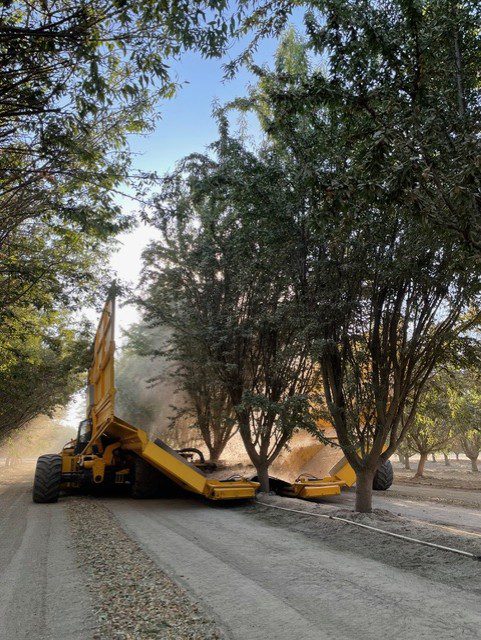
Sun and ambient air have been known as the most efficient drying method for almonds since the first commercial crops were planted in California. While the industry is looking at changing this standard harvest routine, there are signs growers are adapting.
Declaring a goal of 50% reduction in harvest-generated dust by 2025, along with listing numerous advantages of keeping nuts off the ground, Almond Board of California (ABC) has funded research to investigate and solve issues with off-ground harvest. Investments have also been made by harvest machine manufacturers to meet the challenge of off-ground harvest.
Sebastian Saa, director of agricultural research at ABC, emphasized the positives to off-ground harvest in addition to dust reduction, including reduction of water stress in late harvest varieties, less herbicide use, less insect damage and improvements in soil health among others.
An off-ground harvest panel at the 2019 Almond Conference noted harvest can potentially begin earlier, cutting down on insect damage. Nuts that do not hit the ground escape ant damage. Cleaner loads can be delivered to hullers. Dust generated by sweeping nuts into windrows is eliminated. A single pass uses less labor and fuel. Growers would have more flexibility with irrigation scheduling, and there reportedly is less need for orchard floor preparation.
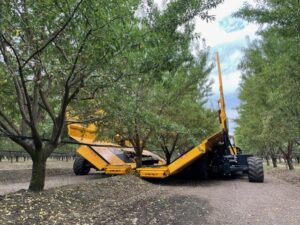
No Single Solution
Progress toward off-ground almond harvest is being made, but industry leaders agree there isn’t a single solution for every orchard. Mel Machado, vice president of grower relations for Blue Diamond, said while there is plenty of interest in off-ground harvest, the challenges to widespread adoption in the near future are many.
“Not in all orchards, and not every year will it work,’’ Machado said, citing concerns in the north with losing crop to windfalls with off-ground harvest. Orchard design may need changes.
Machado noted he has witnessed off-ground harvest operations and reported the machinery did a good job.
Almond grower Brian Wahlbrink said that the biggest hurdle he sees for widespread adoption of off-ground harvest currently is the cost. Extra handling, drying and equipment are tough to take on when growers may just be in survival mode due to low almond prices.
“The concept is great, but until there are financial benefits, it is hard to move forward,” he said.
One segment of the almond industry where off-ground harvest really makes sense is organic, Wahlbrink said. Off-ground harvest would circumvent the problem of weed management, a significant cost in organic production.
Tom Thomas, sales manager with OMC, said every year there is more interest in using off-ground harvest equipment. The Yuba City-based equipment manufacturer has done demonstrations of off-ground harvest equipment in recent years, and Thomas said they will be doing about 600 acres this year for a grower using pistachio harvesting-type catch frames. The nuts will go into a cart and be moved to another site for drying.
“Those growers are thinking about the future and want to reduce dust, but complications remain,” Thomas said, referring to drying methods.
Drying the nuts and the extra handling costs when stockpiling or spreading the nuts to dry at another location are current deterrents to adoption. Wahlbrink noted unloading green hulls can be challenging.
Scott Hermann from TOL in Tulare confirmed there are a few forward-thinking almond growers who are making the move to full off-ground harvest each year. Those choices depend on having an economical drying method.
“I was told by one that they saved $300 an acre with off-ground by saving pesticide and herbicide spray costs,” Hermann said. “There are people out there who see the potential in full off-ground, but they are in the minority right now. It makes sense, but not until the drying issue is resolved.”
Hermann said the cost estimate for drying nuts off-ground is a minimum of 8 cents per pound depending on the heat source. Growers will have to decide if they can save enough on sweep, condition and harvest passes, plus potential savings on reducing pesticide and herbicide sprays to make it a break-even proposition.
TOL’s Twin D has a catch frame and can put the nuts in a cart or in a windrow. It will fit in most orchards. Earlier harvest is possible, Hermann said, but that needs to be better understood.
Drying the nuts offsite has been identified as a major issue with off-ground harvest. ABC-funded research on drying techniques highlighted the challenge. Stockpile drying using wind and hot air drying in trailers were studied. UC Davis researcher Zhongli Pan reported at the 2019 Almond Conference the recommended drying process is using stepwise drying with minimum temperature of 140 degrees F to achieve high drying throughput with reduced energy costs.
While stockpiling and using forced hot air adds to almond processing costs, Pan said off-ground drying can validate the significance in reduction of insect damage, resulting in less rejections and higher-quality kernels and hulls. There remains the extra time and cost for stockpiling and delivery to a huller.
Another drying tactic cited by Hermann involved a UC Merced drying trial involved stockpiling over an air duct and sucking the ambient air from the bottom of stockpiles of almonds as a method of drying.
Then, there are tradeoffs. A hybrid of off-ground harvest is gaining traction. Hermann said the TOL machine can shake, catch and then drop the almonds in a windrow in the orchard for drying. The machine removes sticks and leaves, leaving a clean windrow that does not need conditioning. For those who want to move the nuts out of the orchard, there is a cart that can be connected to the harvester to haul the nuts out of the orchard for drying off-site.
Running a Conditioner is an Option
Billy Schuh, a west Fresno County almond grower, said growers and custom harvesters have been adopting harvest changes that help with the goal of dust reduction but are not yet embracing full off-ground harvest. Use of a conditioner on windrows to sift out dirt and debris is one of the biggest harvest moves. Running a conditioner adds another pass through the orchard, but turnout is improved as less dirt, rocks and stick arrives at the huller.
Not every grower wants to pay for that extra pass through the orchard to clean up windrows, Schuh said, but it can pay off when they aren’t penalized for low turnout.
Schuh said harvest pick-up machines have been modified to reduce the amount of dirt picked up with the nuts, helping to deliver cleaner loads. It is hard to beat the free drying done by the sun, he added.
Wahlbrink said just managing the 4 to 6 feet in the middles to lay the windrows makes sense with the hybrid harvest model. Dry and clean ground allows for better drying and the tree row soil benefits from a ground cover.