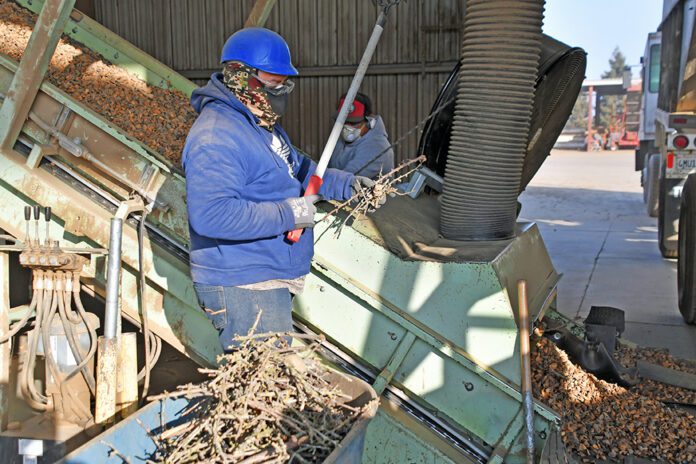
To condition or not to condition?
That is the question many almond growers face at harvest, and their decision ultimately may affect hullers and shellers.
Some almond producers have never used the practice, while others have eliminated it to reduce costs in the current low-price nut market. Proponents, on the other hand, say conditioning speeds harvest, allows them to deliver a cleaner and better-quality crop to huller-shellers, and actually saves money.
The practice involves running a conditioner through the windrow created by sweeping to screen out dirt, rocks, leaves and sticks. It finishes by laying an even layer of mostly almonds on the orchard floor and depositing the collected debris at the end of the row.
Huller-shellers like conditioning because it improves unloading, aids quality and reduces the amount of debris they have to dispose of. In fact, many hullers and shellers have started charging based on field weight as an incentive for growers to deliver cleaner product. Others have invested in additional machinery to handle foreign material at the huller.
Even if growers don’t condition their crop, huller-shellers say using something like a de-sticker goes a long way to remove extraneous material.
To try to provide direction for growers, the Almond Alliance’s Grower Committee has been tasked with looking at conditioning, said Kelli Evans, who chairs the committee and also farms almonds with her family near Live Oak.
“How would this affect their bottom line and how could this save them money?” she said.
Committee members plan to review information from manufacturers, large processors such as Blue Diamond, huller-shellers and UC, among other sources.
Big Sticks a Problem
Most of the current conditioning issues deal with larger sticks, and the problem appears more prevalent in older orchards that haven’t been pruned for several years, said Mel Machado, Blue Diamond vice president of member relations. At one time, smaller woody chips left over after shredding orchard prunings were a major issue.
If the material was shredded too late in the season or wasn’t shredded finely enough, it didn’t have time to decompose and would be picked up during harvest along with the nuts.
Citing long-term research, UC began encouraging growers several years ago to move away from annual orchard pruning after the first few years of training and shaping trees. That has gone a long way to reducing the small woody pieces that made their way into the huller, Machado said.
Delivering a Better-Quality Crop
Evans herself is a proponent of conditioning. Her family adopted the practice about three to four years ago after her father conducted an informal trial that compared conditioning with no treatment. While Evans doesn’t have hard numbers, she said pick-up was much faster after conditioning and she believed they deliver a better quality product.
“I feel like the product is easier for them to hull and shell,” she said. “There are less chips. Every one of those things adds up.”
In addition, Evans said they saw less wear and tear on their pick-up machines.
Machado said conditioning also may speed drying on the orchard floor by up to three days, depending on weather conditions. It does so by taking the nuts in the windrow, removing extraneous material and depositing mostly nuts in an even layer over a wider area in the row middle.
Early in harvest, such as in August or September, he said the improvement in drying may not be that much. But in October, the difference “could be worth quite a bit,” he said.
Conditioning also complements the push for early harvest, which is designed to get nuts off the trees in a timely fashion and reduce their exposure to insect pests, Machado said. The trade off may be growers shake nuts at slightly higher moisture levels.
Come harvest, Machado said he believed conditioning also is beneficial.
“I believe the net cost still comes out a positive,” he said. “Growers will tell you, ‘This is goofy. You have another pass with a machine.’”
Hypothetically, he said it may cost $200 per hour to run a conditioner. A harvester, on the other hand, may cost $450 to $500 per hour to operate.
“I’d rather slow down a $200 machine than a $500 machine,” he said. “Now [after conditioning] that $500 machine runs faster and more efficiently.”
Flory Industries recently conducted a study that looked at the benefits of conditioning for a 250-acre producer who uses custom harvesting. Turnout improved to 25% compared to 20% for the non-conditioned nuts. Truckloads decreased to 46 for the conditioned crop compared to 58 for the non-conditioned. Over one season, Flory found a savings of $4,610. That grew to $23,050 over five years.
For a large-scale producer with 2,500 acres and who owned equipment, Flory found savings ranged from $139,700 for one year and $698,500 over five years. The actual benefits will vary based on several factors, including yield, orchard age, orchard floor management, quality premiums and equipment financing costs, to name a few.
More Than Just Cost Savings
For the first time, Donny Hicks, who farms near Hughson, hired Mike Colombo of Colombo Ag Services to custom condition his crop last year to address concerns about navel orangeworm. Hicks liked the end result so much that he said he planned to continue doing it.
Normally, it would take about nine hours to harvest his orchards. Last year, it took only about six hours after conditioning.
Because Hicks is a smaller-scale grower, he does most of the field work himself. Having the conditioner stop just before the end of the row provided a turning space for the harvester. It also meant that Hicks didn’t have to rake nuts to create that turning area.
“An added benefit for me is it saved me about four hours of raking work,” he said.
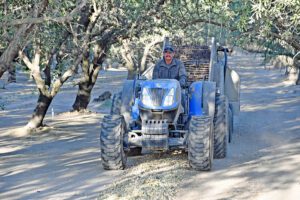
unwanted material and laying the almonds in a flat layer on the orchard floor.
Depending on weather, conditioning may speed drying by up to three days.
In addition, Hicks said he was able to deliver a cleaner quality crop to the huller-sheller, and his grade sheets reflected that. For his Independence, he had a 37% turnout.
“That’s crazy,” Hicks said. “Independence in the 30s is pretty phenomenal.”
Huller Equipment Diverts Sticks
Parreira Almond Processing Co. in Los Banos is among the huller-shellers that have started charging based on field weight to incentivize growers to deliver a cleaner crop, said David Parreira, managing partner.
The Los Banos facility also installed a Slipstick conveyor instead of an auger to feed elevators that feed its pre-cleaner to address larger sticks. Many of the new elevators used to load semis as the nuts come out of orchards also have built-in de-stickers, which have helped.
“Obviously, there’s still some sticks, particularly in the older blocks,” he said. “With our receiver pits with the Slipstick, now we’ve been able to get a lot of it out. We used to be tearing up belts and buckets on the bucket elevator. Getting rid of big rocks is another real benefit.”
In the past, Parreira Almond used to burn the woody material diverted from incoming nuts. To comply with current San Joaquin Valley Air Pollution Control Board regulations, the Los Banos operation installed an air curtain burner more than two years ago. It uses super-heated temperatures and a secondary burn chamber to ignite woody material and significantly reduce emissions.
Parreira Almond has used the Air Board-permitted burner for the past two seasons, and Parreira said, “It worked out tremendously.”
Garrett Howser, who operates Howser Almond Shelling near Modesto with his father, Dan, has mostly smaller-scale customers, many with older orchards. To handle the large influx of sticks and other material, Howser designed and fabricated a belt system to remove much of the foreign material before the field-run nuts go into a pre-cleaner. He based his design on equipment he’d seen in the mining industry and adapted it to hulling and shelling.
Howser said he saw the need after watching his crew spend time removing sticks and other material as they unloaded trailers before the nuts dropped into the pit.
“All I saw was my added waste and labor, and that doesn’t pay the bills,” he said. “This speeds the pre-cleaner up faster than I thought it would.”
2023 was the first year they used the new system, and Howser said it worked well overall. With last season’s smaller crop, he said there seemed to be a higher ratio of foreign material to nuts.
Because they built the system themselves, Howser said he didn’t have exact break-even costs. But he said it should pay for itself in no more than two seasons. It’s already increased capacity by 25% while decreasing labor.