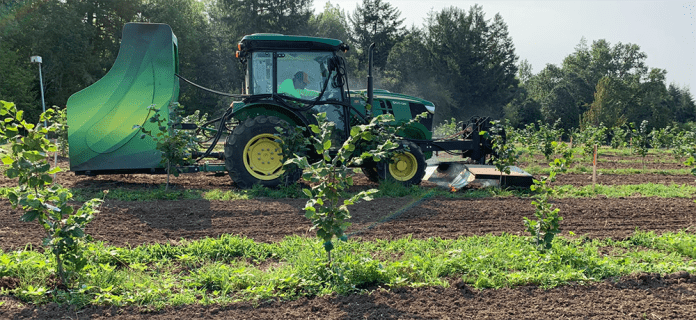
If the thought of zapping an herbicide-resistant weed with a deadly volt of electricity appeals to you, take note of recent advances in this technology.
Electric weed control involves power generated by a tractor PTO shaft to drive a generator. The generator converts mechanical energy into electrical energy that is transformed by a converter into high-voltage currents. An application unit uses electrodes to channel the current into the plant. As the high voltage passes through the plant and toward the roots, electrical resistance generates heat, leading to cell membrane rupture, causing plant death.
The technology was first patented in the 1880s, but safety limitations and agricultural applications did not evolve until the 1970s and 80s. High cost of equipment compared with the relatively low cost of herbicides plus safety issues did not encourage advancement of this technology. With an increase in herbicide resistance developing in select yet pervasive weed species worldwide being noticed by scientists, attention has returned to electric weed control.
Marcello Moretti, Oregon State University weed scientist, OSU grad student James Wirth and Cornell University weed science researcher Lynn Sosnoskie have been testing electric weed control applications with emphasis on orchard weed management. Wirth said for the last two years, they have been working with Switzerland- and Brazil-based Zasso electric weed control equipment testing in hazelnut orchards.
Zasso’s system has insulated cables containing braided copper wires running from the transformer unit to two 2-foot-wide applicators mounted on the front of the tractor. These channel the high-voltage electricity through two sets of metal electrodes in each applicator, separated by about 1.5 feet. The first set acts as a positive electrode and the second set acts as a negative electrode. That means the electricity flows through the first set into plants it comes in contact with, through the roots, and into the soil where the second set of electrodes close the circuit by absorbing the energy again. Wirth said after intensive use, carbonization can be seen on the electrodes, but there is no hard evidence that this decreases efficacy. He said the parts are relatively cheap to replace from local machine shops and are the heaviest sign of wear and tear they’ve experienced, now three years into use.
Management Tool
Wirth confirmed this weed management tool has broad applications on different weed species, including yellow nut sedge, amaranth, field bindweed and horsetail. Stage of weed development, type of root system, population density and water status were listed as sources of resistance to electrical current, but Wirth noted in trials with mature, dense weed stands, they were impressed by the efficacy of machinery in killing grassy weeds. He said they also looked at seed viability after the electric treatment to determine the effect. The more woody tissue in a plant, the higher the resistance to electrical current.
The OSU trials were conducted with a 100 hp tractor, not the optimal power, Wirth said, but it was adequate. They found for higher connectivity to the soils that cool, dry and sandy soils were ideal for electrical dispersal. In heavier soils, the applicators are not able to generate enough power.
OSU trials were conducted with the minimum-horsepower tractor. A UC Weed Science publication noted an electric weed control trial using 5,000 to 12,000 volts on a 75 hp tractor was effective on both annual and perennial weeds.
In the trials, there were concerns with the effect of the electric charge on hazelnut trees. It is common for suckers to grow from the base of the tree, and as the applicators pass, the suckers could be zapped and the charge could be channeled to the tree. No significant issues with this have surfaced, Wirth said.
Two-foot and four-foot applicator heads were tested at OSU, but Wirth said applicator size can be customized to fit management needs. They have also been testing different heights and different speeds.
“At four miles per hour, we have been getting four to six weeks of bare ground with smaller weeds,” Wirth said.
Sosnoskie, formerly with UC Davis, is optimistic about the future of electric weed control. She said studies have been conducted to evaluate the impacts of both generator setting and tractor travel speed on weed control. These trials are also evaluating the safety of the technology with respect to soil microarthropods and soil microbes. She noted while data is still being collected, the preliminary work from 2022 saw no negative impacts. Trials are being done in apple orchards comparing this technique to cultivation.
Not Complete Solution
Moretti noted mowing and tillage are not complete solutions for weed control in all tree nut orchards due to management and harvest practices. Electric weed control, Wirth said, is not a complete replacement for tillage, mowing or herbicides.
“Electric weed control can be easily integrated into a weed management program targeting resistant weeds. I see it as a supplemental control measure,” Wirth said.
Herbicide-resistant weeds are a global problem, Moretti said, and tree nut species all have similar issues with weeds. They can reduce irrigation efficiency, harbor vertebrate pests and interfere with harvest of nuts that are placed on the ground to dry. Moretti’s USDA funded research focused on herbicide-resistant Italian ryegrass in hazelnut orchards, but he noted other tree nuts have similar issues with herbicide-resistant weeds. As of 2021, there are 13 weed species commonly found in almond orchards throughout the California Central Valley. Each of these weeds have had confirmed cases of herbicide-resistant biotypes in California.
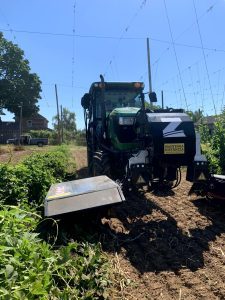
Companies Invested in EWC
Moretti said there has been investment in electric weed control technology with at least three companies producing machinery. Zasso’s Electroherb weed control technology is based on a mature, non-selective electrophysical mode of action. Its application uses dynamic adjustment of the high-voltage power being discharged to the targeted plants via a closed, uniform and directed electrical circuit. Morretti has been using this technology in his research.
UK-based Root Wave has RootWave Pro, a handheld weeder designed for spot weeding and treating invasive species. Each weed must be touched by the electrode for the electricity to flow; the natural resistance means the weed rapidly heats up killing both root and stem. To use this tool, a generator is required along with Respirex Dielectric boots that are mandatory for the operator.
Based in Germany, crop.zone also uses electrical current to shock weeds plants. The equipment mounts to tractors and consists of a front-mounted boom sprayer and a rear PTO-mounted generator and applicator boom. The front sprayer deposits a nitrogen- and phosphate-free mineral solution called volt.fuel to enhance conductivity, while the rear boom trails surface contact applicator plates that expose the plants to a potential of between 2,000 to 5,000 volts. The volt.fuel liquid bridges leaf hairs and irregularities on leaf surfaces and softens the plant’s surface wax layer to increase electrical conductivity and lower power consumption.
Cost per acre for electric weed control, not involving cost of the machinery, is comparable to other orchard machinery operations. Fuel use is similar to the electric applicator. Machine maintenance at the OSU trials was minimal, Wirth said, with only the metal fingers in the applicator needing replacement.
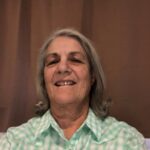
Cecilia Parsons | Associate Editor
Cecilia Parsons has lived in the Central Valley community of Ducor since 1976, covering agriculture for numerous agricultural publications over the years. She has found and nurtured many wonderful and helpful contacts in the ag community, including the UCCE advisors, allowing for news coverage that focuses on the basics of food production.
She is always on the search for new ag topics that can help growers and processors in the San Joaquin Valley improve their bottom line.
In her free time, Cecilia rides her horse, Holly in ranch versatility shows and raises registered Shetland sheep which she exhibits at county and state fairs during the summer.