been assisting with development of safety plans for its members and is continuing to explore ways that it can contribute to the ongoing success of the nut industry in California. For additional information on these services, visit our website at www.agprocessors.org.